PVD (Physical Vapor Deposition) coatings are indeed highly corrosion-resistant, making them suitable for demanding applications where durability is critical. These coatings create a thin, hard, and durable layer that bonds strongly to the substrate, enhancing its resistance to corrosion, oxidation, and wear. The process involves vaporizing a target material in a vacuum and depositing it onto the substrate, ensuring a pure and long-lasting coating. PVD coatings, such as Zirconium Nitride (ZrN), have demonstrated exceptional performance in corrosion resistance tests, including neutral salt spray and CASS tests. Their hardness, thinness, and strong adhesion make them ideal for harsh environments, including coastal areas.
Key Points Explained:
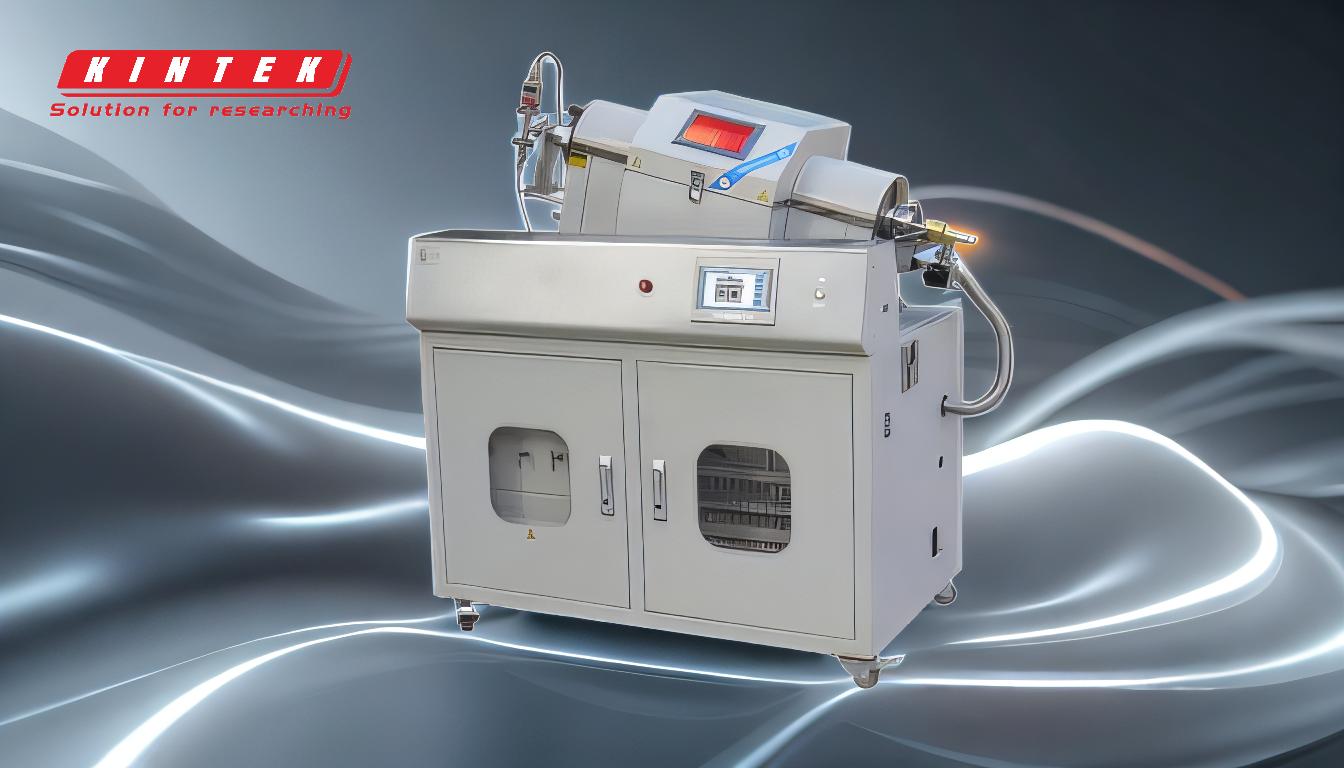
-
Corrosion Resistance of PVD Coatings:
- PVD coatings are highly resistant to corrosion and oxidation. They form a protective layer that shields the substrate from environmental factors that cause rust, tarnish, or degradation.
- The thinness of PVD coatings (0.5 to 5 microns) does not compromise their effectiveness. Instead, their extreme thinness makes them difficult to remove, ensuring long-term protection.
-
Durability and Hardness:
- PVD coatings are four times harder than chrome, making them highly scratch-resistant and durable. This hardness contributes to their ability to withstand harsh conditions, including corrosive environments.
- The hardness of the coating is a critical factor in its durability. For example, a TiN (Titanium Nitride) coating can increase the fatigue limit and endurance of a substrate material like Ti-6Al-4V alloy.
-
Adhesion and Longevity:
- PVD coatings bond strongly to the substrate, even penetrating it slightly. This strong adhesion ensures that the coating remains intact for extended periods, enhancing the product's lifespan by up to ten times in some cases.
- The annealing process used in PVD coating ensures that the layer is free from impurities, further improving its durability and resistance to wear and corrosion.
-
Performance in Corrosion Tests:
- PVD coatings, such as Zirconium Nitride (ZrN), have demonstrated exceptional performance in standardized corrosion tests. For example, they have surpassed 1200 hours in neutral salt spray tests (ASTM B117) and over 150 hours in CASS tests, which are rigorous measures of corrosion resistance.
- These results highlight the suitability of PVD coatings for applications exposed to corrosive environments, such as marine or coastal settings.
-
Applications in Harsh Environments:
- PVD coatings are ideal for projects exposed to harsh environments, including those near the coast, where saltwater and humidity can accelerate corrosion.
- Their ability to replicate the original finish of materials with minimal effort makes them versatile for both functional and aesthetic applications.
-
Process and Purity:
- The PVD process involves vaporizing a target material in a vacuum and depositing it onto the substrate. This ensures a pure coating free from impurities, which enhances its durability and corrosion resistance.
- The process allows for precise control over the coating's properties, including thickness, hardness, and adhesion, ensuring optimal performance for specific applications.
In summary, PVD coatings are highly corrosion-resistant due to their hardness, strong adhesion, and purity. Their performance in rigorous corrosion tests and suitability for harsh environments make them an excellent choice for applications requiring long-lasting durability and protection against corrosion.
Summary Table:
Feature | Details |
---|---|
Corrosion Resistance | Highly resistant to rust, tarnish, and oxidation; ideal for harsh environments. |
Hardness | 4x harder than chrome; scratch-resistant and durable. |
Adhesion | Bonds strongly to substrates, enhancing longevity by up to 10x. |
Performance in Tests | Exceeds 1200 hours in neutral salt spray tests and 150 hours in CASS tests. |
Applications | Suitable for marine, coastal, and other corrosive environments. |
Process | Pure, impurity-free coatings via vacuum vaporization, ensuring durability. |
Enhance your project's durability with PVD coatings—contact our experts today!