Sputtering is indeed a form of Physical Vapor Deposition (PVD). PVD is a broad category of vacuum deposition techniques used to produce thin films and coatings, where materials transition from a condensed phase to a vapor phase and then back to a thin film condensed phase. Sputtering, a specific PVD method, involves ejecting atoms from a target material using high-energy particle bombardment in a vacuum environment. This process is widely used in industries due to its versatility, ability to deposit a wide range of materials, and economic efficiency. Below, the key points explaining why sputtering is a form of PVD are detailed.
Key Points Explained:
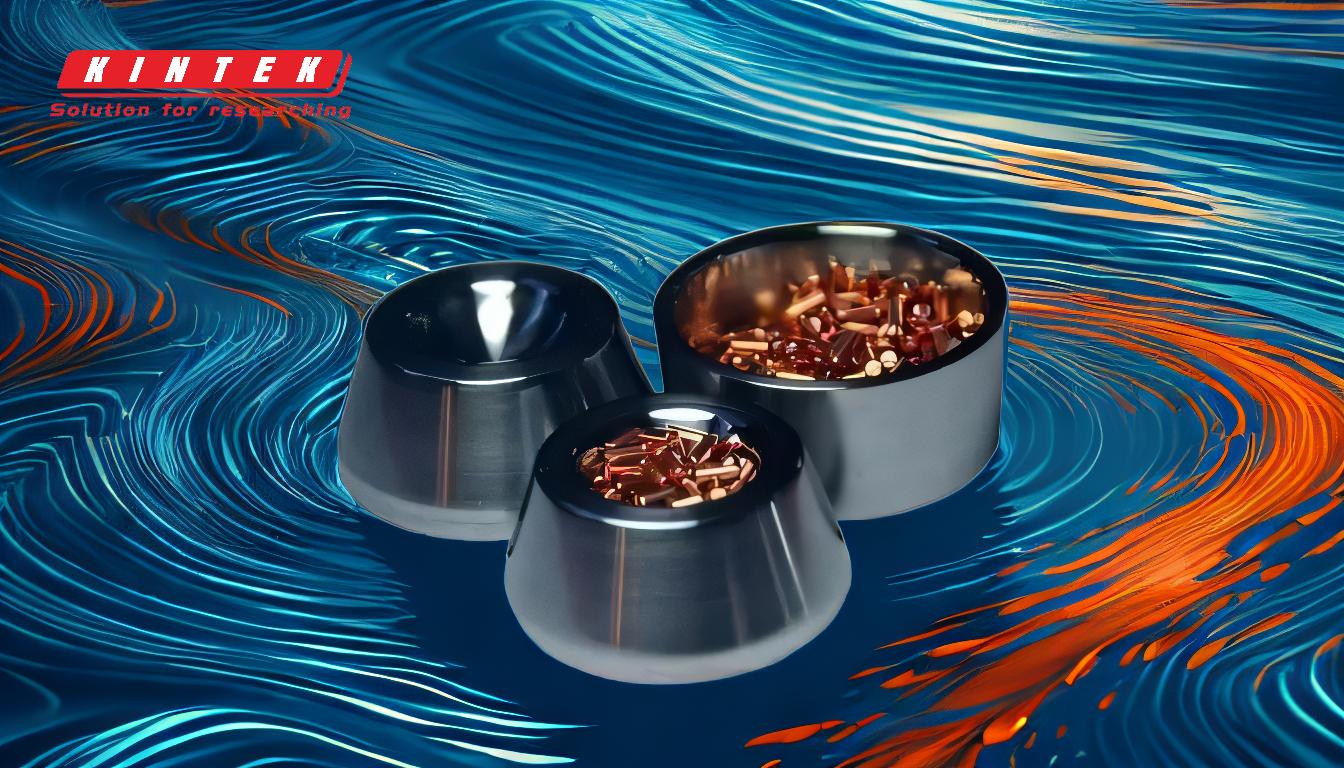
-
Definition of PVD:
- PVD is a vacuum deposition process where materials transition from a condensed phase (solid or liquid) to a vapor phase and then condense back into a thin film on a substrate.
- It involves three key steps: vaporization of the coating material, migration of atoms or molecules, and deposition onto the substrate.
- PVD is characterized by its "line of sight" coating process, physical bonding, and ability to produce pure, environmentally friendly coatings.
-
Sputtering as a PVD Mechanism:
- Sputtering is a specific PVD technique where atoms are ejected from the surface of a target material when struck by high-energy particles, typically ions from a plasma.
- The process occurs in a vacuum chamber, aligning with the PVD requirement of a vacuum environment.
- The ejected atoms then travel through the vapor phase and deposit onto a substrate, forming a thin film.
-
Process Details:
- Sputtering involves introducing a controlled gas (usually argon) into a vacuum chamber and energizing a cathode to create a plasma.
- The plasma generates high-energy ions that bombard the target material, causing atoms to be ejected and deposited onto the substrate.
- This non-thermal vaporization process is a hallmark of PVD, as it does not rely on melting or evaporation but rather on atomic collision cascades.
-
Types of Sputtering:
- Sputtering includes various methods such as diode sputtering, reactive sputtering, bias sputtering, magnetron sputtering, and ion-beam sputtering.
- Common techniques like DC and RF sputtering are widely used, with RF sputtering offering advantages such as deposition on insulating materials and sustaining plasma at low pressures.
-
Advantages of Sputtering in PVD:
- Sputtering is one of the most economical PVD methods, making it a standard coating technique in many industries.
- It allows for the deposition of a wide variety of materials on diverse substrates, including metals, ceramics, and polymers.
- The process produces high-quality, uniform coatings with excellent adhesion and purity.
-
Alignment with PVD Characteristics:
- Sputtering operates within the standard PVD temperature range (320 to 900°F) and does not require heat treatment.
- It produces coatings with an average thickness of .00004 to .0002 inches, replicating the finish of the target material.
- The "line of sight" nature of sputtering ensures precise coating deposition, making it ideal for applications requiring tight tolerances.
-
Industrial Applications:
- Sputtering is widely used in industries such as semiconductor manufacturing, optics, and decorative coatings.
- Its ability to deposit thin films with controlled properties makes it essential for producing microelectronics, solar panels, and wear-resistant coatings.
-
Environmental and Quality Benefits:
- Like other PVD methods, sputtering is environmentally friendly, as it does not involve hazardous chemicals or produce harmful byproducts.
- The coatings produced are pure and improve the surface quality of substrates, enhancing their durability and performance.
In summary, sputtering is a well-established form of PVD that adheres to all the defining characteristics of the PVD process. Its ability to deposit a wide range of materials with high precision and efficiency makes it a cornerstone of modern thin-film coating technologies.
Summary Table:
Aspect | Details |
---|---|
Definition of PVD | Vacuum deposition process transitioning materials to vapor and back to film. |
Sputtering Mechanism | Ejects atoms from a target using high-energy ions in a vacuum environment. |
Process Details | Uses argon gas and plasma to deposit atoms onto substrates. |
Types of Sputtering | Includes diode, reactive, magnetron, and RF sputtering. |
Advantages | Economical, versatile, high-quality coatings with excellent adhesion. |
Applications | Used in semiconductors, optics, solar panels, and wear-resistant coatings. |
Ready to explore how sputtering can enhance your thin-film coating processes? Contact our experts today!