Induction furnaces are primarily made of three key components: a power supply, an induction coil (or ring), and a crucible constructed from refractory materials. The power supply generates the necessary electrical energy, which is transferred to the induction coil to create a magnetic field. This magnetic field induces eddy currents in the metal charge placed within the crucible, causing it to heat up and melt. The crucible, made of durable refractory materials, withstands high temperatures and contains the molten metal. Additional components, such as insulation materials, cooling systems, and capacitors, enhance the furnace's efficiency and durability.
Key Points Explained:
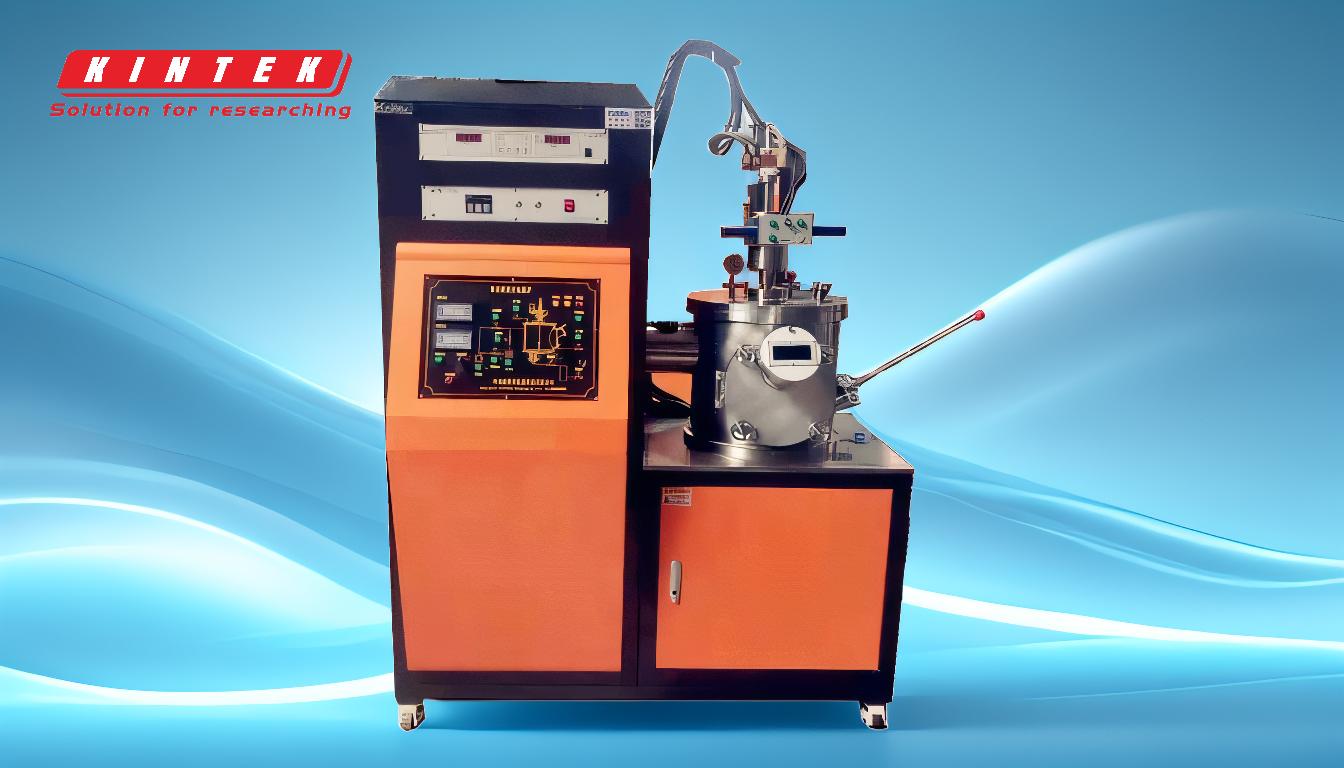
-
Power Supply
- The power supply is the core component that provides the electrical energy required for the furnace to operate.
- It typically includes an intermediate frequency power supply, often operating at frequencies like 2500 Hz for aluminum melting furnaces.
- The power supply ensures the generation of a stable magnetic field through the induction coil, which is essential for efficient heating.
-
Induction Coil (or Induction Ring)
- The induction coil is a critical part of the furnace, responsible for generating the magnetic field that induces eddy currents in the metal charge.
- It is usually made of copper or another highly conductive material to minimize energy loss.
- The coil is often water-cooled to prevent overheating during operation, ensuring longevity and consistent performance.
-
Crucible
- The crucible is the container that holds the metal charge during the melting process.
- It is constructed from refractory materials, such as high-purity alumina or other ceramics, which can withstand extreme temperatures and resist chemical corrosion.
- The crucible's design ensures that it can contain molten metal without degrading, even under prolonged exposure to high heat.
-
Refractory Materials
- Refractory materials are used extensively in the construction of the crucible and other furnace components.
- These materials include high-purity alumina fiber insulation, Morgan materials brick, and lightweight refractory bricks.
- They provide excellent thermal insulation, durability, and resistance to thermal shock, ensuring the furnace operates efficiently at high temperatures.
-
Insulation and Heat Preservation
- Insulation is a key feature of induction furnaces, designed to minimize heat loss and improve energy efficiency.
- Materials like vacuum-formed high-purity alumina fiber are commonly used for insulation due to their ability to bear high temperatures and provide excellent heat preservation.
- Proper insulation also protects the furnace's external structure from excessive heat, enhancing safety and longevity.
-
Additional Components
- Compensation Capacitor: Used to improve the power factor and efficiency of the furnace by compensating for reactive power.
- Water-Cooled Cable: Ensures that the induction coil and other components remain at optimal temperatures during operation.
- Reducer: Helps control the flow of molten metal and manage the furnace's operational parameters.
- SiC Heating Rods: In some designs, silicon carbide (SiC) heating rods are vertically installed to provide additional heating support.
-
Durability and Efficiency
- The combination of high-quality materials and advanced design ensures that induction furnaces are both durable and efficient.
- Components like refractory materials and insulation contribute to the furnace's ability to operate at high temperatures for extended periods without significant wear.
- Efficient heat transfer and minimal energy loss make induction furnaces a preferred choice for metal melting applications.
By understanding these key components and their roles, one can appreciate the engineering and material science behind induction furnaces, which make them reliable and effective tools for industrial metal melting processes.
Summary Table:
Component | Role |
---|---|
Power Supply | Provides electrical energy and generates a stable magnetic field. |
Induction Coil | Creates a magnetic field to induce eddy currents in the metal charge. |
Crucible | Holds the metal charge and withstands extreme temperatures. |
Refractory Materials | Ensures durability and resistance to thermal shock. |
Insulation | Minimizes heat loss and improves energy efficiency. |
Additional Components | Includes capacitors, water-cooled cables, and reducers for enhanced performance. |
Ready to optimize your metal melting process? Contact our experts today to learn more about induction furnaces!