The speed of a hydraulic motor is influenced by several factors, including the flow rate of hydraulic fluid, the motor's displacement, system pressure, and mechanical efficiency. Flow rate directly determines how fast the motor can turn, while displacement affects the motor's torque and speed relationship. System pressure impacts the motor's ability to overcome load, and mechanical efficiency accounts for losses due to friction and internal leakage. Understanding these factors helps in optimizing hydraulic motor performance for specific applications.
Key Points Explained:
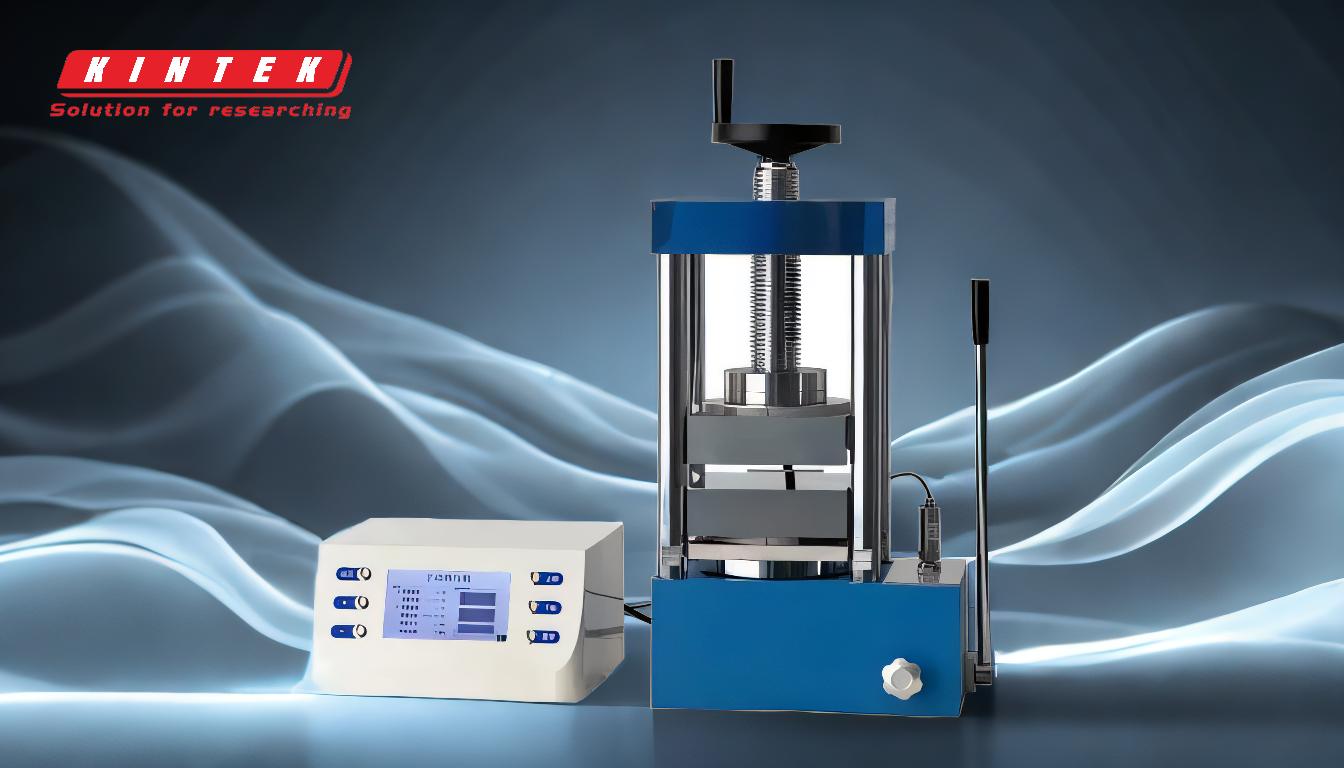
-
Flow Rate of Hydraulic Fluid:
- The speed of a hydraulic motor is directly proportional to the flow rate of the hydraulic fluid entering the motor. Higher flow rates result in faster motor speeds, while lower flow rates slow the motor down.
- Flow rate is typically controlled by the hydraulic pump and valves in the system. Adjusting these components can fine-tune the motor's speed.
-
Motor Displacement:
- Displacement refers to the volume of fluid required to turn the motor's output shaft by one revolution. Motors with higher displacement require more fluid to achieve the same speed, resulting in lower RPMs at a given flow rate.
- Conversely, motors with lower displacement can achieve higher speeds with the same flow rate. This relationship is crucial when selecting a motor for applications requiring specific speed and torque characteristics.
-
System Pressure:
- System pressure affects the motor's ability to overcome load resistance. Higher pressure allows the motor to generate more torque, which can influence speed under load.
- However, excessive pressure can lead to inefficiencies or damage, so it's essential to operate within the motor's rated pressure range.
-
Mechanical Efficiency:
- Mechanical efficiency accounts for energy losses due to friction, internal leakage, and other factors. A motor with higher efficiency will convert more hydraulic energy into mechanical motion, resulting in better speed performance.
- Regular maintenance, such as ensuring proper lubrication and minimizing wear, can help maintain high mechanical efficiency.
-
Load Characteristics:
- The load on the motor directly impacts its speed. Heavy loads require more torque, which can reduce speed if the motor's displacement or system pressure is insufficient.
- Understanding the load profile is essential for selecting a motor that can maintain the desired speed under varying conditions.
-
Fluid Viscosity and Temperature:
- Hydraulic fluid viscosity changes with temperature, affecting flow resistance and motor performance. Higher viscosity at lower temperatures can reduce flow rate and, consequently, motor speed.
- Maintaining optimal fluid temperature through proper system design and cooling mechanisms ensures consistent motor performance.
By considering these factors, you can optimize the speed of a hydraulic motor for your specific application, ensuring efficient and reliable operation.
Summary Table:
Factor | Impact on Motor Speed |
---|---|
Flow Rate | Directly proportional: higher flow = faster speed, lower flow = slower speed. |
Motor Displacement | Higher displacement = lower speed at a given flow rate; lower displacement = higher speed. |
System Pressure | Higher pressure = more torque, but excessive pressure can reduce efficiency or cause damage. |
Mechanical Efficiency | Higher efficiency = better speed performance; regular maintenance is key. |
Load Characteristics | Heavy loads = reduced speed if displacement or pressure is insufficient. |
Fluid Viscosity | Higher viscosity = reduced flow rate and slower speed; temperature control is crucial. |
Need help optimizing your hydraulic motor's speed? Contact our experts today for tailored solutions!