Leak detection is a critical process in various industries, especially when dealing with sensitive equipment like PECVD equipment. Acceptable methods of leak detection typically involve a combination of visual inspections, pressure testing, and the use of specialized tools such as helium leak detectors or ultrasonic leak detectors. These methods ensure that even the smallest leaks are identified, which is crucial for maintaining the integrity and performance of systems. The choice of method depends on the type of system, the sensitivity required, and the environment in which the equipment operates.
Key Points Explained:
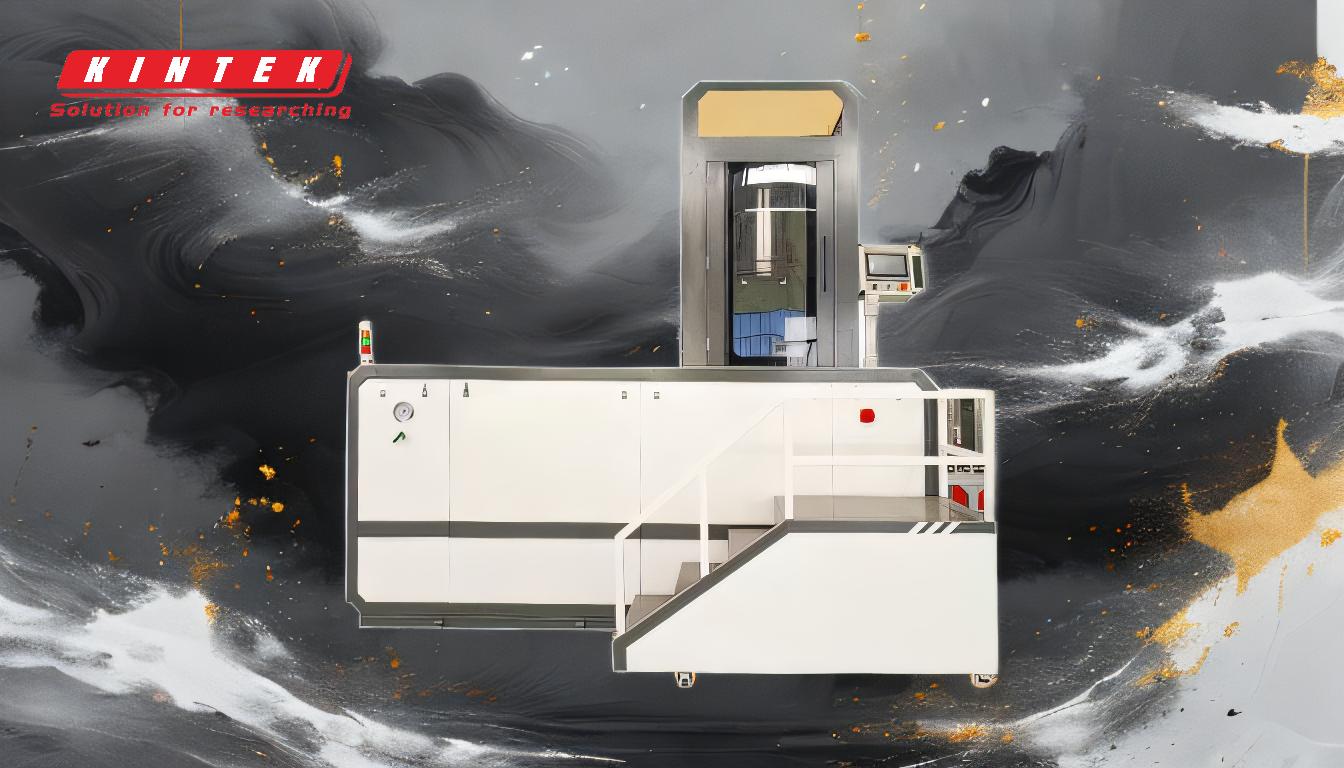
-
Visual Inspection:
- Description: This is the most basic form of leak detection, involving a thorough visual examination of the equipment for any signs of leakage, such as stains, corrosion, or physical damage.
- Application: Useful for initial checks and in environments where leaks are likely to be visible.
