Powder metallurgy (PM) offers significant advantages over traditional manufacturing processes, making it a preferred choice for many industries. It is a green manufacturing technology characterized by a short process, energy efficiency, low cost, and minimal material waste. PM allows for precise control over material properties by freely assembling material structures, making it ideal for producing complex and high-performance parts. It is particularly beneficial for materials with high melting points, large differences in melting points of constituent elements, and poor castability. Additionally, PM provides high process control, exceptional tolerances, and the ability to produce intricate parts economically, making it widely used in automotive and aerospace industries. Its eco-friendly nature, with 97% material utilization, further enhances its appeal.
Key Points Explained:
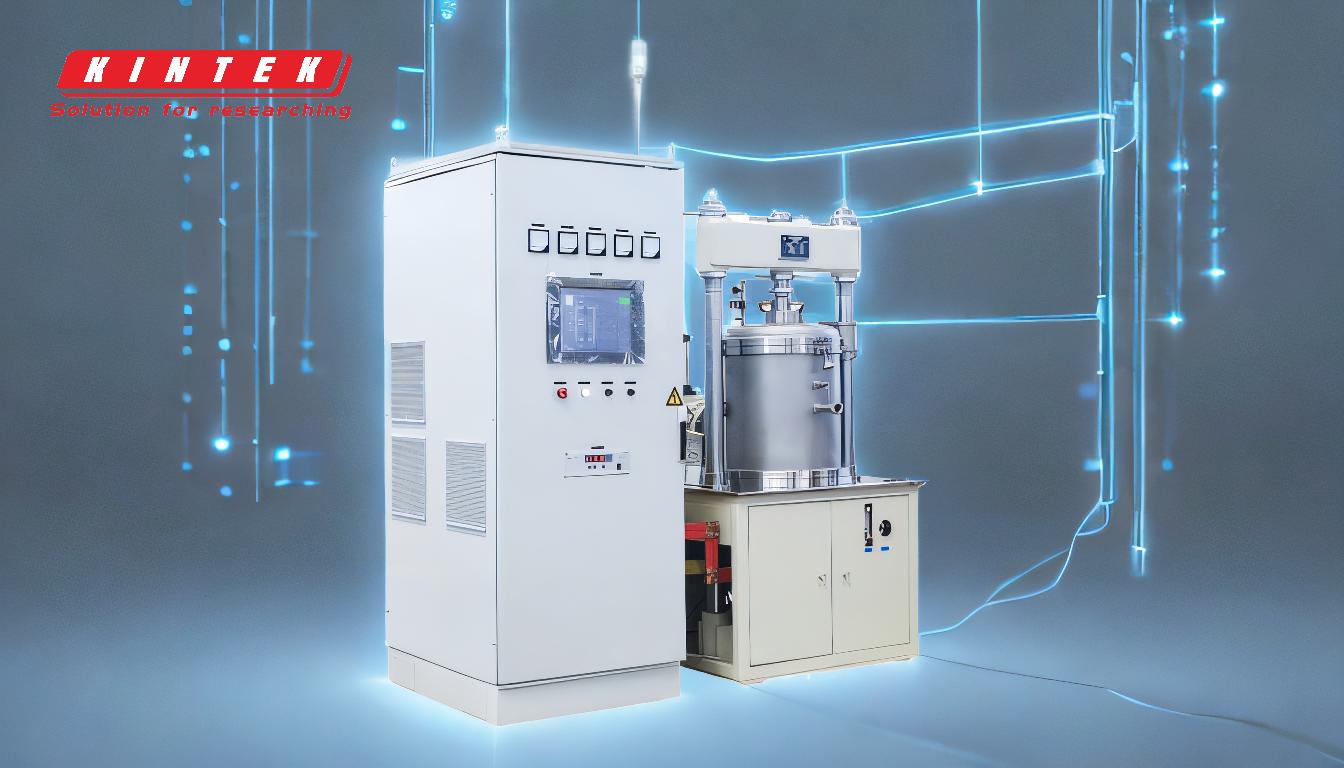
-
Short Process and Energy Efficiency
- Powder metallurgy involves fewer steps compared to traditional manufacturing methods like casting or forging. This streamlined process reduces energy consumption and production time.
- The sintering process in PM occurs at lower temperatures than melting in traditional methods, further contributing to energy savings.
-
Cost-Effectiveness
- PM minimizes material waste, as 97% of the powder used becomes part of the final product. This high material utilization reduces raw material costs.
- The ability to produce near-net-shape parts reduces the need for secondary machining, lowering labor and equipment costs.
-
Precision and Control Over Material Properties
- PM allows for the precise blending of powders to create custom material compositions, enabling the production of parts with tailored mechanical, thermal, and electrical properties.
- The process ensures uniform density and microstructure, resulting in parts with consistent performance and exceptional tolerances.
-
Ability to Handle Complex Materials
- PM is particularly advantageous for materials with high melting points, such as tungsten or molybdenum, which are difficult to process using traditional methods.
- It can also handle materials with large differences in melting points or poor castability, such as metal-ceramic composites, which are challenging to produce through other methods.
-
Eco-Friendly Manufacturing
- PM is a sustainable manufacturing method, producing minimal waste and emissions. The high material utilization rate (97%) aligns with green manufacturing principles.
- The process does not involve harmful chemicals or excessive energy consumption, making it environmentally friendly.
-
Versatility in Applications
- PM is widely used in industries such as automotive, aerospace, and electronics due to its ability to produce intricate and high-performance parts.
- It is suitable for mass production as well as small-batch manufacturing, offering flexibility to meet diverse application requirements.
-
High Process Efficiency
- The sintering process in PM is rapid, with short sintering times and high compactness, ensuring efficient production cycles.
- The ability to produce complex geometries in a single step reduces the need for multiple manufacturing processes, further enhancing efficiency.
-
Superior Part Quality
- PM produces homogenous and uniform parts with consistent mechanical properties, ensuring reliability and durability.
- The process eliminates common defects associated with casting, such as porosity and shrinkage, resulting in higher-quality parts.
In summary, powder metallurgy stands out as a superior manufacturing process due to its efficiency, cost-effectiveness, precision, and environmental benefits. Its ability to handle complex materials and produce high-quality parts makes it a vital technology in modern manufacturing.
Summary Table:
Advantage | Description |
---|---|
Short Process | Fewer steps, reduced energy consumption, and faster production times. |
Cost-Effectiveness | 97% material utilization, minimal waste, and reduced machining costs. |
Precision and Control | Custom material compositions and uniform density for consistent performance. |
Handles Complex Materials | Ideal for high-melting-point materials, metal-ceramic composites, and more. |
Eco-Friendly | Sustainable process with minimal waste, emissions, and energy consumption. |
Versatility | Used in automotive, aerospace, and electronics for intricate, high-performance parts. |
High Efficiency | Rapid sintering and single-step production of complex geometries. |
Superior Quality | Homogeneous parts with consistent properties and no casting defects. |
Unlock the potential of powder metallurgy for your manufacturing needs—contact us today to learn more!