Physical vapor deposition (PVD) is a widely used technique in materials science and manufacturing for depositing thin films of material onto a substrate. Unlike chemical vapor deposition (CVD), which involves chemical reactions in the gas phase, PVD relies on physical processes such as sputtering or evaporation to deposit materials. While PVD is generally considered safer than CVD due to the absence of chemical reactions, there are still potential risks associated with the process, particularly related to the materials being deposited and the equipment used.
Key Points Explained:
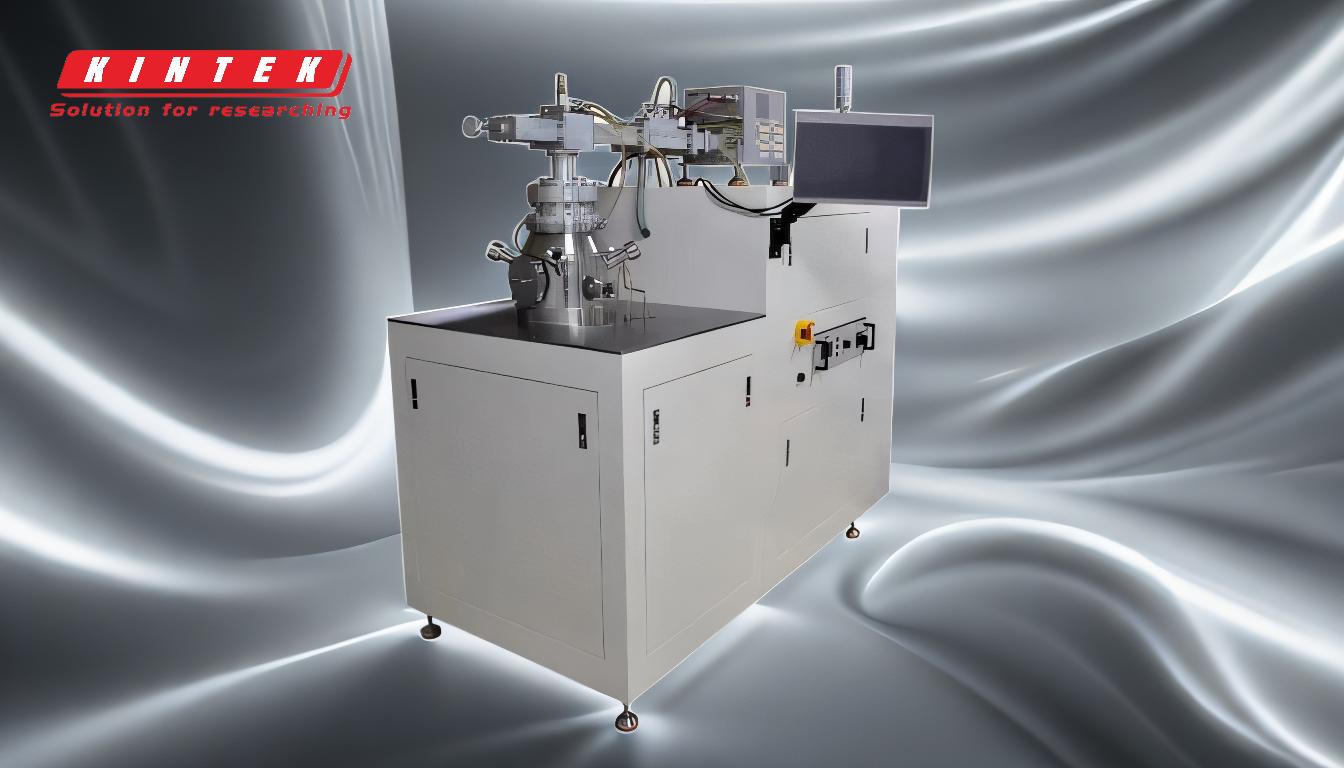
-
Nature of PVD Process:
- PVD involves the physical transfer of material from a source to a substrate, typically through processes like sputtering or evaporation. This means that the process does not inherently involve chemical reactions that could produce toxic byproducts, unlike CVD.
- However, the materials being deposited can still pose risks. For example, if the target material is toxic (e.g., certain metals or compounds), the deposition process could release particles or vapors that are harmful if inhaled or come into contact with skin.
-
Material-Specific Risks:
- The toxicity of PVD largely depends on the materials being used. For instance, depositing materials like lead, cadmium, or arsenic can release toxic particles or vapors during the process. Proper handling and containment of these materials are essential to minimize exposure.
- Even non-toxic materials can become hazardous if they are in the form of fine particles or nanoparticles, which can be inhaled and cause respiratory issues.
-
Equipment and Process Safety:
- PVD systems are typically enclosed, which helps to contain any potentially harmful particles or vapors. However, maintenance and cleaning of the equipment can expose operators to residual materials, so proper safety protocols must be followed.
- The use of high-energy processes like sputtering can generate heat and potentially harmful byproducts, such as ozone or nitrogen oxides, especially if reactive gases are used in the process.
-
Comparison with CVD:
- Unlike CVD, which involves chemical reactions that can produce toxic gases or byproducts, PVD is generally considered less hazardous. However, this does not mean that PVD is entirely risk-free. The absence of chemical reactions reduces the likelihood of toxic gas formation, but the physical nature of the process still requires careful handling of materials and equipment.
-
Mitigation Strategies:
- Proper ventilation and filtration systems are crucial in PVD facilities to capture any airborne particles or vapors.
- Personal protective equipment (PPE), such as gloves, masks, and safety goggles, should be worn by operators to minimize direct exposure to materials.
- Regular maintenance and cleaning of PVD equipment can help prevent the buildup of potentially harmful residues.
-
Regulatory and Safety Standards:
- PVD processes are subject to occupational safety and health regulations, which dictate the handling, storage, and disposal of hazardous materials. Compliance with these standards is essential to ensure the safety of operators and the environment.
- Material Safety Data Sheets (MSDS) for the materials used in PVD should be readily available, and operators should be trained on the specific hazards associated with each material.
In summary, while physical vapor deposition (PVD) is generally considered less toxic than chemical vapor deposition (CVD) due to the absence of chemical reactions, it is not entirely risk-free. The toxicity of PVD depends largely on the materials being deposited and the specific processes used. Proper safety measures, including ventilation, PPE, and adherence to regulatory standards, are essential to mitigate potential risks.
Summary Table:
Aspect | Details |
---|---|
Nature of PVD Process | Physical transfer of material without chemical reactions. |
Material-Specific Risks | Depends on materials used (e.g., lead, cadmium, nanoparticles). |
Equipment Safety | Enclosed systems minimize exposure; maintenance requires safety protocols. |
Comparison with CVD | PVD is less hazardous than CVD but still requires careful handling. |
Mitigation Strategies | Ventilation, PPE, and regular equipment maintenance are crucial. |
Regulatory Standards | Compliance with safety regulations and MSDS is mandatory. |
Ensure your PVD process is safe and efficient—contact our experts today for tailored solutions!