Sputtering is a widely used physical vapor deposition (PVD) technique for depositing thin films, offering advantages such as high precision, reproducibility, and compatibility with a broad range of materials. While sputtering is generally considered cost-effective compared to other deposition methods like E-Beam or thermal evaporation, its expense depends on factors such as the type of materials used, the complexity of the process, and the scale of production. Sputtering is particularly advantageous for depositing high-melting-point materials, achieving better adhesion, and producing uniform films with precise control over properties. However, the initial setup costs, maintenance, and energy consumption can influence its overall expense. For applications requiring high-quality, durable coatings, sputtering often provides a cost-efficient solution despite its higher upfront investment compared to simpler methods like gold plating.
Key Points Explained:
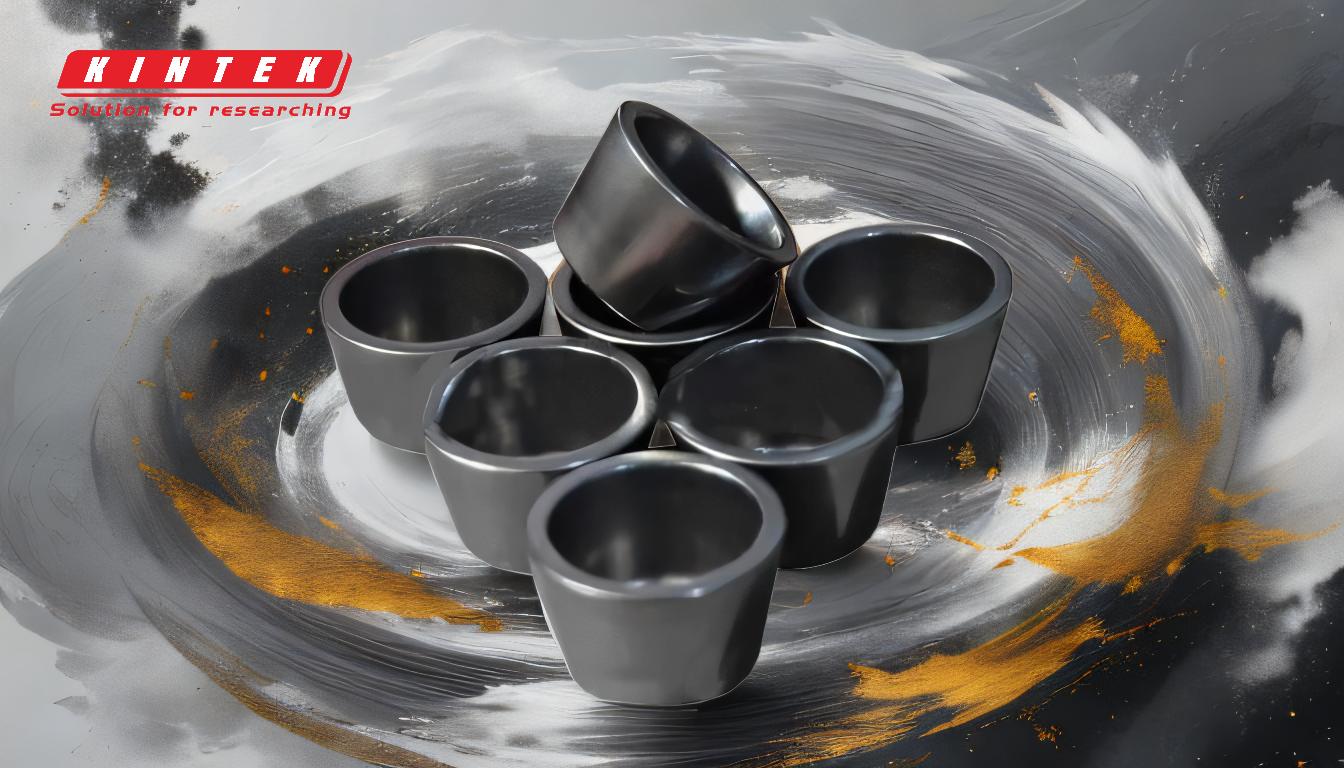
-
Cost Comparison with Other Deposition Methods:
- Sputtering is relatively inexpensive compared to other deposition techniques like E-Beam or thermal evaporation.
- It offers better reproducibility and simpler process automation, which can reduce long-term operational costs.
- Methods like gold plating, while cheaper upfront, result in softer and less durable coatings, making sputtering more cost-effective for high-performance applications.
-
Material Versatility and Efficiency:
- Sputtering can deposit materials with very high melting points, which are difficult or impossible to evaporate.
- It works well with a wide range of materials, including plastics, organics, glass, and metals, reducing the need for multiple deposition methods.
- The ability to deposit films with precise composition and properties minimizes material waste, enhancing cost efficiency.
-
Process Advantages and Cost Implications:
- Sputtering provides better adhesion and more uniform films, reducing the need for post-processing and improving yield.
- It is maintenance-free and compatible with reactive gases, lowering operational costs over time.
- The ability to perform sputtering in ultrahigh vacuum conditions ensures high-quality results, which can justify the higher initial investment.
-
Energy Consumption and Scale of Production:
- Sputtering requires significant energy, especially for high-melting-point materials, which can increase operational costs.
- For large-scale production, the cost per unit decreases due to economies of scale, making sputtering more affordable for industrial applications.
- Advanced processes like epitaxial growth and molecular-level precision can further enhance cost-effectiveness by reducing defects and improving performance.
-
Environmental and Long-Term Cost Benefits:
- Sputtering is more environmentally friendly compared to methods like gold plating, which involve harmful chemical processes.
- The durability and strength of sputtered coatings reduce the need for frequent replacements or repairs, offering long-term cost savings.
- The ability to control film properties precisely, such as color and hardness, adds value and reduces waste in applications like optical coatings or decorative finishes.
-
Initial Setup and Maintenance Costs:
- The initial investment for sputtering equipment can be high due to the need for specialized vacuum systems and target materials.
- However, the maintenance-free nature of the process and its compatibility with advanced technologies like reactive sputtering can offset these costs over time.
- For applications requiring high-quality, durable coatings, the higher upfront cost is often justified by the superior performance and longevity of sputtered films.
In summary, while sputtering may involve higher initial costs and energy consumption, its advantages in material versatility, process efficiency, and long-term durability make it a cost-effective choice for many applications, particularly those requiring high-performance coatings.
Summary Table:
Aspect | Details |
---|---|
Cost Comparison | Less expensive than E-Beam or thermal evaporation; better reproducibility. |
Material Versatility | Works with high-melting-point materials, plastics, organics, and metals. |
Process Advantages | Better adhesion, uniform films, and maintenance-free operation. |
Energy Consumption | High energy use but cost-effective at scale. |
Environmental Benefits | Eco-friendly compared to gold plating; durable coatings reduce waste. |
Setup and Maintenance Costs | Higher upfront investment but long-term savings due to durability. |
Interested in optimizing your thin film deposition process? Contact us today to learn how sputtering can benefit your application!