Sputtering and evaporation are both Physical Vapor Deposition (PVD) techniques used to deposit thin films onto substrates, but they differ significantly in their mechanisms and applications. Sputtering involves the ejection of atoms from a target material when struck by high-energy particles, typically in a high vacuum environment. This method provides better step coverage and adhesion, making it ideal for applications requiring precise and uniform coatings. Evaporation, on the other hand, involves heating the source material until it vaporizes, allowing the vapor to diffuse through a vacuum and condense on the substrate. While evaporation can achieve higher deposition rates, it is less versatile in terms of material options and adhesion quality compared to sputtering. Both methods are essential in various industries, but the choice between them depends on the specific requirements of the application.
Key Points Explained:
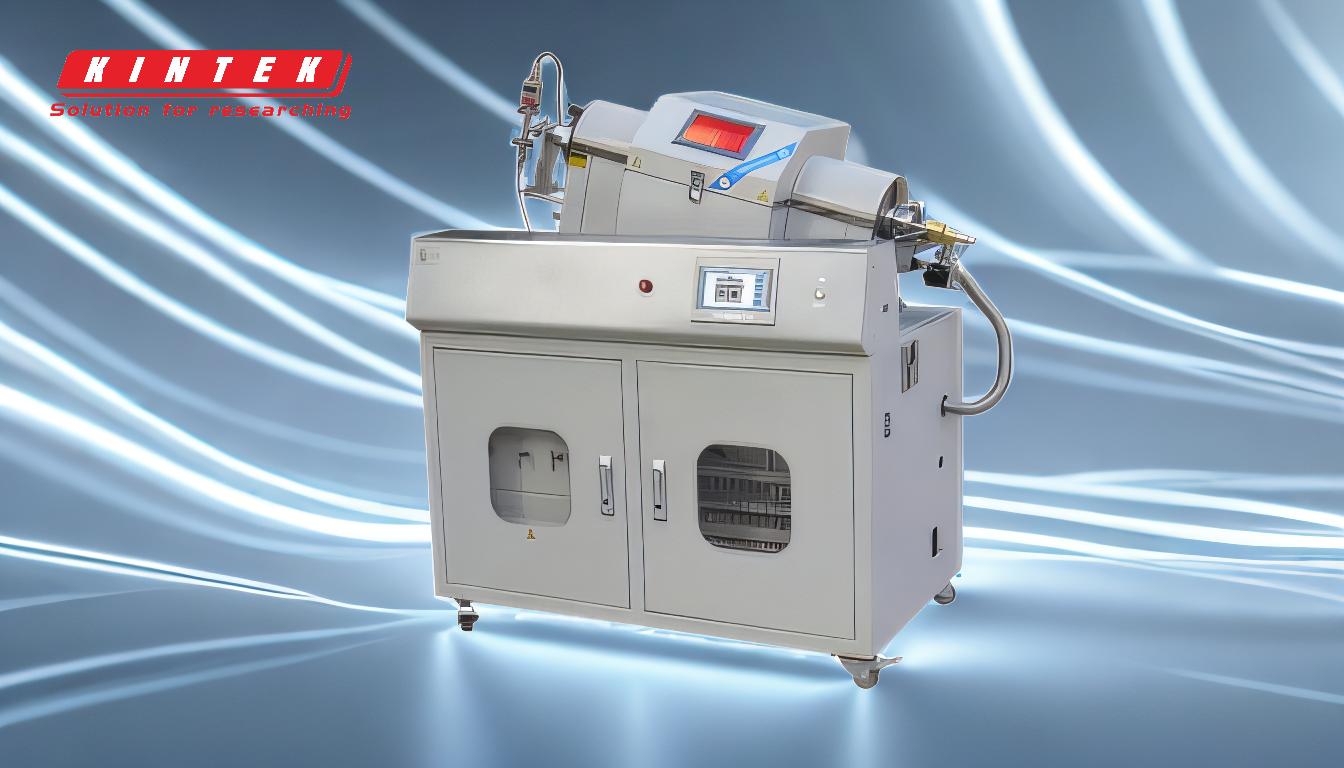
-
Mechanism of Sputtering:
- Sputtering is a PVD process where high-energy particles collide with a target material, causing atoms to be ejected from its surface. These atoms then travel through a vacuum and deposit onto a substrate, forming a thin film.
- This method is highly controlled and allows for precise deposition, making it suitable for applications requiring uniformity and strong adhesion.
-
Mechanism of Evaporation:
- Evaporation involves heating the source material until it reaches its vaporization temperature. The resulting vapor diffuses through a vacuum and condenses on the substrate, forming a thin film.
- This process is generally faster than sputtering but may lack the uniformity and adhesion strength provided by sputtering.
-
Step Coverage and Adhesion:
- Sputtering is preferred in applications where step coverage (the ability to coat uneven surfaces uniformly) and adhesion are critical. The energetic nature of sputtered atoms ensures better coverage of complex geometries and stronger bonding to the substrate.
- Evaporation, while faster, may struggle with step coverage and adhesion, particularly on surfaces with intricate features.
-
Material Versatility:
- Sputtering offers greater versatility in terms of material options and color modulation. It can deposit a wide range of materials, including metals, alloys, and ceramics, with varying colors and properties.
- Evaporation is more limited, often restricted to materials that can be easily vaporized, such as aluminum, and may require additional processes (e.g., spray painting) to achieve desired colors.
-
Deposition Rates:
- Evaporation typically achieves higher deposition rates due to the robust vapor stream produced during heating. This makes it suitable for applications where speed is a priority.
- Sputtering, while slower, provides more controlled and consistent deposition, which is essential for high-precision applications.
-
Applications:
- Sputtering is widely used in industries such as semiconductor manufacturing, optics, and decorative coatings, where precision and durability are paramount.
- Evaporation is often employed in applications like metallization of plastics, solar cell production, and simple decorative coatings, where speed and cost-effectiveness are more critical than precision.
In summary, while both sputtering and evaporation are integral to PVD, they serve different purposes based on the specific requirements of the application. Sputtering excels in precision, adhesion, and material versatility, whereas evaporation offers speed and simplicity. Understanding these differences allows for the selection of the most appropriate technique for a given task.
Summary Table:
Aspect | Sputtering | Evaporation |
---|---|---|
Mechanism | High-energy particles eject atoms from a target material. | Source material is heated until it vaporizes and condenses on the substrate. |
Step Coverage | Excellent for uniform coatings on complex geometries. | Struggles with step coverage on intricate surfaces. |
Adhesion | Stronger adhesion due to energetic atom deposition. | Adhesion is weaker compared to sputtering. |
Material Versatility | Can deposit a wide range of materials, including metals, alloys, and ceramics. | Limited to easily vaporized materials like aluminum. |
Deposition Rate | Slower but more controlled. | Faster due to robust vapor stream. |
Applications | Ideal for semiconductor manufacturing, optics, and decorative coatings. | Used in metallization of plastics, solar cells, and simple decorative coatings. |
Still unsure which PVD technique is right for your application? Contact our experts today for personalized advice!