Physical Vapor Deposition (PVD) coating is a highly advanced and versatile coating technology that offers numerous benefits, including lower process temperatures, precise thin-film deposition, and environmental friendliness. It is widely used across various industries, from cutting tools to decorative products, due to its ability to enhance durability, wear resistance, and aesthetic appeal. However, whether PVD is the "best" coating depends on the specific application, material, and performance requirements. While PVD excels in many areas, such as producing high-hardness coatings and reducing thermal distortion, its suitability must be evaluated against alternative coating methods like Chemical Vapor Deposition (CVD) or electroplating, which may offer advantages in other contexts.
Key Points Explained:
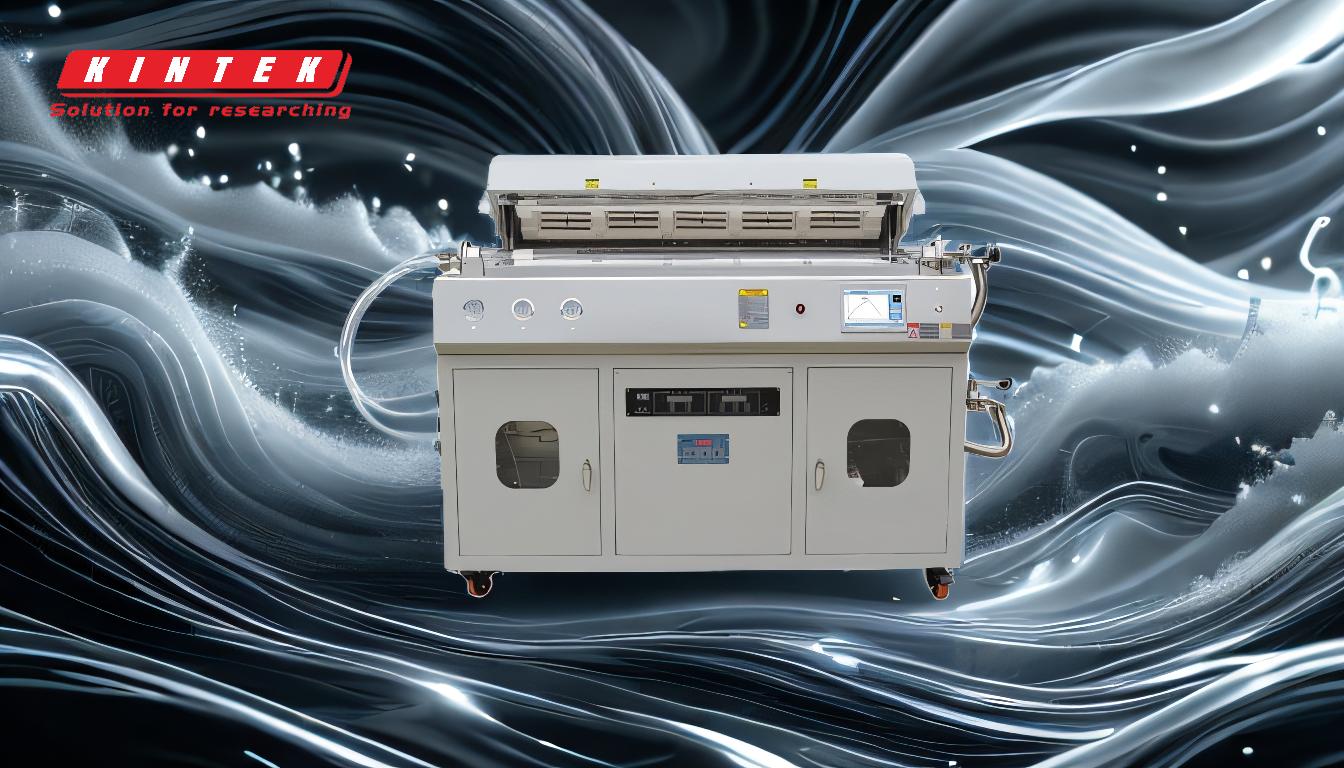
-
Advantages of PVD Coating:
- Lower Process Temperatures: PVD operates at temperatures around 500 °C, which minimizes thermal distortion and damage to the substrate. This makes it ideal for heat-sensitive materials like high-speed steel (HSS) and carbide tools.
- Precision and Thin Films: PVD allows for the deposition of ultra-thin coatings (0.02-5 microns), ensuring precise control over thickness and uniformity. This is particularly beneficial for applications requiring tight tolerances, such as optical coatings and fine blanking tools.
- Environmental and Safety Benefits: Unlike chemical-based methods, PVD does not require toxic substances or extensive cleanup, making it safer and more eco-friendly.
-
Applications of PVD Coating:
- Industrial Tools: PVD is extensively used for cutting tools, molds, and dies, where high hardness, wear resistance, and sharpness are critical. The compressive stress formed during cooling also makes PVD coatings suitable for interrupted cutting processes like milling.
- Decorative Products: PVD is widely employed in the production of jewelry, door and window hardware, kitchen and bathroom fixtures, and other decorative items, thanks to its ability to provide a superior finish and enhance durability.
- Functional Coatings: PVD is used to create thin films for mechanical, optical, chemical, or electronic functions, making it a versatile choice for various industries.
-
Durability and Performance:
- PVD coatings bond a thin layer of metal to the substrate, significantly improving durability and wear resistance. The annealing process allows for the removal and replacement of this layer, ensuring long-lasting performance.
- The molecular-scale application of PVD results in a high-quality finish, reducing cutting force and heat generation in tools, which enhances their lifespan and efficiency.
-
Comparison with Other Coating Methods:
- PVD vs. CVD: While PVD operates at lower temperatures and is more environmentally friendly, CVD can produce thicker coatings and is better suited for certain high-temperature applications. The choice between PVD and CVD depends on the specific requirements of the application.
- PVD vs. Electroplating: PVD offers superior adhesion and hardness compared to electroplating, which is often limited by its reliance on chemical reactions and potential environmental hazards.
-
Limitations of PVD:
- Coating Thickness: PVD coatings are generally thinner (3-5 microns), which may not be suitable for applications requiring thicker protective layers.
- Cost and Complexity: While PVD reduces production costs in the long run, the initial investment in equipment and the need for skilled operators can be a barrier for some manufacturers.
In conclusion, PVD coating is an excellent choice for many applications due to its precision, durability, and environmental benefits. However, whether it is the "best" coating depends on the specific needs of the project, including material compatibility, performance requirements, and cost considerations. For applications requiring high hardness, wear resistance, and minimal thermal distortion, PVD is often the preferred option.
Summary Table:
Aspect | Details |
---|---|
Advantages | Lower process temperatures, precise thin-film deposition, eco-friendly |
Applications | Industrial tools, decorative products, functional coatings |
Durability | High hardness, wear resistance, long-lasting performance |
Comparison with CVD | Lower temperatures, thinner coatings, but CVD suits high-temperature needs |
Comparison with Electroplating | Superior adhesion and hardness, less environmental impact |
Limitations | Thinner coatings (3-5 microns), higher initial costs, requires skilled operators |
Still unsure if PVD is the right coating for your needs? Contact our experts today for personalized advice!