- Limitations: Not effective for detecting very small or internal leaks.
-
Pressure Testing:
- Description: This method involves pressurizing the system and monitoring the pressure over time to detect any drops that would indicate a leak.
- Types: Includes both static and dynamic pressure testing.
- Application: Commonly used in pipelines, HVAC systems, and other pressurized systems.
- Advantages: Can detect leaks in systems that are not easily accessible for visual inspection.
-
Helium Leak Detection:
- Description: Helium is used as a tracer gas because it is inert, non-toxic, and has a small molecular size, making it ideal for detecting very small leaks.
- Process: The system is pressurized with helium, and a helium leak detector is used to sniff out any escaping gas.
- Application: Highly effective in vacuum systems, such as those used in PECVD equipment.
- Advantages: Extremely sensitive and can detect leaks that other methods might miss.
-
Ultrasonic Leak Detection:
- Description: This method uses ultrasonic sensors to detect the high-frequency sounds produced by gas or liquid escaping from a leak.
- Process: The sensor is moved around the equipment, and any ultrasonic signals are detected and analyzed.
- Application: Useful in noisy environments where other methods might be less effective.
- Advantages: Can detect leaks in real-time and is non-invasive.
-
Bubble Testing:
- Description: A simple method where a soap solution is applied to the suspected area, and the formation of bubbles indicates a leak.
- Application: Often used for quick checks on gas lines and fittings.
- Limitations: Not suitable for detecting very small leaks or in hard-to-reach areas.
-
Dye Penetrant Testing:
- Description: A dye is applied to the surface, and after a certain period, the excess is removed. Any remaining dye in cracks or leaks is then visible under UV light.
- Application: Used for detecting surface-breaking defects in non-porous materials.
- Advantages: Simple and effective for surface leaks.
-
Thermal Imaging:
- Description: Uses infrared cameras to detect temperature differences caused by escaping gases or liquids.
- Application: Useful in large systems where leaks might cause localized cooling or heating.
- Advantages: Can cover large areas quickly and is non-contact.
-
Mass Spectrometry:
- Description: A highly sensitive method that ionizes gas molecules and detects them based on their mass-to-charge ratio.
- Application: Used in high-vacuum systems and critical applications where even the smallest leaks must be detected.
- Advantages: Extremely precise and can identify the type of gas leaking.
Each of these methods has its own strengths and is chosen based on the specific requirements of the system being tested. For PECVD equipment, methods like helium leak detection and ultrasonic leak detection are often preferred due to their high sensitivity and ability to detect even the smallest leaks, which are crucial for maintaining the vacuum integrity necessary for the process.
Summary Table:
Method | Description | Application | Advantages |
---|---|---|---|
Visual Inspection | Basic examination for visible signs of leakage (stains, corrosion, damage). | Initial checks in environments where leaks are likely visible. | Simple and cost-effective. |
Pressure Testing | Pressurizes the system to monitor pressure drops indicating leaks. | Pipelines, HVAC systems, and pressurized systems. | Detects leaks in inaccessible areas. |
Helium Leak Detection | Uses helium as a tracer gas to detect small leaks. | Vacuum systems like PECVD equipment. | Highly sensitive and detects tiny leaks. |
Ultrasonic Detection | Detects high-frequency sounds from escaping gas or liquid. | Noisy environments where other methods may fail. | Real-time detection and non-invasive. |
Bubble Testing | Applies soap solution to identify leaks through bubble formation. | Quick checks on gas lines and fittings. | Simple and quick for surface-level leaks. |
Dye Penetrant Testing | Uses dye to reveal surface-breaking defects under UV light. | Non-porous materials with surface leaks. | Effective for visible surface leaks. |
Thermal Imaging | Detects temperature differences caused by leaks using infrared cameras. | Large systems with localized cooling or heating. | Covers large areas quickly and is non-contact. |
Mass Spectrometry | Ionizes gas molecules to detect leaks based on mass-to-charge ratio. | High-vacuum systems and critical applications. | Extremely precise and identifies gas type. |
Need help choosing the right leak detection method for your equipment? Contact our experts today for tailored solutions!