Graphene production, like many advanced material manufacturing processes, has environmental implications that need to be carefully considered. While graphene itself is a revolutionary material with potential benefits in energy storage, electronics, and water purification, its production methods can have varying degrees of environmental impact. The primary concerns include the use of toxic chemicals, high energy consumption, and waste generation. However, advancements in sustainable production techniques, such as green chemistry approaches and renewable energy integration, are being developed to mitigate these impacts. The environmental footprint of graphene production largely depends on the specific method used, with some processes being more eco-friendly than others.
Key Points Explained:
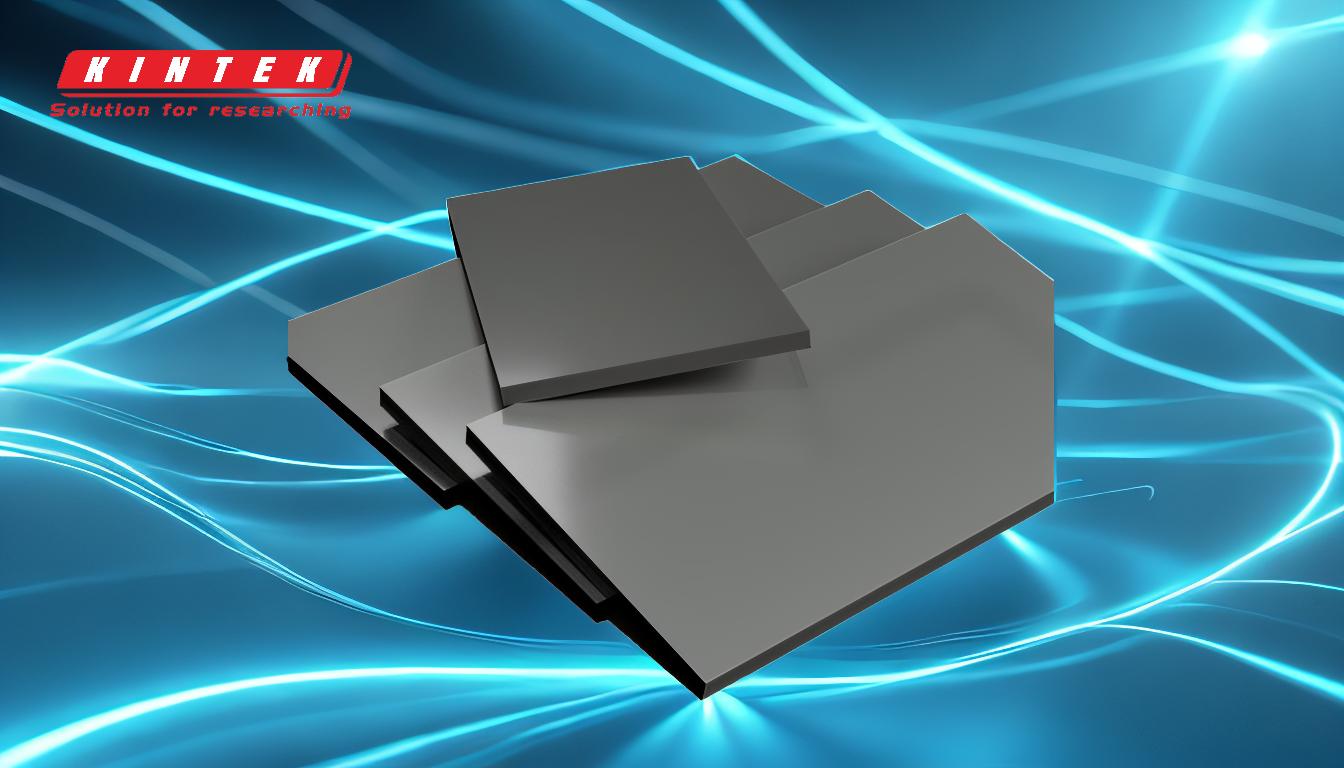
-
Production Methods and Their Environmental Impact:
- Chemical Vapor Deposition (CVD): This is one of the most common methods for producing high-quality graphene. However, it involves high temperatures and the use of gases like methane, which can contribute to greenhouse gas emissions. The process also requires significant energy, often derived from non-renewable sources.
- Exfoliation Techniques: Mechanical exfoliation and chemical exfoliation are other methods. Chemical exfoliation, in particular, often involves the use of strong acids and oxidants, which can lead to hazardous waste and require careful disposal.
- Green Chemistry Approaches: Researchers are developing more sustainable methods, such as using bio-based materials or water as solvents, to reduce the environmental impact. These methods aim to minimize the use of toxic chemicals and lower energy consumption.
-
Energy Consumption:
- The production of graphene, especially through methods like CVD, is energy-intensive. The high temperatures required for these processes often rely on fossil fuels, contributing to carbon emissions.
- However, integrating renewable energy sources into the production process can significantly reduce the carbon footprint. For example, using solar or wind energy to power graphene production facilities can make the process more sustainable.
-
Waste Generation and Management:
- Graphene production can generate hazardous waste, particularly when chemical exfoliation methods are used. The disposal of this waste must be carefully managed to prevent environmental contamination.
- Advances in recycling and waste management techniques are being explored to mitigate this issue. For instance, some researchers are working on ways to recycle the solvents and chemicals used in graphene production, reducing the overall waste generated.
-
Potential Environmental Benefits of Graphene:
- Despite the environmental challenges in its production, graphene has the potential to offer significant environmental benefits. For example, graphene-based materials can improve the efficiency of energy storage systems, such as batteries and supercapacitors, leading to reduced energy consumption and lower greenhouse gas emissions.
- Graphene can also be used in water purification systems, helping to remove pollutants and improve water quality, which can have positive environmental impacts.
-
Future Directions and Sustainability:
- Ongoing research is focused on developing more sustainable graphene production methods. This includes exploring alternative raw materials, optimizing production processes to reduce energy consumption, and improving waste management practices.
- The development of industry standards and regulations can also play a crucial role in ensuring that graphene production is conducted in an environmentally responsible manner.
In conclusion, while graphene production does have environmental challenges, particularly in terms of energy consumption and waste generation, there are ongoing efforts to make the process more sustainable. The potential environmental benefits of graphene, combined with advancements in green production techniques, suggest that the overall impact can be mitigated. As the technology matures, it is likely that graphene production will become more eco-friendly, aligning with broader sustainability goals.
Summary Table:
Aspect | Details |
---|---|
Production Methods | - Chemical Vapor Deposition (CVD): High energy, greenhouse gas emissions. |
- Exfoliation Techniques: Chemical exfoliation generates hazardous waste. | |
- Green Chemistry: Sustainable methods using bio-based materials. | |
Energy Consumption | - High energy use, often from fossil fuels. |
- Renewable energy integration reduces carbon footprint. | |
Waste Management | - Hazardous waste from chemical exfoliation. |
- Advances in recycling and waste management. | |
Environmental Benefits | - Improves energy storage efficiency. |
- Enhances water purification systems. | |
Future Directions | - Sustainable methods, alternative materials, and optimized processes. |
Learn how sustainable graphene production can benefit your industry—contact our experts today!