Yes, PVD (Physical Vapor Deposition) coating is possible on plastic, but it comes with specific challenges and considerations. While PVD is commonly used on metals and ceramics, its application on plastics requires careful control of process parameters, particularly temperature, to avoid damaging the plastic substrate. PVD operates at lower temperatures compared to other coating methods (around 500 °C), but this is still too high for many plastics. However, with specialized equipment and techniques, PVD can be adapted for certain plastic materials, especially those with higher thermal stability. The process is also limited by its line-of-sight nature, making it difficult to coat complex geometries or internal surfaces. Despite these challenges, PVD offers advantages such as high hardness, corrosion resistance, and environmental friendliness, making it a viable option for specific plastic applications where durability and aesthetics are critical.
Key Points Explained:
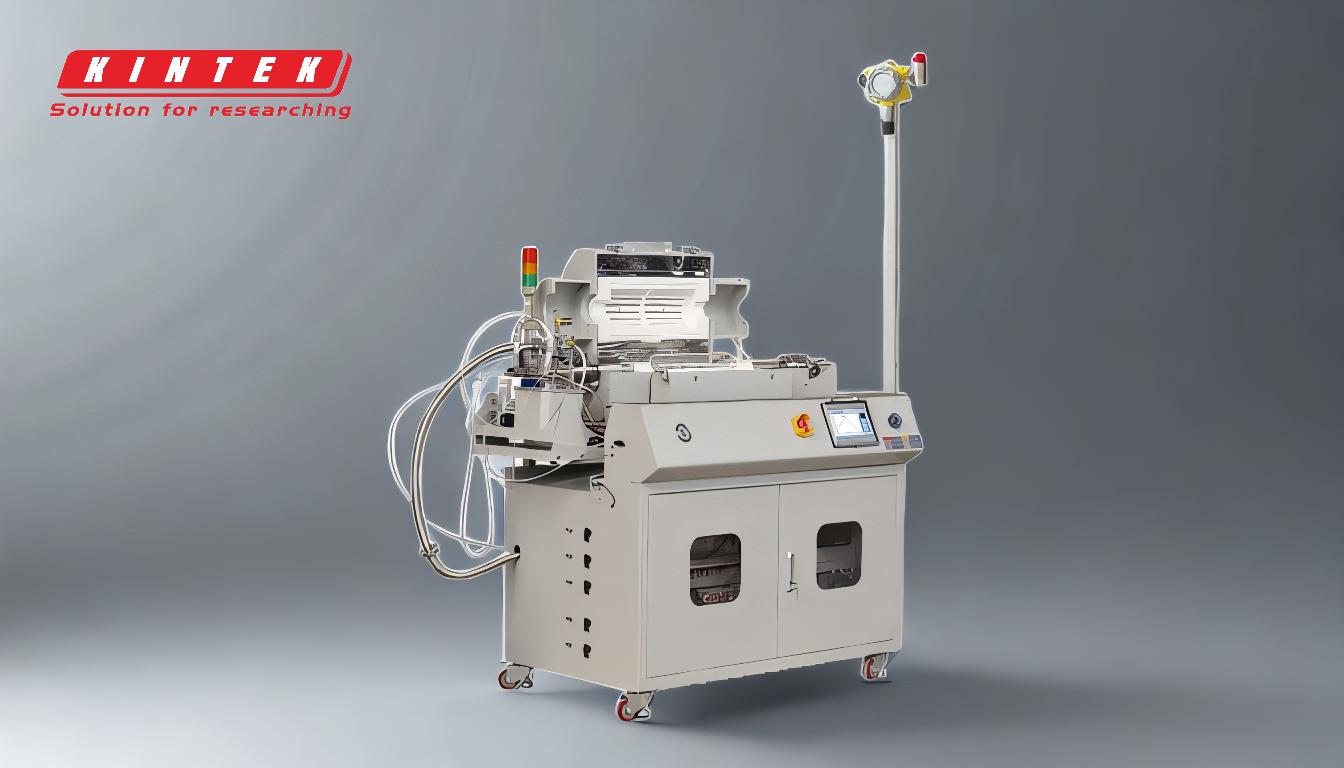
-
Feasibility of PVD Coating on Plastic:
- PVD coating is technically possible on plastic, but it requires careful adaptation due to the thermal sensitivity of most plastics.
- The process operates at relatively lower temperatures (around 500 °C) compared to other methods like CVD, but this is still too high for many plastics. Specialized techniques and equipment are needed to ensure the plastic substrate is not damaged.
- Plastics with higher thermal stability, such as certain engineering plastics, are more suitable for PVD coating.
-
Challenges of PVD Coating on Plastic:
- Temperature Sensitivity: Most plastics cannot withstand the high temperatures required for PVD coating, even at the lower end of the spectrum (around 500 °C). This limits the types of plastics that can be coated.
- Line-of-Sight Limitations: PVD is a line-of-sight process, meaning it cannot effectively coat internal surfaces, undercuts, or complex geometries. This makes it less suitable for intricate plastic parts.
- Adhesion Issues: Achieving strong adhesion between the PVD coating and the plastic substrate can be challenging due to the differences in material properties.
-
Advantages of PVD Coating for Plastic:
- Durability: PVD coatings provide high hardness, wear resistance, and corrosion resistance, which can significantly enhance the lifespan of plastic components.
- Aesthetic Appeal: PVD coatings can be applied in various colors and finishes, making them ideal for decorative applications on plastic products.
- Environmental Friendliness: PVD is a vacuum-based process that produces minimal waste and does not involve harmful chemicals, making it an eco-friendly coating option.
-
Applications of PVD-Coated Plastics:
- Consumer Goods: PVD-coated plastics are used in products like eyeglass frames, writing instruments, and decorative hardware, where both durability and aesthetics are important.
- Automotive Components: Certain plastic parts in vehicles, such as interior trim and decorative elements, can benefit from PVD coatings to improve scratch resistance and appearance.
- Medical Equipment: Some medical devices made from high-temperature-resistant plastics can be PVD-coated to enhance their durability and biocompatibility.
-
Process Considerations for PVD on Plastic:
- Pre-Treatment: Proper surface preparation, such as plasma treatment or primer application, is often necessary to improve adhesion between the PVD coating and the plastic substrate.
- Temperature Control: Specialized equipment and techniques are required to manage the temperature during the PVD process to prevent thermal damage to the plastic.
- Material Selection: Only plastics with sufficient thermal stability should be considered for PVD coating. Examples include polyether ether ketone (PEEK) and polyimides.
-
Cost and Complexity:
- PVD coating is generally more expensive and time-consuming compared to other coating methods, especially when applied to plastics. The need for specialized equipment and skilled operators further adds to the cost.
- Despite the higher costs, the benefits of enhanced durability, aesthetic appeal, and environmental friendliness can justify the investment for specific applications.
In summary, while PVD coating on plastic is possible, it requires careful consideration of material properties, process parameters, and application requirements. For suitable plastics, PVD can provide significant advantages in terms of durability, aesthetics, and environmental impact.
Summary Table:
Aspect | Details |
---|---|
Feasibility | Possible with specialized techniques and high-thermal-stability plastics. |
Challenges | Temperature sensitivity, line-of-sight limitations, adhesion issues. |
Advantages | High durability, aesthetic appeal, environmental friendliness. |
Applications | Consumer goods, automotive components, medical equipment. |
Process Considerations | Pre-treatment, temperature control, material selection. |
Cost & Complexity | Higher cost due to specialized equipment and skilled operators. |
Discover how PVD coating can enhance your plastic products—contact our experts today!