Melting and pouring of casting in a vacuum environment offers significant advantages, primarily due to the controlled atmosphere that eliminates contamination and enhances the purity and properties of the metal. Key benefits include improved degassing, reduction of impurities, better control of reactive elements, and enhanced mechanical properties. The vacuum environment prevents re-oxidation, reduces harmful elements, and improves the metal's surface finish, machining characteristics, and overall performance. Additionally, vacuum melting supports environmental protection by minimizing heat loss and preventing pollution from gas-phase interactions.
Key Points Explained:
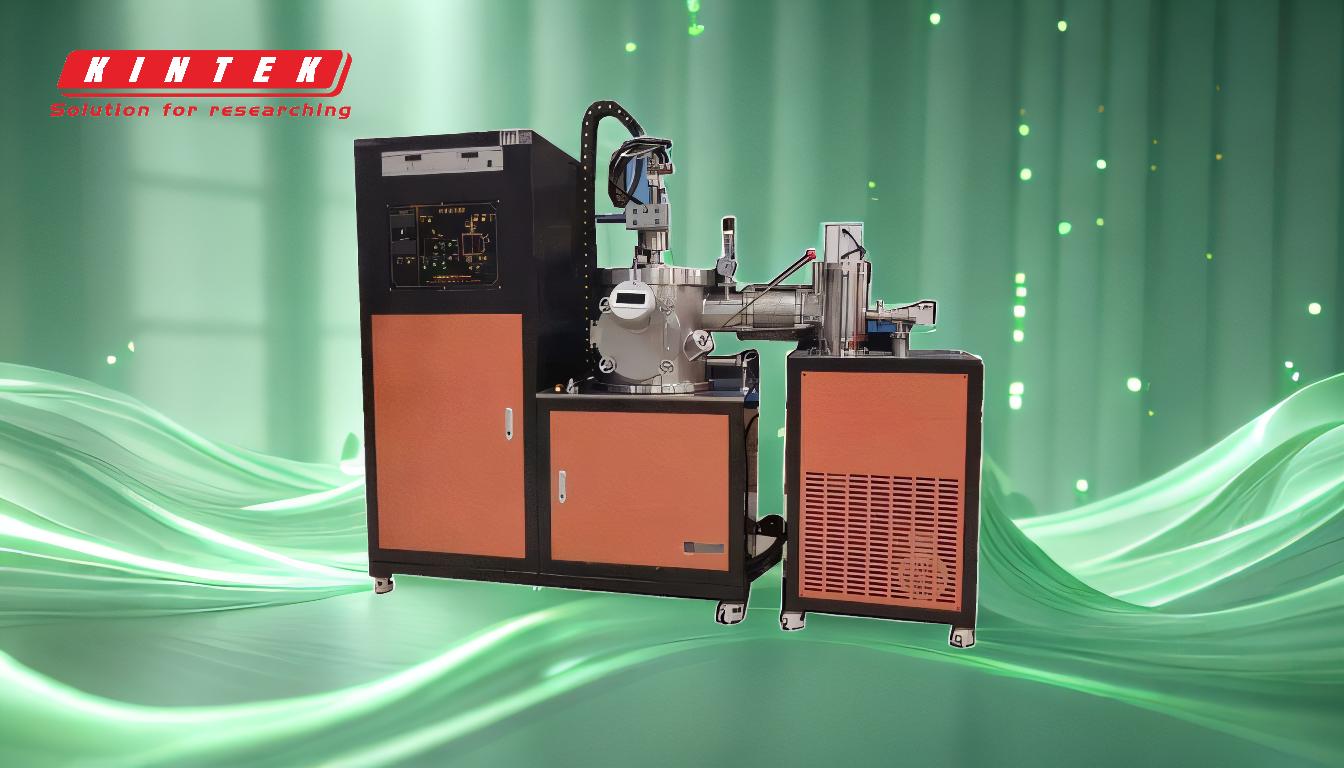
-
Vacuum Degassing and Impurity Reduction:
- Degassing: Vacuum melting effectively removes gases like hydrogen, nitrogen, and oxygen from the molten metal. This process, known as degassing, significantly reduces the risk of porosity and gas-related defects in the final cast product.
- Reduction of Tramp Elements: Harmful impurities such as lead, bismuth, silver, and other low-melting-point metals are reduced. The vacuum environment allows for the evaporation of these elements, leading to a purer metal.
- Deoxidation: The combination of vacuum and carbon-oxygen (C-O) reaction facilitates deoxidation. Carbon acts as a strong deoxidizer, and the resulting CO gas is continuously pumped out, preventing contamination from metal deoxidizers.
-
Improved Mechanical and Physical Properties:
- Enhanced Toughness and Fatigue Strength: The removal of impurities and better control of reactive elements like aluminum, titanium, and zirconium improve the metal's toughness and fatigue resistance.
- Better Corrosion Resistance and High-Temperature Performance: Vacuum melting enhances the metal's ability to withstand corrosive environments and high-temperature conditions, such as creep resistance.
- Superior Surface Finish and Machinability: The absence of impurities and oxides results in a smoother surface finish and better machining characteristics, reducing post-processing efforts.
-
Environmental and Process Advantages:
- Prevention of Re-oxidation: The vacuum environment prevents active metals from re-oxidizing, ensuring the integrity of the molten metal.
- Heat Loss Reduction: Vacuum conditions minimize heat loss, improving energy efficiency during the melting process.
- Pollution Control: By eliminating gas-phase interactions, vacuum melting reduces environmental pollution and ensures a cleaner production process.
-
Control of Reactive Elements:
- Reactive elements such as aluminum, titanium, boron, and zirconium can be precisely controlled in a vacuum environment. This control leads to improved magnetic properties, better alloy homogeneity, and enhanced performance in critical applications.
-
Decarburization and Desulfurization:
- Decarburization: The vacuum environment facilitates the removal of carbon, which is particularly beneficial for producing low-carbon steels and alloys.
- Desulfurization: Sulfur content is reduced, further enhancing the metal's purity and performance.
In summary, vacuum melting and pouring provide a superior method for producing high-quality castings with enhanced mechanical properties, reduced impurities, and improved environmental sustainability. This process is particularly advantageous for industries requiring high-performance materials, such as aerospace, automotive, and energy sectors.
Summary Table:
Advantage | Description |
---|---|
Degassing & Impurity Reduction | Removes gases and harmful impurities, reducing porosity and defects. |
Improved Mechanical Properties | Enhances toughness, fatigue strength, and corrosion resistance. |
Superior Surface Finish | Smoother surface and better machinability due to fewer impurities. |
Environmental Benefits | Minimizes heat loss, prevents pollution, and ensures cleaner production. |
Control of Reactive Elements | Precise control of elements like aluminum and titanium for better alloy quality. |
Decarburization & Desulfurization | Reduces carbon and sulfur content, improving metal purity. |
Unlock the benefits of vacuum melting for your applications—contact our experts today to learn more!