Sputtering generally offers better step coverage compared to evaporation due to the higher energy of sputtered atoms, which results in better adhesion and more uniform deposition on complex geometries. While evaporation can struggle with step coverage, especially on high-aspect-ratio features, sputtering provides more control over the deposition process, making it suitable for applications requiring precise and uniform thin films. However, the choice between the two methods depends on specific application requirements, such as material compatibility, deposition rate, and cost considerations.
Key Points Explained:
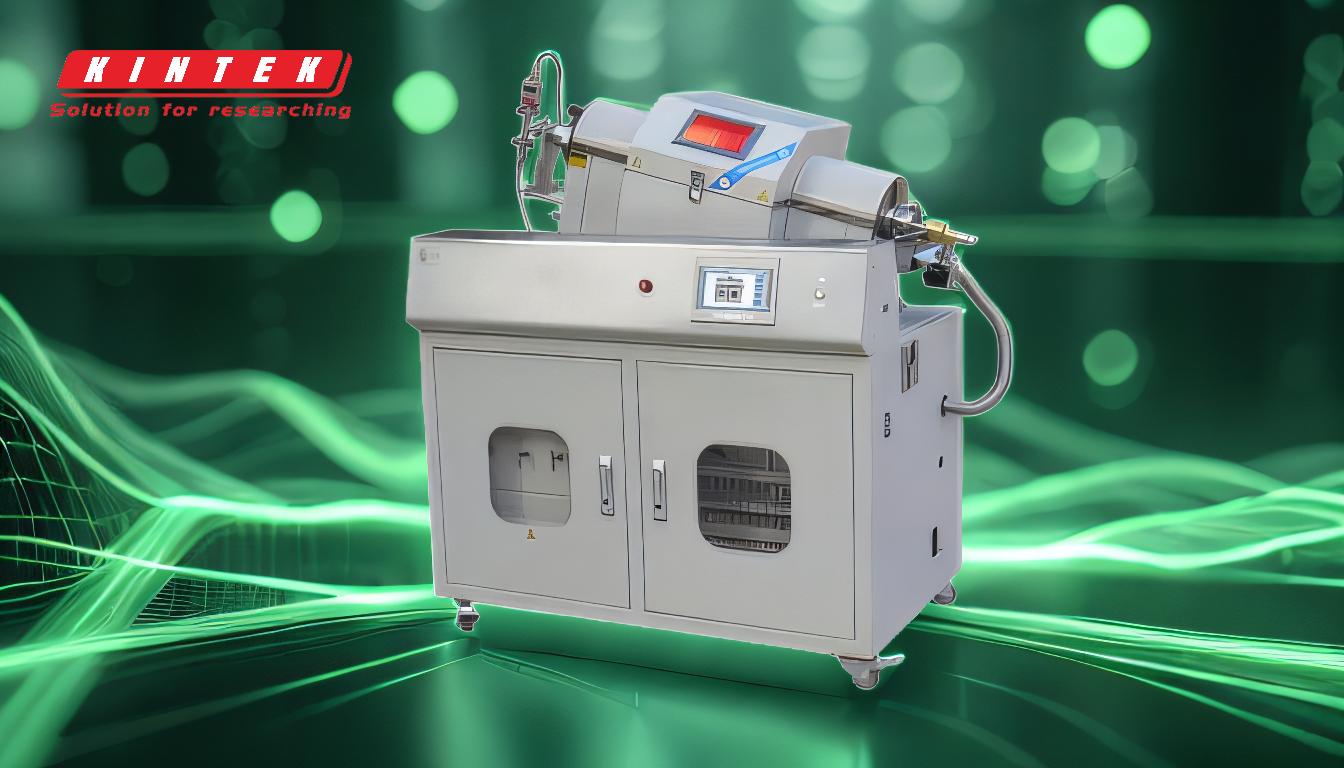
-
Step Coverage in Sputtering vs. Evaporation:
- Sputtering: Sputtering provides better step coverage due to the higher energy of sputtered atoms. These atoms are ejected from the target with significant kinetic energy, allowing them to adhere more uniformly to the substrate, even on complex or high-aspect-ratio features. This makes sputtering ideal for applications requiring precise and uniform thin films.
- Evaporation: Evaporation, particularly thermal evaporation, often struggles with step coverage. The evaporated atoms have lower energy and tend to deposit in a line-of-sight manner, leading to uneven coverage on non-planar surfaces or features with high aspect ratios.
-
Adhesion and Deposition Control:
- Sputtering: The higher energy of sputtered atoms results in better adhesion to the substrate. Additionally, sputtering allows for more control over the deposition process, including the ability to adjust parameters like pressure, power, and target material to achieve desired film properties.
- Evaporation: While evaporation can produce high-purity films, it offers less control over adhesion and deposition uniformity, especially on complex geometries.
-
Material Compatibility and Deposition Rate:
- Sputtering: Sputtering is compatible with a wide range of materials, including metals, alloys, and ceramics. However, it typically has a slower deposition rate compared to evaporation.
- Evaporation: Evaporation is faster and well-suited for materials with low melting points, but it may not be suitable for materials that require high-energy deposition for good adhesion.
-
Application-Specific Considerations:
- Sputtering: Preferred for applications requiring uniform thin films on complex geometries, such as semiconductor devices, optical coatings, and wear-resistant coatings.
- Evaporation: Often used in applications where high deposition rates and purity are prioritized, such as in the production of thin-film solar cells or decorative coatings.
-
Cost and Complexity:
- Sputtering: Generally more expensive and complex due to the need for vacuum systems, power supplies, and precise control mechanisms.
- Evaporation: Simpler and more cost-effective, making it a popular choice for less demanding applications.
In summary, sputtering is better than evaporation for step coverage due to its superior adhesion and control, especially for complex geometries. However, the choice between the two methods depends on the specific requirements of the application, including material compatibility, deposition rate, and cost constraints.
Summary Table:
Aspect | Sputtering | Evaporation |
---|---|---|
Step Coverage | Better due to higher energy of sputtered atoms, ideal for complex geometries. | Struggles with high-aspect-ratio features, uneven coverage on non-planar surfaces. |
Adhesion | Superior adhesion due to higher energy deposition. | Less control over adhesion, especially on complex geometries. |
Deposition Control | High control over parameters like pressure, power, and target material. | Limited control, primarily line-of-sight deposition. |
Material Compatibility | Wide range, including metals, alloys, and ceramics. | Best for low-melting-point materials, limited for high-energy adhesion. |
Deposition Rate | Slower but more precise. | Faster but less uniform. |
Applications | Semiconductor devices, optical coatings, wear-resistant coatings. | Thin-film solar cells, decorative coatings. |
Cost & Complexity | More expensive and complex due to vacuum systems and precise controls. | Simpler and more cost-effective for less demanding applications. |
Need help choosing the right deposition method for your application? Contact our experts today!