Metal sintering is a versatile and efficient fabrication process that involves fusing metal powders into solid objects using heat and pressure. This process is widely used in industries such as automotive, aerospace, medical, and electronics due to its ability to produce complex shapes, high dimensional precision, and cost-effectiveness. Metal sintering techniques include conventional sintering, high-temperature sintering, direct metal laser sintering (DMLS), and liquid phase sintering (LPS), each suited for specific applications. The process is divided into three main steps: blending, compaction, and sintering, and it offers numerous advantages, including self-lubricating properties, vibration damping, and environmental benefits. Metal sintering is also used to create unique materials with uniform properties and is considered a green technology due to its minimal emissions.
Key Points Explained:
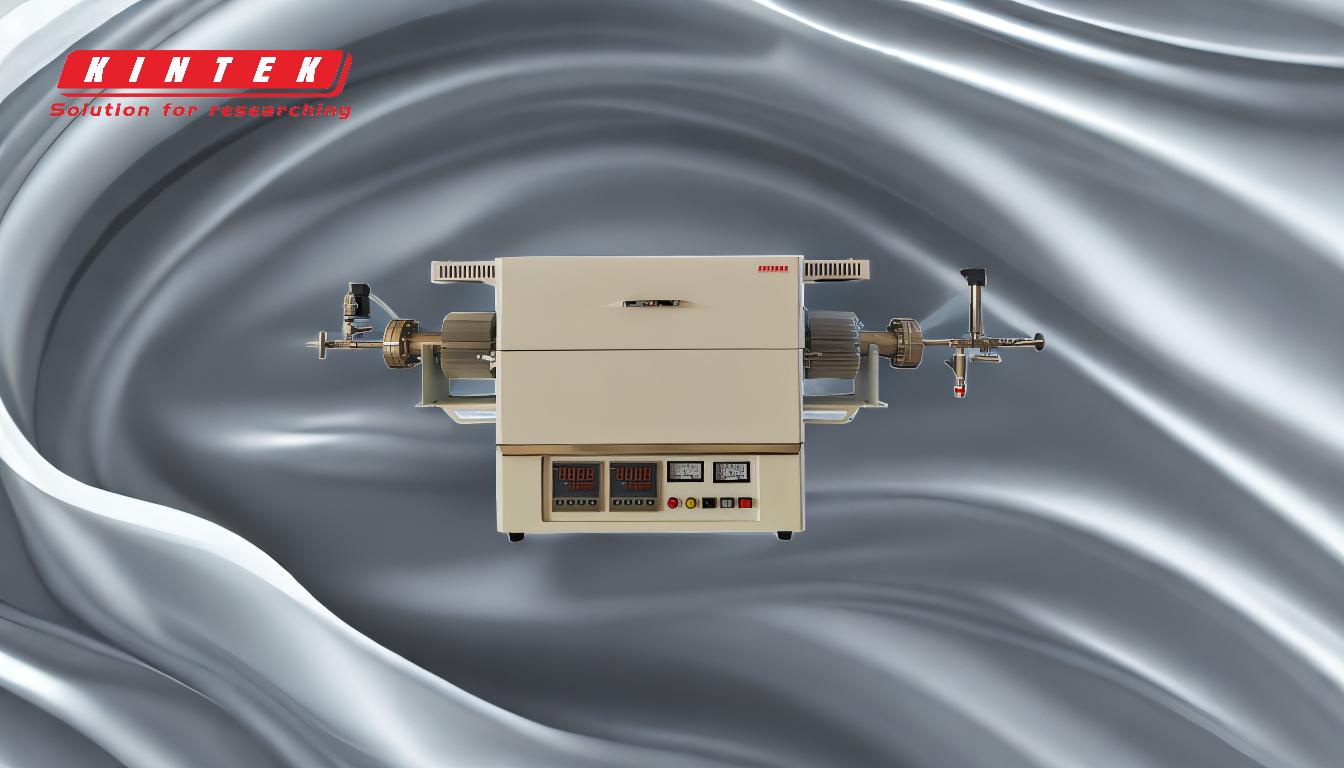
-
Definition and Overview of Metal Sintering:
- Metal sintering is a fabrication process that uses metal powders, heat, and pressure to create solid objects. It involves atomic diffusion and bonding between particles, resulting in a near-net shape that requires minimal finishing.
- The process is also known as powder metallurgy and is divided into three main steps: blending, compaction, and sintering.
-
Types of Metal Sintering Processes:
- Conventional Sintering: Involves heating the powder compact without external pressure. It is widely used for its simplicity and cost-effectiveness.
- High-Temperature Sintering: Reduces surface oxidation and improves mechanical properties, making it suitable for high-performance applications.
- Direct Metal Laser Sintering (DMLS): An advanced 3D printing technique used to produce complex metal components with high precision.
- Liquid Phase Sintering (LPS): Uses a liquid phase to accelerate densification and bonding, resulting in low porosity and strong bonds.
-
Advantages of Metal Sintering:
- Complex Shapes: Enables the production of intricate and complex shapes that are difficult or impossible to achieve with other methods.
- Dimensional Precision: Ensures high accuracy and consistency in the final product.
- Cost-Effectiveness: Reduces material waste and energy consumption compared to traditional melting processes.
- Self-Lubricating Properties: The dense bond between particles provides self-lubricating characteristics, reducing wear and tear.
- Isotropic Materials: Produces materials with uniform properties in all directions, enhancing performance.
- Environmental Benefits: Considered a green technology due to minimal harmful emissions and energy efficiency.
- Vibration Damping: The dense bond between particles also provides vibration damping properties, useful in applications requiring noise reduction.
-
Applications of Metal Sintering:
- Electrical and Electronics: Used to produce electrical components, semiconductors, and optical fibers.
- 3D Printing: Enables the creation of custom metal forms for additive manufacturing.
- Structural Components: Manufactures structural steel parts, porous metals for filtering, and tungsten wiring.
- Bearings and Magnetic Materials: Produces self-lubricating bearings and magnetic materials.
- Medical and Dental Products: Used in the production of dental implants, medical devices, and cutting tools.
-
Additional Sintering Techniques:
- Solid-State Sintering: Powdered material is heated just below its melting point to bond particles by atomic diffusion.
- Reactive Sintering: Involves a chemical reaction of powder particles during heating, creating new compounds.
- Microwave Sintering: Uses microwaves for faster integration, particularly in ceramics.
- Spark Plasma Sintering: Employs electric current and physical compression for rapid densification.
- Hot Isostatic Pressing (HIP): Applies high pressure and temperature to form and fuse powder particles, resulting in high-density materials.
-
Process Control and Efficiency:
- Metal sintering offers better control over the fabrication process, leading to consistent results and fewer imperfections.
- It is energy-efficient and capable of working with high-melting-point materials without the need for melting, reducing energy consumption and costs.
Metal sintering is a critical process in modern manufacturing, offering a blend of precision, efficiency, and versatility. Its ability to produce high-quality, complex components with minimal environmental impact makes it a preferred choice across various industries.
Summary Table:
Aspect | Details |
---|---|
Process Overview | Fuses metal powders using heat and pressure to create solid objects. |
Key Steps | Blending, compaction, and sintering. |
Types of Sintering | Conventional, high-temperature, DMLS, liquid phase sintering. |
Advantages | Complex shapes, dimensional precision, cost-effectiveness, green technology. |
Applications | Automotive, aerospace, medical, electronics, 3D printing. |
Additional Techniques | Solid-state, reactive, microwave, spark plasma, and hot isostatic pressing. |
Learn how metal sintering can revolutionize your manufacturing process—contact us today!