Sputtering is a subset of Physical Vapor Deposition (PVD), but they are not the same. PVD encompasses a broader range of techniques, including sputtering, evaporation, and other methods, all aimed at depositing thin films onto substrates. Sputtering specifically involves using plasma to bombard a target material, causing atoms to be ejected and deposited onto a substrate. This method is known for its ability to produce high-quality, dense films with reduced residual stress, especially at lower temperatures. While sputtering is a widely used and economical PVD technique, it is just one of several methods within the PVD category, each with its own unique processes and applications.
Key Points Explained:
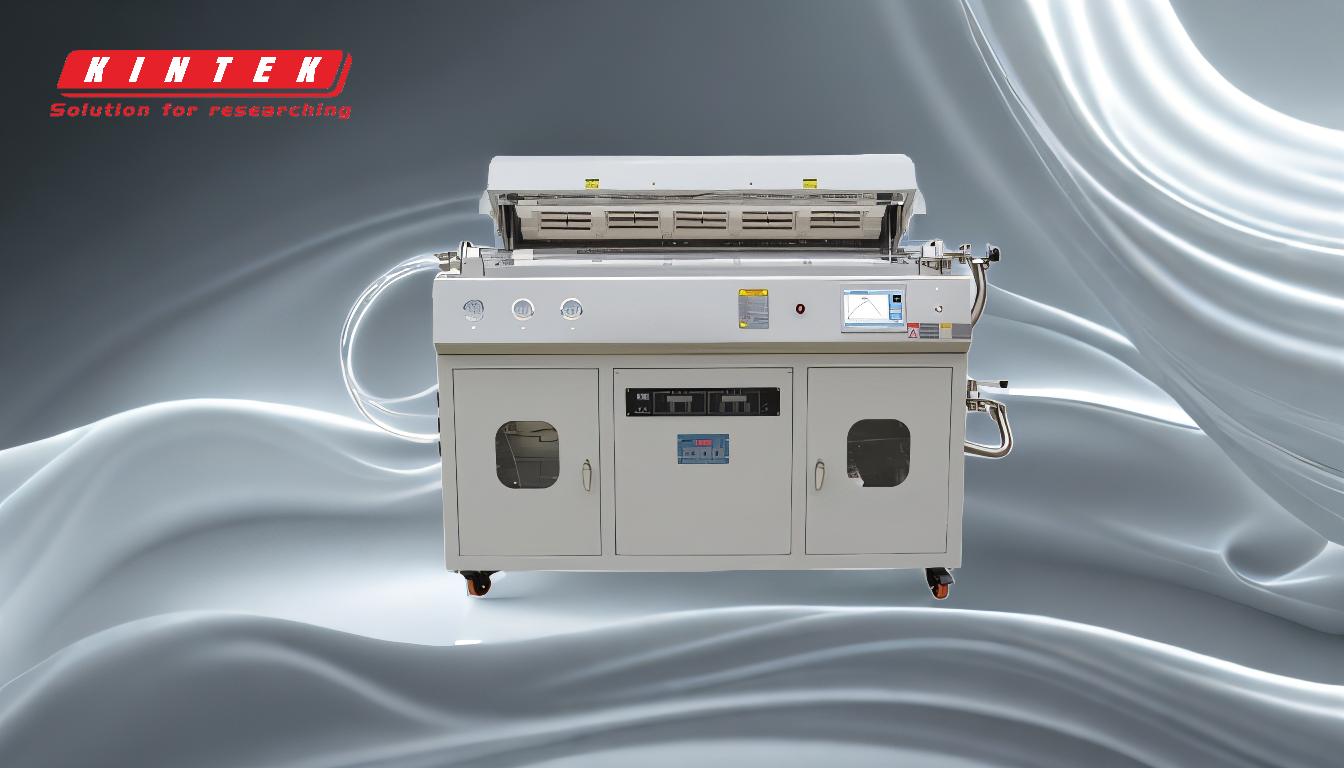
-
Sputtering is a Type of PVD:
- Sputtering is one of several techniques within the broader category of Physical Vapor Deposition (PVD). PVD includes methods like evaporation, sputtering, and others, all of which involve the deposition of thin films onto substrates. Sputtering, however, specifically uses plasma to eject atoms from a target material, which are then deposited onto a substrate.
-
Mechanism of Sputtering:
- In sputtering, plasma is generated, typically containing argon ions and electrons. These high-energy ions bombard the target material, causing atoms to be ejected through a process known as atomic collision cascades. These ejected atoms then travel through the plasma and form a thin film on the substrate. This method allows for excellent control over film quality and density.
-
Types of Sputtering:
- There are several types of sputtering techniques, including:
- Diode Sputtering: The simplest form, using a direct current (DC) to generate plasma.
- Reactive Sputtering: Involves a reactive gas that reacts with the sputtered material to form a compound film.
- Bias Sputtering: Applies a bias voltage to the substrate to improve film adhesion and density.
- Magnetron Sputtering: Uses magnetic fields to confine electrons near the target, increasing ionization efficiency and deposition rates.
- Ion-Beam Sputtering: Produces high-quality, uniform films but is more complex and costly.
- There are several types of sputtering techniques, including:
-
Advantages of Sputtering:
- High-Quality Films: Sputtering can produce dense, high-quality films with reduced residual stress, especially at lower deposition temperatures.
- Versatility: It can deposit a wide range of materials on various substrates.
- Economic: Sputtering is one of the most economical deposition methods within PVD, making it a standard technique in many industries.
-
Comparison with Other PVD Methods:
- Evaporation: Unlike sputtering, evaporation relies on heating the source material past its vaporization temperature to create a vapor that condenses on the substrate. Evaporation offers higher deposition rates but may not achieve the same film quality as sputtering.
- Ion-Beam Sputtering: This method produces better film quality and uniformity compared to standard sputtering but is more costly and complex.
- Magnetron Sputtering: Ideal for highly automated, high-volume production, particularly for thin films with short deposition times.
-
Applications of Sputtering:
- Sputtering is widely used in industries such as semiconductor manufacturing, optics, and decorative coatings. It is particularly valued for its ability to deposit a multitude of different materials on a wide variety of substrates, making it a versatile and essential technique in modern manufacturing.
In summary, while sputtering is a key technique within the PVD category, it is distinct in its mechanism and advantages. Understanding these differences is crucial for selecting the appropriate deposition method for specific applications.
Summary Table:
Aspect | Sputtering | Other PVD Methods |
---|---|---|
Mechanism | Uses plasma to bombard target material, ejecting atoms for deposition. | Includes evaporation, ion-beam sputtering, and more. |
Film Quality | Produces dense, high-quality films with reduced residual stress. | Evaporation offers higher deposition rates but may lack film quality. |
Versatility | Can deposit a wide range of materials on various substrates. | Depends on the specific PVD method used. |
Cost | Economical and widely used in many industries. | Ion-beam sputtering is more costly but produces superior film quality and uniformity. |
Applications | Used in semiconductor manufacturing, optics, and decorative coatings. | Other PVD methods are tailored for specific industrial needs. |
Discover the right deposition method for your project—contact our experts today!