PVD (Physical Vapor Deposition) coatings are renowned for their exceptional durability and longevity, making them a top choice in various industries, including jewelry, automotive, and industrial applications. The longevity of PVD coatings can range from 10 years to hundreds of years, depending on factors such as the substrate material, coating thickness, and environmental conditions. PVD coatings are highly resistant to corrosion, scratches, and wear, outperforming traditional finishes like electroplating. The process involves vaporizing a target material in a vacuum and depositing it onto the surface, ensuring a pure and durable coating. Proper application and maintenance further enhance its lifespan, making PVD a long-lasting solution for demanding applications.
Key Points Explained:
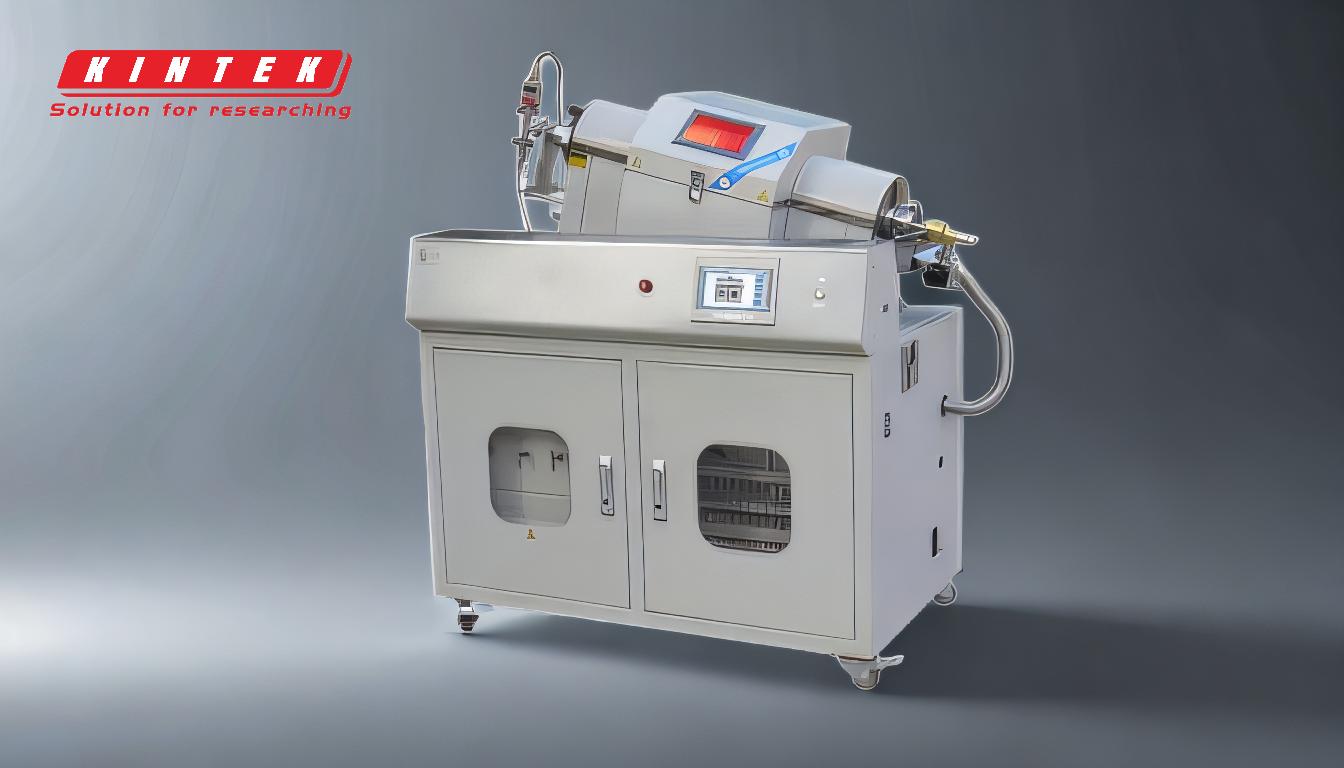
-
Durability of PVD Coatings:
- PVD coatings are considered the most durable coatings available today, offering superior resistance to corrosion, scratches, and wear.
- They outperform traditional finishes like electroplating, which typically lasts only about 1 year, whereas PVD-coated items can last 3 years or more with everyday wear.
-
Lifespan Variability:
- The lifespan of PVD coatings can vary significantly, ranging from 10 years to hundreds of years.
- This variability depends on several factors, including the substrate material, coating thickness, and the specific application conditions.
-
Application Process:
- The PVD process involves heating a target material until it vaporizes and then depositing the vapor onto the surface in a vacuum environment.
- This method ensures the coating is free from impurities, enhancing its durability and longevity.
-
Industry-Specific Longevity:
- In the jewelry industry, PVD coatings can last up to 10 years if applied correctly and maintained properly.
- PVD-coated jewelry is more durable than electroplated jewelry, which typically lasts only about 1 year.
-
Environmental Resistance:
- PVD coatings exhibit robust temperature tolerance, impact strength, and excellent abrasion and corrosion resistance.
- These properties make PVD coatings suitable for demanding applications where durability is critical.
-
Maintenance and Care:
- Proper maintenance can significantly extend the lifespan of PVD-coated items.
- Regular cleaning and avoiding harsh chemicals can help maintain the coating's integrity and appearance.
-
Comparative Advantages:
- PVD coatings are by far the most durable coating available today, offering superior quality that will outlast any traditional finish.
- The enhanced durability and resistance to environmental factors make PVD coatings a preferred choice for high-performance applications.
In summary, PVD coatings are highly durable and long-lasting, with their lifespan influenced by various factors such as application conditions and maintenance. Their superior resistance to wear, corrosion, and environmental factors makes them an excellent choice for a wide range of applications, ensuring they remain a top-tier solution for durability and longevity.
Summary Table:
Aspect | Details |
---|---|
Durability | Superior resistance to corrosion, scratches, and wear. |
Lifespan | 10 years to hundreds of years, depending on conditions. |
Application Process | Vaporizes target material in a vacuum, ensuring a pure and durable coating. |
Industry Longevity | Jewelry: up to 10 years; outperforms electroplating (1 year). |
Environmental Resistance | High temperature tolerance, impact strength, and corrosion resistance. |
Maintenance | Regular cleaning and avoiding harsh chemicals extend lifespan. |
Ready to enhance your products with durable PVD coatings? Contact us today to learn more!