PVD (Physical Vapor Deposition) coatings are not inherently waterproof, but they are highly resistant to corrosion, wear, and environmental factors due to their dense and uniform structure. While the thin layer (0.5–5 microns) of PVD coating provides excellent protection against moisture, oxidation, and chemical exposure, it does not create a fully waterproof barrier. The coating's effectiveness in resisting water penetration depends on the substrate material, the specific PVD coating type, and the application environment. PVD coatings are ideal for applications requiring durability and resistance to harsh conditions, but they should not be considered a substitute for waterproofing in scenarios where complete water resistance is critical.
Key Points Explained:
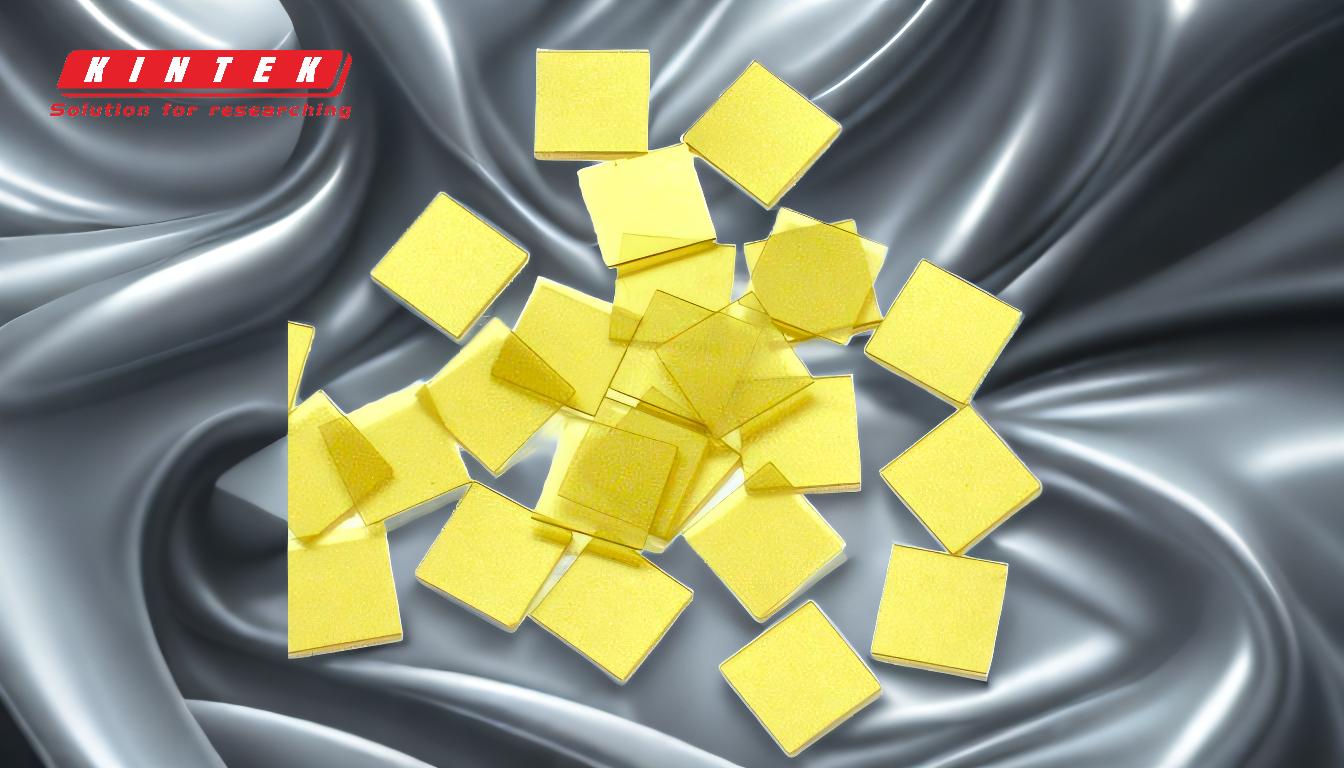
-
PVD Coating Properties and Water Resistance:
- PVD coatings are known for their high hardness, wear resistance, and corrosion resistance, which make them highly durable in harsh environments.
- While PVD coatings provide excellent protection against moisture and oxidation due to their dense and uniform structure, they are not inherently waterproof. Their thinness (0.5–5 microns) limits their ability to create a fully waterproof barrier.
-
Dependence on Substrate Material:
- The effectiveness of PVD coatings in resisting water penetration depends on the underlying substrate material. For example, coatings applied to metals like titanium alloys (e.g., Ti-6Al-4V) enhance fatigue and endurance limits, but the substrate's properties still play a significant role in overall water resistance.
- If the substrate is porous or prone to water absorption, the PVD coating alone may not prevent water ingress.
-
Application-Specific Performance:
- PVD coatings are widely used in industries such as automotive, aerospace, and medical, where resistance to wear, corrosion, and environmental factors is critical. However, these applications do not typically require complete waterproofing.
- In scenarios where waterproofing is essential, additional protective measures (e.g., sealants or topcoats) may be necessary alongside PVD coatings.
-
Limitations of PVD Coatings:
- PVD coatings are extremely thin, which limits their ability to block water penetration entirely. While they provide excellent surface protection, they are not designed to act as a waterproof seal.
- The coating's performance may also vary on complex geometries (e.g., back and sides of tools) due to limitations in deposition uniformity.
-
Practical Considerations for Buyers:
- If waterproofing is a primary requirement, PVD coatings should be evaluated in conjunction with other protective measures. For example, combining PVD coatings with a waterproof sealant can enhance overall performance.
- Buyers should consider the specific environmental conditions and application requirements when selecting PVD coatings. While they offer exceptional durability and resistance, they are not a standalone solution for waterproofing.
In summary, PVD coatings are highly resistant to moisture and environmental factors but are not fully waterproof. Their performance depends on the substrate material, coating type, and application environment. For applications requiring complete waterproofing, additional protective measures may be necessary.
Summary Table:
Aspect | Details |
---|---|
Water Resistance | Resists moisture and oxidation but not fully waterproof. |
Thickness | 0.5–5 microns; too thin for complete waterproofing. |
Substrate Dependence | Performance depends on the material (e.g., metals like Ti-6Al-4V). |
Applications | Automotive, aerospace, medical—ideal for durability, not waterproofing. |
Limitations | Thin layer and complex geometries may reduce effectiveness. |
Additional Measures | Combine with sealants for enhanced waterproofing. |
Need help choosing the right PVD coating for your application? Contact our experts today!