Hot isostatic pressing (HIP) is a specialized manufacturing process that enhances material properties by applying high temperature and pressure uniformly to components. While it offers significant benefits such as improved wear resistance, corrosion resistance, and mechanical performance, it is generally considered an expensive process due to the advanced equipment, precise control systems, and energy-intensive operations required. Warm isostatic pressing, a related but less intensive process, operates at lower temperatures and may offer a more cost-effective alternative for certain applications. Below, we explore the factors contributing to the cost of hot isostatic pressing and compare it with warm isostatic pressing.
Key Points Explained:
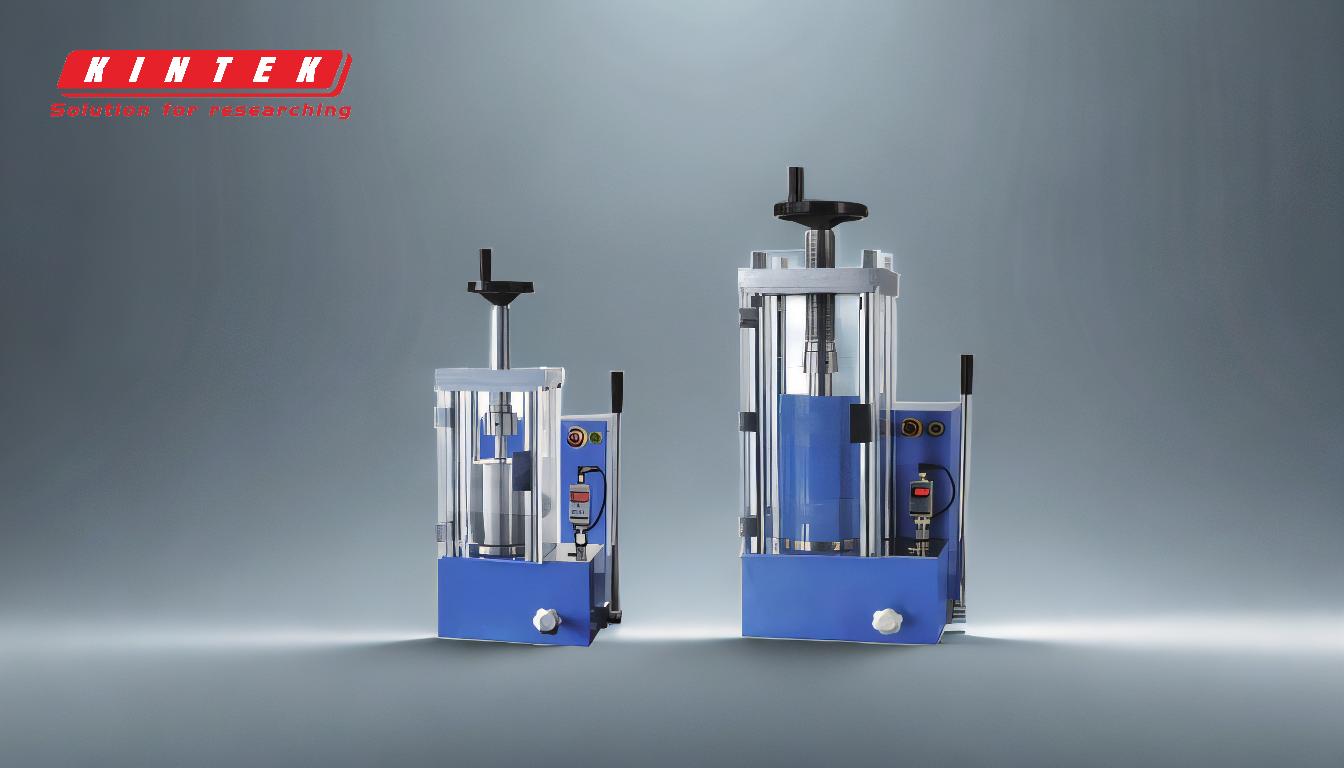
-
Equipment and Operational Costs:
- Advanced Equipment: Hot isostatic pressing requires sophisticated equipment, including high-pressure chambers, heating systems, and computer-controlled systems. These components are expensive to manufacture and maintain.
- Energy Consumption: The process involves heating materials to high temperatures (often exceeding 1000°C) and applying high pressure, which consumes significant amounts of energy, contributing to operational costs.
- Precision Control: Computers are used to program and control the temperature ramp-up, pressure, and process time, ensuring consistent and high-quality results. This level of precision adds to the overall cost.
-
Material Benefits vs. Cost:
- Enhanced Properties: HIP improves material properties such as wear resistance, corrosion resistance, and mechanical performance. It can increase fatigue life by 10 to 100 times and achieve material densities close to theoretical values. These benefits often justify the higher costs for critical applications in industries like aerospace, medical, and energy.
- Cost-Effectiveness for High-Performance Applications: While HIP is expensive, the long-term benefits, such as extended component life and reduced maintenance, can offset the initial investment in certain high-performance applications.
-
Comparison with Warm Isostatic Pressing:
- Lower Temperature and Pressure: Warm isostatic pressing operates at temperatures no higher than the boiling point of the liquid medium, typically using hydraulic pressure and flexible envelope dies. This reduces energy consumption and equipment complexity, making it a more cost-effective option for less demanding applications.
- Application Suitability: Warm isostatic pressing is suitable for forming and pressing powder materials where the extreme conditions of HIP are not required. It is often used in industries where cost savings are prioritized over the need for ultra-high material performance.
-
Industry-Specific Considerations:
- Aerospace and Medical Industries: These sectors often require the superior material properties achieved through HIP, making the process cost-effective despite its high price tag.
- General Manufacturing: For applications where material performance requirements are less stringent, warm isostatic pressing or other alternative processes may be more economical.
In summary, hot isostatic pressing is an expensive process due to its advanced equipment, high energy consumption, and precision control requirements. However, its ability to significantly enhance material properties makes it a valuable investment for high-performance applications. Warm isostatic pressing offers a more cost-effective alternative for less demanding applications, balancing performance and cost.
Summary Table:
Aspect | Hot Isostatic Pressing (HIP) | Warm Isostatic Pressing |
---|---|---|
Temperature | High (often >1000°C) | Lower (up to liquid medium boiling point) |
Pressure | High | Moderate (hydraulic pressure) |
Energy Consumption | High | Lower |
Equipment Complexity | Advanced (high-pressure chambers, heating systems, computer-controlled systems) | Less complex (flexible envelope dies, hydraulic systems) |
Cost | Expensive | More cost-effective |
Applications | Aerospace, medical, energy (high-performance needs) | General manufacturing (less demanding applications) |
Material Benefits | Improved wear resistance, corrosion resistance, mechanical performance, extended fatigue life | Suitable for forming and pressing powder materials |
Interested in optimizing your manufacturing process? Contact us today to explore the best isostatic pressing solution for your needs!