PVD (Physical Vapor Deposition) finishes are generally considered safe once applied, as the particles are firmly bonded to the substrate and do not become airborne. However, during the application process, precautions are necessary to avoid inhaling particles, which can be harmful. PVD coatings are highly durable, corrosion-resistant, and often food-safe, making them suitable for various applications, including cutlery and kitchen equipment. Their thinness and strong adhesion to substrates ensure they pose minimal health risks post-application.
Key Points Explained:
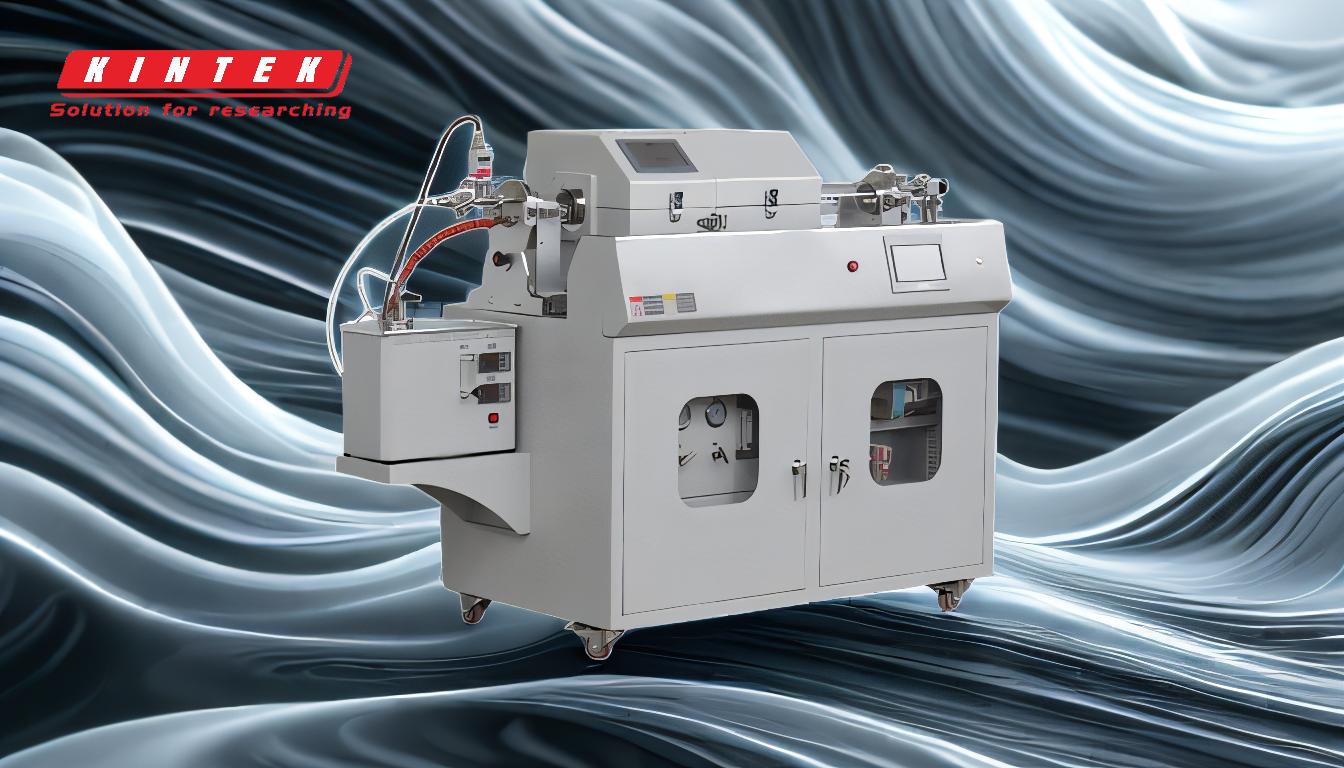
-
Safety of PVD Coatings Post-Application:
- Once applied, PVD coatings are safe because the particles are firmly bonded to the substrate and cannot become airborne. This ensures no risk of inhalation or exposure to harmful particles.
- The coatings are chemically and biologically inert, making them suitable for use in environments where safety is critical, such as in food-related applications.
-
Precautions During Application:
- During the PVD coating process, particles can become airborne, posing inhalation risks. Proper safety measures, such as ventilation and protective equipment, are essential to minimize exposure.
- The application process involves high temperatures and vacuum conditions, which require specialized equipment and trained personnel to ensure safety.
-
Durability and Resistance:
- PVD coatings are highly resistant to corrosion, oxidation, and wear, making them ideal for long-lasting applications.
- The coatings are extremely thin (0.5 to 5 microns) and adhere strongly to the substrate, making them difficult to remove and ensuring their durability.
-
Food-Safe Properties:
- Most PVD coatings are food-safe due to their strong adhesion and inert nature. This makes them suitable for use in the cutlery industry and commercial kitchen equipment.
- Their wear-resistant properties enhance their functionality in environments where hygiene and durability are paramount.
-
Material-Specific Benefits:
- The properties of PVD coatings can vary depending on the substrate material. For example, coatings like TiN (Titanium Nitride) can improve the fatigue limit and endurance of certain alloys, such as Ti-6Al-4V.
- The hardness of the coating plays a crucial role in determining its durability and performance in specific applications.
-
Versatility in Applications:
- PVD coatings are widely used in both decorative and functional applications, including jewelry, automotive parts, and medical devices, due to their aesthetic appeal and protective properties.
- Their ability to replicate the original finish of materials with minimal effort makes them a popular choice in industries requiring precise and high-quality finishes.
In summary, PVD finishes are safe and highly beneficial for a wide range of applications, provided that proper precautions are taken during the application process. Their durability, resistance to wear and corrosion, and food-safe properties make them an excellent choice for industries prioritizing safety and performance.
Summary Table:
Aspect | Details |
---|---|
Safety Post-Application | Particles are firmly bonded; no airborne risks. Chemically and biologically inert. |
Precautions During Application | Use ventilation and protective gear to avoid inhaling harmful particles. |
Durability | Highly resistant to corrosion, oxidation, and wear. Thin (0.5-5 microns) and strong adhesion. |
Food-Safe Properties | Suitable for cutlery and kitchen equipment due to inert nature and durability. |
Material-Specific Benefits | Enhances fatigue limit and endurance of alloys like Ti-6Al-4V. Hardness impacts durability. |
Applications | Used in jewelry, automotive parts, medical devices, and more for aesthetics and protection. |
Interested in PVD coatings for your industry? Contact us today to learn more!