PVD (Physical Vapor Deposition) coating is widely regarded as a sustainable and environmentally friendly process. It is a vacuum-based technology that minimizes waste, reduces the use of toxic substances, and avoids harmful emissions compared to traditional coating methods like electroplating or painting. PVD coatings are durable, long-lasting, and recyclable, making them a preferred choice in industries such as medical implants and manufacturing. The process uses environmentally safe materials like Chromium Nitride (CrN) and Titanium Nitride, and it preserves the recyclable value of the base material, such as stainless steel. Overall, PVD coating aligns with sustainability goals by reducing environmental impact and supporting circular economy principles.
Key Points Explained:
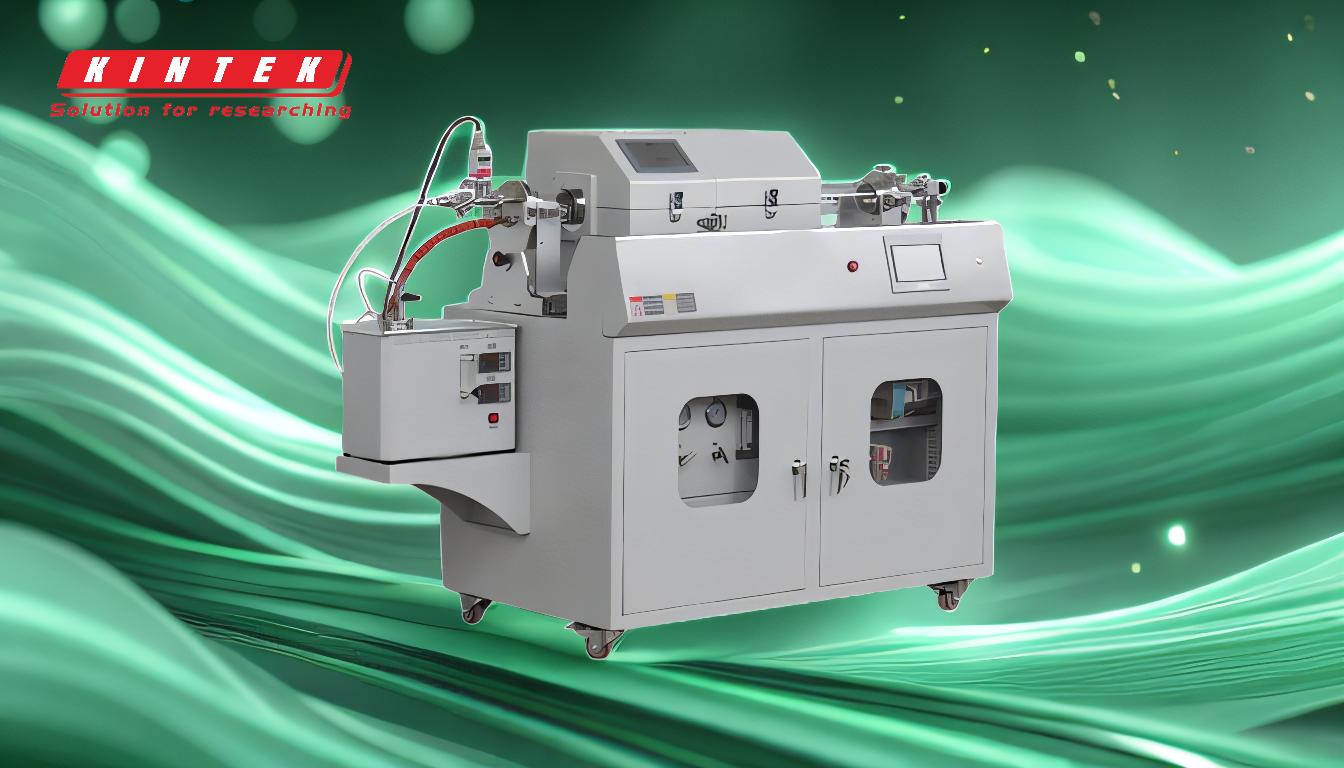
-
Environmentally Friendly Process:
- PVD coating is a vacuum-based process that eliminates the release of harmful chemicals or pollutants into the atmosphere. Unlike traditional "wet" processes such as electroplating, PVD does not require toxic substances, making it a cleaner alternative.
- The process produces no waste or gases, further reducing its environmental footprint.
-
Reduction of Toxic Substances:
- PVD significantly reduces the use of hazardous chemicals compared to electroplating or painting. This makes it safer for both the environment and workers involved in the coating process.
- The materials used in PVD, such as Chromium Nitride (CrN) and Titanium Nitride, are environmentally safe and non-toxic.
-
Durability and Longevity:
- PVD coatings are known for their durability and long-lasting performance. This reduces the need for frequent replacements or repairs, which in turn minimizes waste and resource consumption over time.
- The durability of PVD coatings makes them ideal for high-performance applications, such as surgical and medical implants, where reliability is critical.
-
Recyclability:
- One of the most significant advantages of PVD coating is that it does not alter the recyclable value of the base material, such as stainless steel. Coated components can be fully recycled at the end of their lifecycle, supporting sustainability efforts.
- The process itself is also recyclable, further enhancing its eco-friendly credentials.
-
Energy Efficiency:
- PVD processes are typically more energy-efficient compared to traditional coating methods. The vacuum-based technology requires less energy to operate, contributing to lower carbon emissions and energy consumption.
-
Industry Applications:
- PVD coatings are widely used in industries such as medical implants, aerospace, and manufacturing due to their purity, cleanliness, and durability. These industries benefit from the sustainability and performance advantages of PVD technology.
- The medical implant industry, in particular, prefers PVD coatings because they are biocompatible and meet stringent safety and environmental standards.
-
Support for Circular Economy:
- By preserving the recyclable value of materials and reducing waste, PVD coating supports the principles of a circular economy. This approach emphasizes the reuse and recycling of materials to minimize environmental impact and resource depletion.
- The ability to recycle coated components at the end of their life ensures that materials remain in use for as long as possible, reducing the need for new raw materials.
In summary, PVD coating is a sustainable and environmentally friendly technology that offers numerous advantages over traditional coating methods. Its ability to reduce toxic substances, produce durable and recyclable coatings, and support energy efficiency makes it a key player in promoting sustainability across various industries.
Summary Table:
Key Benefit | Description |
---|---|
Environmentally Friendly | Vacuum-based process with no harmful emissions or waste. |
Reduction of Toxic Substances | Uses non-toxic materials like CrN and TiN, safer for workers and the environment. |
Durability & Longevity | Long-lasting coatings reduce waste and resource consumption. |
Recyclability | Preserves recyclable value of base materials like stainless steel. |
Energy Efficiency | Lower energy consumption compared to traditional coating methods. |
Industry Applications | Widely used in medical implants, aerospace, and manufacturing. |
Circular Economy Support | Promotes reuse and recycling, minimizing environmental impact. |
Ready to adopt sustainable PVD coating solutions? Contact us today to learn more!