PVD (Physical Vapor Deposition) coatings are highly durable and offer exceptional performance for knives. These coatings are known for their high hardness, wear resistance, corrosion resistance, and low friction properties, making them ideal for demanding applications. The vacuum environment during the PVD process ensures a strong bond with the substrate, eliminating contamination and preventing oxidation. This results in a coating that is resistant to scratching, corrosion, and degradation. Additionally, PVD coatings enhance the aesthetic appearance of knives while providing long-lasting durability, making them a superior choice compared to traditional finishes.
Key Points Explained:
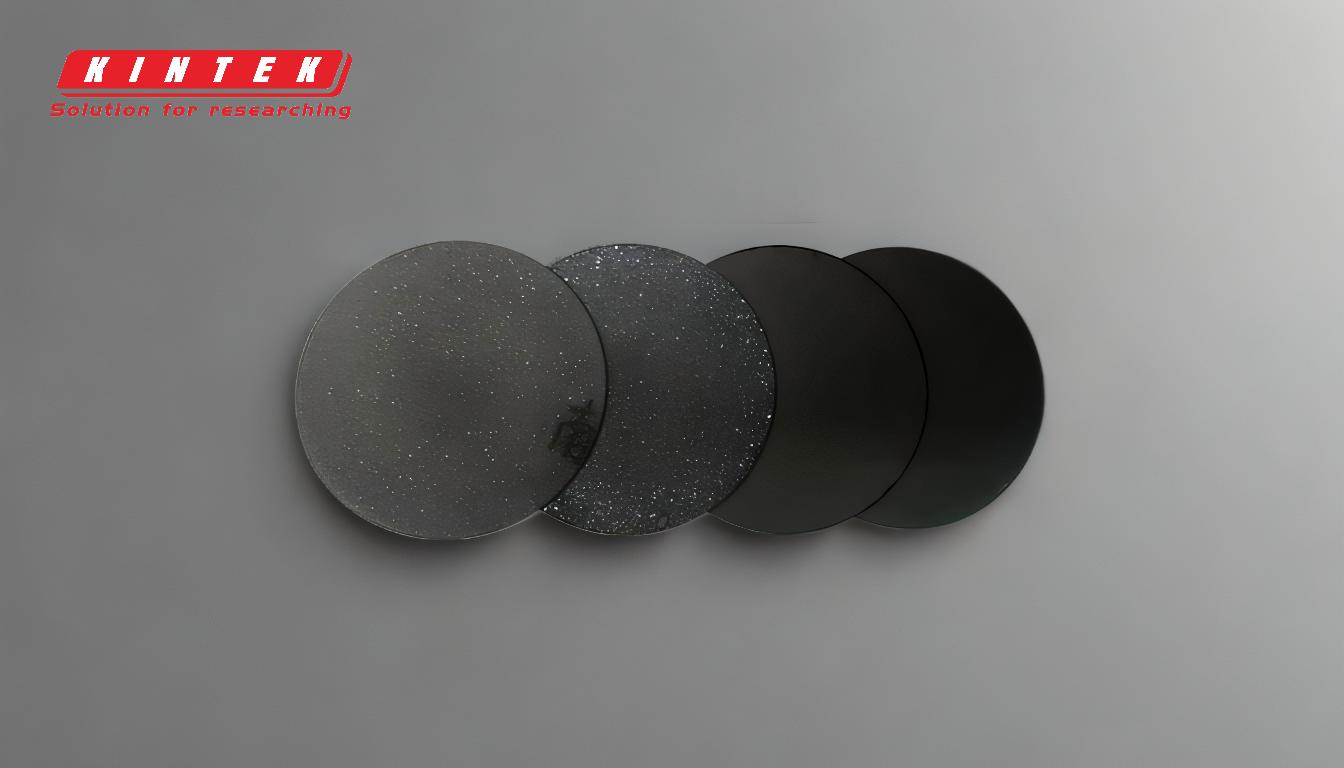
-
High Hardness and Wear Resistance:
- PVD coatings are super-hard, making them highly resistant to wear and abrasion. This is particularly important for knives, which are subject to constant use and friction.
- The hardness of the coating directly impacts its durability, ensuring that the knife edge remains sharp and effective over time.
-
Corrosion and Oxidation Resistance:
- The vacuum environment during the PVD process eliminates contamination and forms a strong bond with the substrate, preventing oxidation and degradation caused by oxygen and moisture.
- This resistance to corrosion is crucial for knives, especially those used in environments where they may be exposed to moisture or harsh chemicals.
-
Low Friction Properties:
- PVD coatings have low friction properties, which reduce the wear and tear on the knife during use. This not only extends the life of the knife but also improves its performance.
- Reduced friction means smoother cutting and slicing, enhancing the overall user experience.
-
Temperature Tolerance and Impact Strength:
- PVD coatings exhibit robust temperature tolerance and impact strength, making them suitable for a wide range of applications, including those that involve extreme conditions.
- This durability ensures that knives with PVD coatings can withstand heavy use and harsh environments without compromising their performance.
-
Aesthetic Enhancement:
- In addition to their functional benefits, PVD coatings enhance the aesthetic appearance of knives. They can replicate the original finish of materials with minimal effort, providing a visually appealing product.
- The thinness of PVD coatings (ranging from 0.5 microns to five microns) allows them to maintain the knife's original design while adding a layer of protection.
-
Longevity and Durability:
- PVD coatings are by far the most durable coatings available today, offering superior quality that outlasts traditional finishes.
- The combination of high hardness, wear resistance, and corrosion resistance ensures that knives with PVD coatings remain functional and attractive for an extended period.
In summary, PVD coatings are an excellent choice for knives due to their exceptional durability, resistance to wear and corrosion, and aesthetic enhancement. These properties make PVD-coated knives a reliable and long-lasting tool for various applications.
Summary Table:
Feature | Benefit |
---|---|
High Hardness | Resists wear and abrasion, keeping knives sharp and durable. |
Corrosion Resistance | Prevents oxidation and degradation, even in harsh environments. |
Low Friction | Reduces wear, improves cutting performance, and enhances user experience. |
Temperature Tolerance | Withstands extreme conditions, ensuring reliability in demanding uses. |
Aesthetic Enhancement | Maintains the knife's design while adding a visually appealing finish. |
Longevity | Outperforms traditional finishes, offering superior durability over time. |
Upgrade your knives with PVD coatings—contact us today to learn more!