When deciding whether to weld or braze aluminum, the choice depends on the specific application, material properties, and desired outcomes. Brazing aluminum, particularly vacuum aluminum brazing, offers distinct advantages such as clean joints, minimal distortion, and the ability to join dissimilar materials. Welding, on the other hand, is typically stronger but can introduce heat-related challenges like distortion and requires more skill. Both methods have their merits, but brazing is often preferred for its versatility, repeatability, and suitability for complex assemblies.
Key Points Explained:
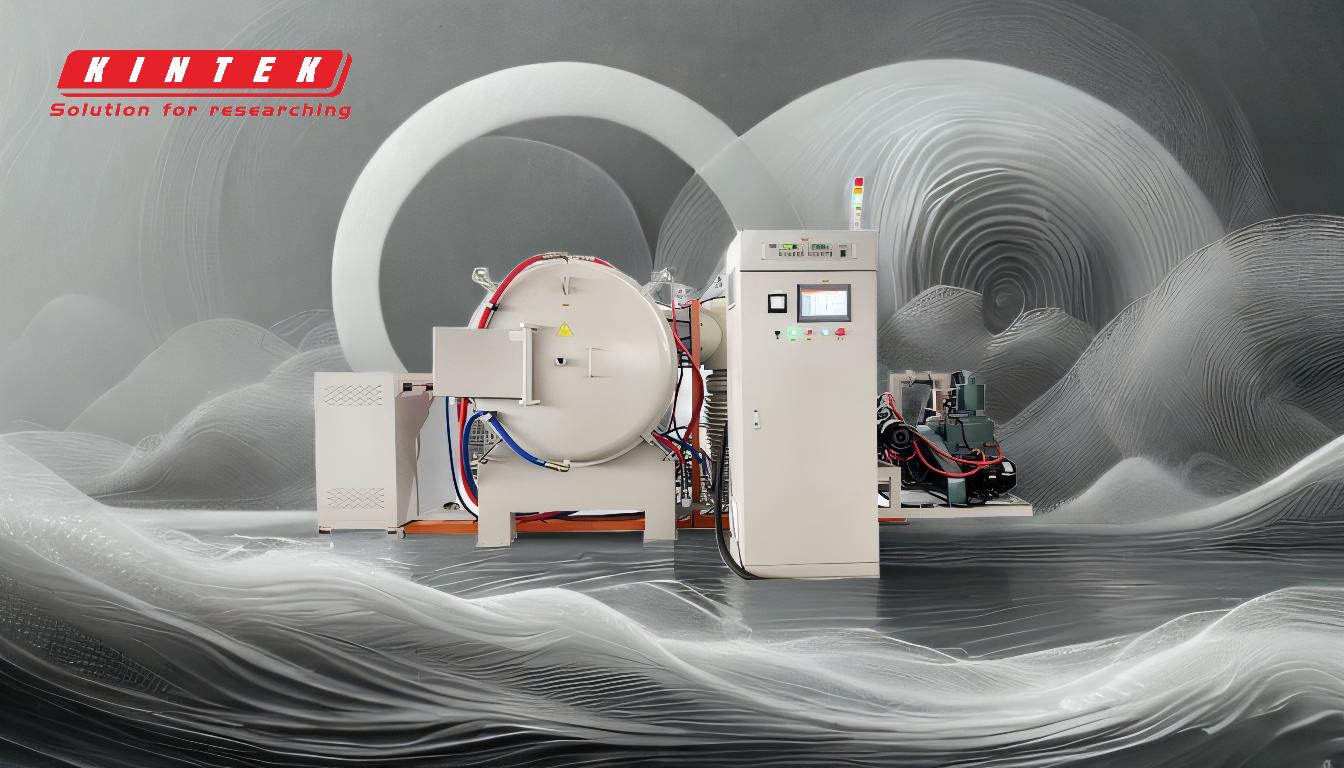
-
Advantages of Vacuum Aluminum Brazing:
- Clean Joints: Vacuum aluminum brazing produces joints without the need for additional finishing, making it ideal for applications requiring a high-quality surface finish.
- Minimal Distortion: The uniform heating and cooling process reduces part distortion, which is critical for maintaining dimensional accuracy in precision components.
- Suitability for Complex Assemblies: This method is effective for joining large surface areas and assemblies with numerous joints, making it versatile for intricate designs.
- Repeatability: Vacuum brazing offers highly consistent results, which is essential for mass production and quality control.
- Hermetic Sealing: The process creates a continuous, hermetically sealed bond, which is crucial for applications requiring leak-proof joints.
- Corrosion Resistance: It is ideal for materials sensitive to corrosion or oxidation, ensuring long-term durability.
- Gas Purging: The vacuum environment effectively removes entrapped gases, ensuring strong and defect-free joints.
-
Flexibility and Economic Feasibility:
- Material Versatility: Vacuum aluminum brazing can join materials of varying shapes, forms, and even dissimilar metals, providing design flexibility.
- Cost-Effectiveness: It is economically viable for manufacturing many aluminum products, especially in industries like automotive, aerospace, and HVAC systems.
-
Comparison with Welding:
- Strength: Welding typically produces stronger joints than brazing, as it involves melting and fusing the base materials. However, brazed joints can still achieve strength comparable to the base metals.
- Heat Impact: Welding introduces significant heat, which can lead to distortion and require post-weld treatments. Brazing, with its lower temperatures, minimizes these issues.
- Skill Requirements: Welding aluminum requires more specialized skills and equipment compared to brazing, which is relatively easier to perform and automate.
-
Applications and Industry Preferences:
- Brazing: Commonly used in industries like cookware, automotive, and HVAC systems due to its ability to create strong, leak-proof joints with minimal distortion.
- Welding: Preferred for structural applications where maximum strength is required, such as in aerospace or heavy machinery.
In conclusion, while both welding and brazing have their strengths, vacuum aluminum brazing is often the better choice for applications requiring clean, precise, and repeatable joints with minimal distortion. Welding remains superior for high-strength structural applications but comes with challenges like heat distortion and higher skill requirements. The decision ultimately depends on the specific requirements of the project.
Summary Table:
Aspect | Welding | Brazing |
---|---|---|
Strength | Stronger joints; melts and fuses base materials | Joints comparable to base metals; suitable for less critical applications |
Heat Impact | High heat can cause distortion; post-weld treatments often required | Minimal distortion; lower temperatures reduce heat-related issues |
Skill Requirements | Requires specialized skills and equipment | Easier to perform and automate; less skill-intensive |
Applications | Preferred for structural applications (e.g., aerospace, heavy machinery) | Ideal for complex assemblies, automotive, HVAC, and cookware industries |
Cost | Higher cost due to equipment and labor | Economically viable for mass production and complex designs |
Still unsure whether welding or brazing is right for your aluminum project? Contact our experts today for personalized advice!