PVD (Physical Vapor Deposition) coatings are indeed heat resistant, making them suitable for applications where high temperatures are a concern. These coatings are known for their high hardness, wear resistance, and corrosion resistance, which contribute to their ability to withstand elevated temperatures. PVD coatings are applied in a vacuum environment, resulting in a thin, durable layer that adheres well to the substrate. Their thermal stability, combined with properties like low friction and chemical stability, makes them ideal for industries such as automotive, aerospace, and medical, where heat resistance is critical. While PVD coatings are not immune to all high-temperature conditions, their performance is generally superior to many other coating methods.
Key Points Explained:
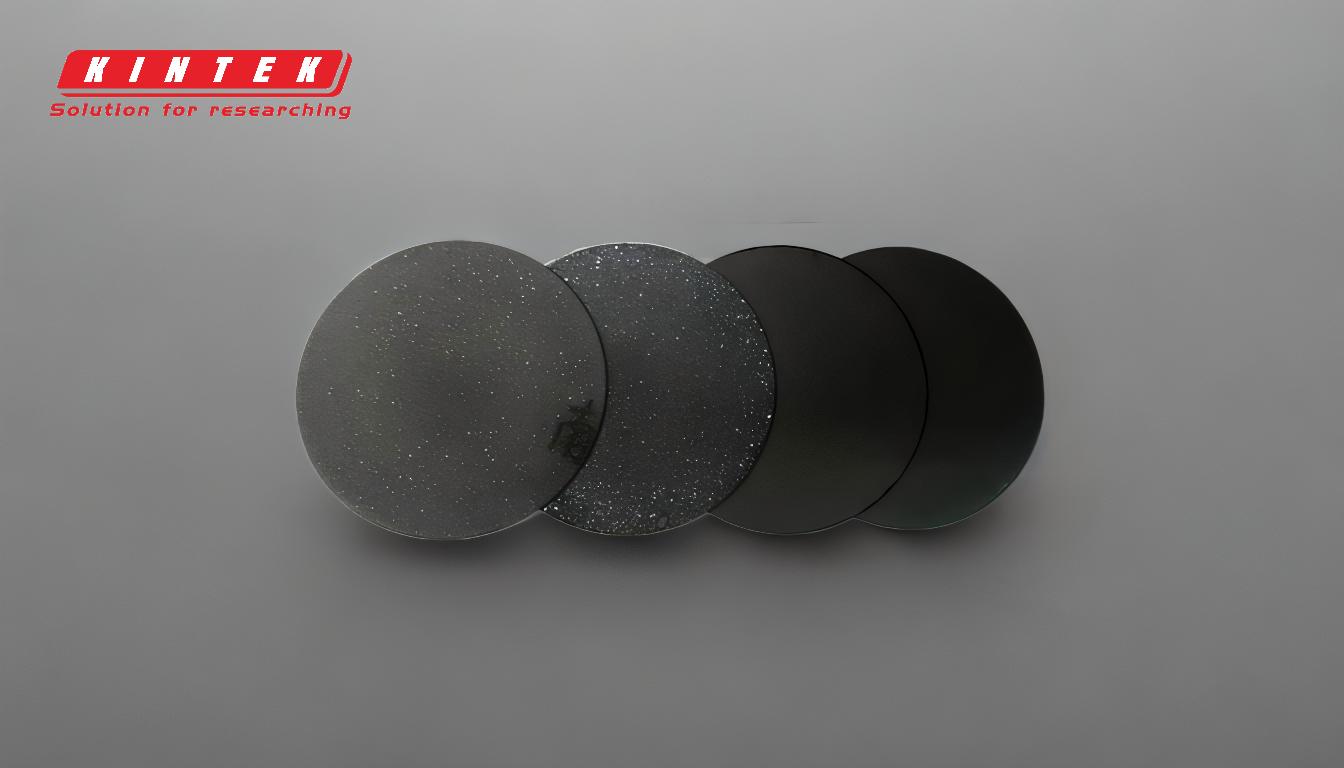
-
Heat Resistance of PVD Coatings:
- PVD coatings exhibit excellent heat resistance due to their high hardness and chemical stability. These properties allow them to maintain structural integrity and performance even at elevated temperatures.
- The coatings are often used in high-temperature environments, such as in automotive engines or aerospace components, where they must withstand thermal stress without degrading.
-
Thin and Durable Nature:
- PVD coatings are extremely thin, ranging from 0.5 to 5 microns, but their durability is exceptional. This thinness does not compromise their ability to resist heat, as the materials used in PVD (e.g., TiN, CrN) are inherently heat-resistant.
- The coatings' adhesion to the substrate is strong, ensuring they remain intact even under thermal cycling or mechanical stress.
-
Applications in High-Temperature Environments:
- PVD coatings are widely used in industries where heat resistance is critical. For example:
- Automotive: In engine components like pistons and valves, where high temperatures and friction are common.
- Aerospace: In turbine blades and other parts exposed to extreme heat during operation.
- Medical: In surgical tools that undergo repeated sterilization at high temperatures.
- PVD coatings are widely used in industries where heat resistance is critical. For example:
-
Comparison with Other Coating Methods:
- PVD coatings outperform many traditional coating methods, such as electroplating, in terms of heat resistance. They are harder, more corrosion-resistant, and better suited for high-temperature applications.
- Unlike some coatings that may degrade or oxidize at high temperatures, PVD coatings maintain their properties, making them a reliable choice for demanding environments.
-
Limitations of PVD Coatings in Heat Resistance:
- While PVD coatings are heat resistant, their performance can be influenced by the substrate material and the specific PVD process used. For instance, coatings on certain alloys may perform better under thermal stress than others.
- The thinness of the coating, while beneficial for many properties, may also limit its ability to provide long-term protection in extremely high-temperature environments without proper substrate support.
-
Material-Specific Performance:
- The heat resistance of PVD coatings can vary depending on the materials used. For example:
- TiN (Titanium Nitride): Known for its high hardness and thermal stability, making it ideal for high-temperature applications.
- CrN (Chromium Nitride): Offers excellent oxidation resistance and is commonly used in environments with elevated temperatures.
- The choice of coating material can be tailored to specific heat resistance requirements.
- The heat resistance of PVD coatings can vary depending on the materials used. For example:
-
Additional Benefits Contributing to Heat Resistance:
- PVD coatings provide other properties that indirectly enhance their heat resistance:
- Wear Resistance: Reduces material loss due to friction, which is crucial in high-temperature applications.
- Corrosion Resistance: Protects the substrate from oxidation and chemical degradation, which can be exacerbated by heat.
- Low Friction: Minimizes heat generation due to friction, further enhancing the coating's performance in high-temperature environments.
- PVD coatings provide other properties that indirectly enhance their heat resistance:
In summary, PVD coatings are heat resistant and well-suited for applications requiring durability under high temperatures. Their thinness, hardness, and chemical stability make them a preferred choice in industries where thermal stress is a concern. However, their performance can vary based on the substrate and specific coating material, so careful selection is essential for optimal results.
Summary Table:
Property | Description |
---|---|
Heat Resistance | High hardness and chemical stability ensure performance at elevated temperatures. |
Thickness | 0.5 to 5 microns, offering durability without compromising heat resistance. |
Applications | Automotive (engine parts), aerospace (turbine blades), medical (surgical tools). |
Material Examples | TiN (Titanium Nitride), CrN (Chromium Nitride). |
Additional Benefits | Wear resistance, corrosion resistance, and low friction enhance heat resistance. |
Discover how PVD coatings can enhance your high-temperature applications—contact us today!