Yes, tungsten is indeed used in heating elements, particularly in high-temperature applications where its unique properties are advantageous. Tungsten has an exceptionally high melting point (3422°C), making it suitable for environments requiring extreme heat. It is commonly used in vacuum furnaces, semiconductor manufacturing, and other industrial processes where temperatures exceed 2000°C. However, tungsten heating elements are prone to embrittlement and oxidation at high temperatures, so they must be operated in controlled environments, such as vacuum or inert gas atmospheres, to prevent degradation. Its fast heating, precise temperature control, and long service life make it a preferred choice for specialized heating applications.
Key Points Explained:
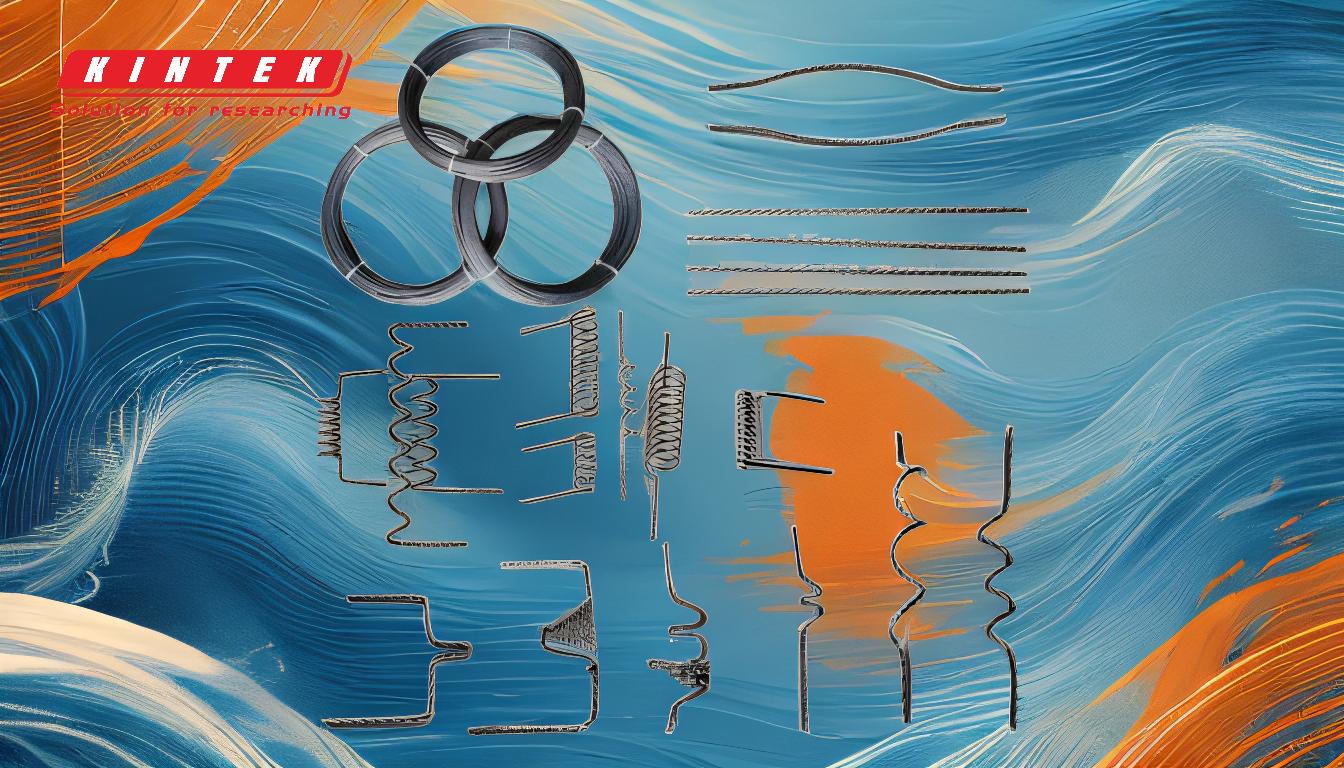
-
High-Temperature Capability:
- Tungsten has the highest melting point of all metals (3422°C), making it ideal for heating elements in extreme environments.
- Tungsten mesh heating elements can operate at a maximum temperature of 2400°C, with a long-term use temperature of 2300°C, which is significantly higher than many other materials.
-
Fast Heating and Precise Control:
- Tungsten heating elements provide rapid heating due to their excellent thermal conductivity and efficient energy transfer.
- The heating process involves the transfer of kinetic energy from electrons to tungsten atoms, generating heat that warms the surrounding chamber. This ensures precise temperature control, which is critical in applications like semiconductor manufacturing and vacuum metallizing.
-
Durability and Long Service Life:
- Tungsten is highly durable and resistant to corrosion, making it suitable for long-term use in harsh environments.
- Its dimensional stability at high temperatures ensures consistent performance over time, reducing the need for frequent replacements.
-
Challenges and Limitations:
- Tungsten heating elements are susceptible to embrittlement, especially when exposed to mechanical or thermal shock.
- Oxidation is a significant concern; tungsten must not be exposed to air above 500°C (932°F) to avoid degradation. This necessitates the use of controlled atmospheres, such as vacuum or inert gas environments.
- A ramping temperature control system is required during cold start-up to prevent embrittlement and ensure safe operation.
-
Applications in High-Temperature Processes:
- Tungsten heating elements are widely used in industries such as vacuum metallizing, the glass industry, and semiconductor manufacturing.
- In these applications, tungsten's ability to withstand extreme temperatures and maintain dimensional stability is critical. For example, tungsten boats are often used in evaporation processes due to their high melting point and resistance to thermal stress.
-
Comparison with Other Materials:
- While tungsten is preferred for its high-temperature capabilities, materials like molybdenum are used in applications where lower melting points and easier processing are advantageous.
- Tungsten carbide, a compound of tungsten, is also used in industrial machinery and cutting tools due to its hardness and wear resistance, but it is not typically used in heating elements.
In summary, tungsten is a highly effective material for heating elements in high-temperature applications, offering fast heating, precise control, and durability. However, its use requires careful handling and controlled environments to mitigate risks such as embrittlement and oxidation. Its unique properties make it indispensable in industries where extreme heat and precision are essential.
Summary Table:
Key Feature | Details |
---|---|
Melting Point | 3422°C, the highest among metals |
Operating Temperature | Up to 2400°C (max), 2300°C (long-term) |
Heating Speed | Fast heating due to excellent thermal conductivity |
Durability | Highly durable, corrosion-resistant, and dimensionally stable at high temps |
Challenges | Prone to embrittlement and oxidation; requires controlled atmospheres |
Applications | Vacuum furnaces, semiconductor manufacturing, glass industry |
Interested in tungsten heating elements for your high-temperature applications? Contact us today to learn more!