Plastic pyrolysis, a process that thermally decomposes plastic waste in the absence of oxygen, has both potential benefits and environmental risks. While it can convert non-recyclable plastics into valuable products like fuel, gas, and char, the process is not without harm. It can release harmful gases, liquids, and residues that may pollute air, water, and soil if not properly managed. Additionally, the sustainability of feedstock sourcing and the energy requirements for the process are critical factors that influence its overall environmental impact. Proper regulation, advanced technology, and sustainable practices are essential to mitigate these risks and maximize the benefits of plastic pyrolysis.
Key Points Explained:
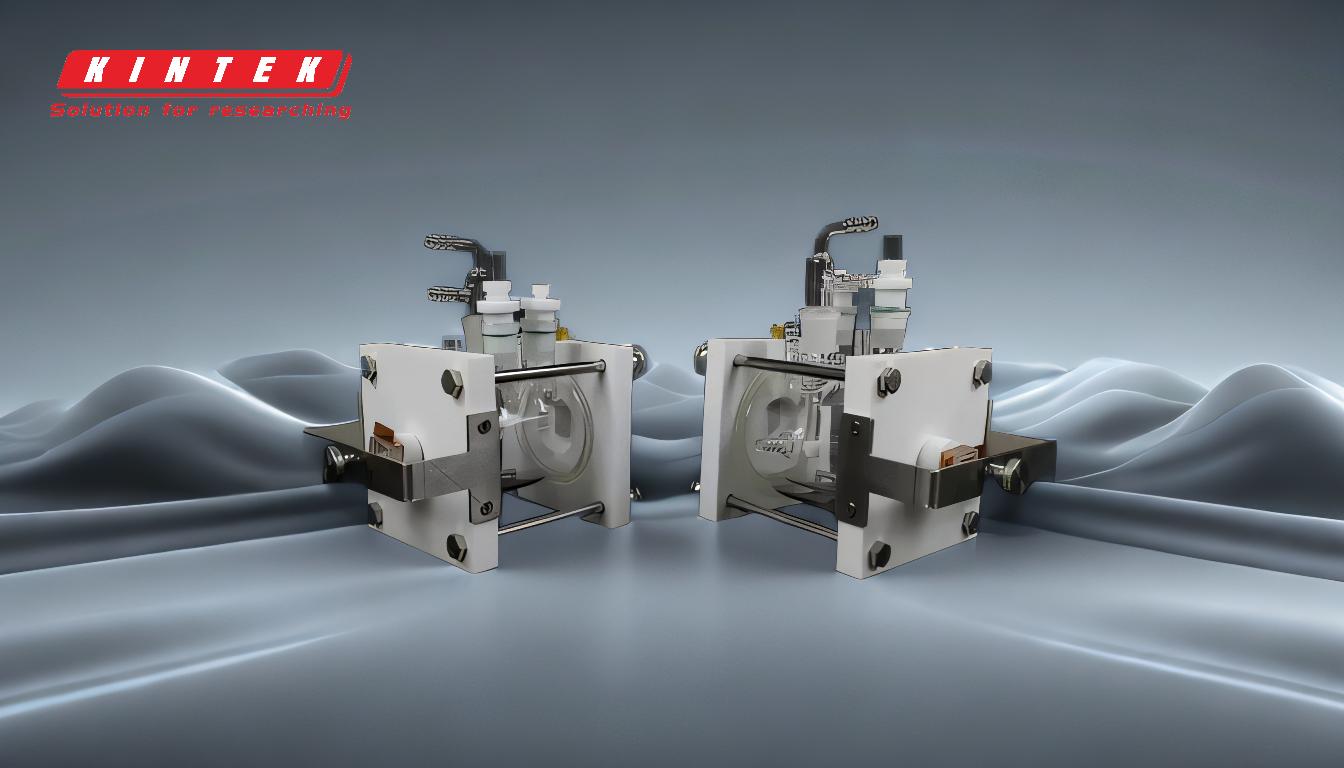
-
Environmental Benefits of Plastic Pyrolysis:
- Reduction in Greenhouse Gas Emissions: Plastic pyrolysis can offset CO2 emissions by preventing plastic waste from decomposing in landfills, where it would release methane (a potent greenhouse gas).
- Production of Valuable Products: The process converts non-recyclable plastics into useful products such as pyrolysis oil, syngas, and char, which can replace fossil fuels and reduce reliance on virgin materials.
- Waste Management Solution: It provides a way to handle plastic waste that would otherwise contribute to pollution, particularly in oceans and landfills.
-
Potential Environmental Harms:
- Release of Pollutants: The pyrolysis process can emit harmful gases like carbon monoxide, carbon dioxide, and volatile organic compounds (VOCs), which contribute to air pollution and climate change.
- Liquid and Solid Residues: The process generates liquid by-products and ash, which may contain toxic substances. If not properly treated, these residues can contaminate soil and water systems.
- Energy Consumption: Pyrolysis requires significant energy input, and if this energy comes from non-renewable sources, it can offset the environmental benefits of the process.
-
Sustainability of Feedstock Sourcing:
- Unsustainable Practices: If the plastic feedstock is sourced unsustainably, such as through deforestation or excessive fossil fuel extraction, the environmental benefits of pyrolysis are diminished.
- Competition with Recycling: Pyrolysis may compete with mechanical recycling, which is generally more energy-efficient and environmentally friendly for certain types of plastics.
-
Technological and Regulatory Challenges:
- Need for Advanced Technology: To minimize environmental harm, pyrolysis plants must employ advanced filtration and emission control systems to capture and neutralize pollutants.
- Regulatory Oversight: Strict regulations are necessary to ensure that pyrolysis facilities operate sustainably and do not exacerbate environmental problems. This includes monitoring emissions, waste management, and energy sources.
-
Role in a Circular Economy:
- Complementary Technology: Pyrolysis can be part of a circular economy by transforming non-recyclable plastics into resources, reducing the need for virgin materials and fossil fuels.
- Integration with Other Processes: It can work alongside other waste management technologies, such as anaerobic digestion, to maximize resource recovery and minimize environmental impact.
-
Historical and Global Context:
- Lessons from History: Historical examples of pyrolysis, such as wood pyrolysis, highlight the potential for environmental harm if the process is not managed sustainably. Deforestation and pollution were significant issues in the past.
- Global Implications: In regions like Africa and Asia, where pyrolysis is increasingly used, there is a risk of repeating historical mistakes if sustainable practices are not adopted.
In conclusion, plastic pyrolysis has the potential to be both beneficial and harmful to the environment. Its overall impact depends on how the process is managed, the sustainability of feedstock sourcing, and the effectiveness of emission control technologies. With proper regulation and innovation, pyrolysis can play a valuable role in reducing plastic waste and supporting a circular economy. However, without careful oversight, it risks exacerbating environmental problems.
Summary Table:
Aspect | Benefits | Risks |
---|---|---|
Greenhouse Gas Emissions | Reduces methane emissions from landfills | Releases CO2, CO, and VOCs if not managed properly |
Product Output | Produces pyrolysis oil, syngas, and char | Generates toxic residues and ash |
Waste Management | Handles non-recyclable plastics, reducing pollution | Competes with more sustainable recycling methods |
Energy Use | Can replace fossil fuels if energy sources are renewable | High energy consumption may offset benefits if sourced from non-renewables |
Regulation & Technology | Advanced systems can minimize emissions and pollution | Lack of regulation can lead to environmental harm |
Want to learn more about sustainable plastic pyrolysis solutions? Contact us today to explore how we can help!