Mill balls, also known as grinding media, are essential components in ball mills used for grinding and mixing materials. They are made from a variety of materials, each chosen for specific properties that suit different grinding applications. Common materials include steel, stainless steel, ceramic, tungsten carbide, zirconia, agate, alumina, silicon nitride, brass, bronze, flint, and non-sparking lead. The choice of material depends on factors such as the hardness of the material being ground, the required fineness of the grind, and the need for contamination-free grinding. Each material offers unique advantages, such as durability, resistance to wear, and chemical inertness, making them suitable for various industrial and laboratory applications.
Key Points Explained:
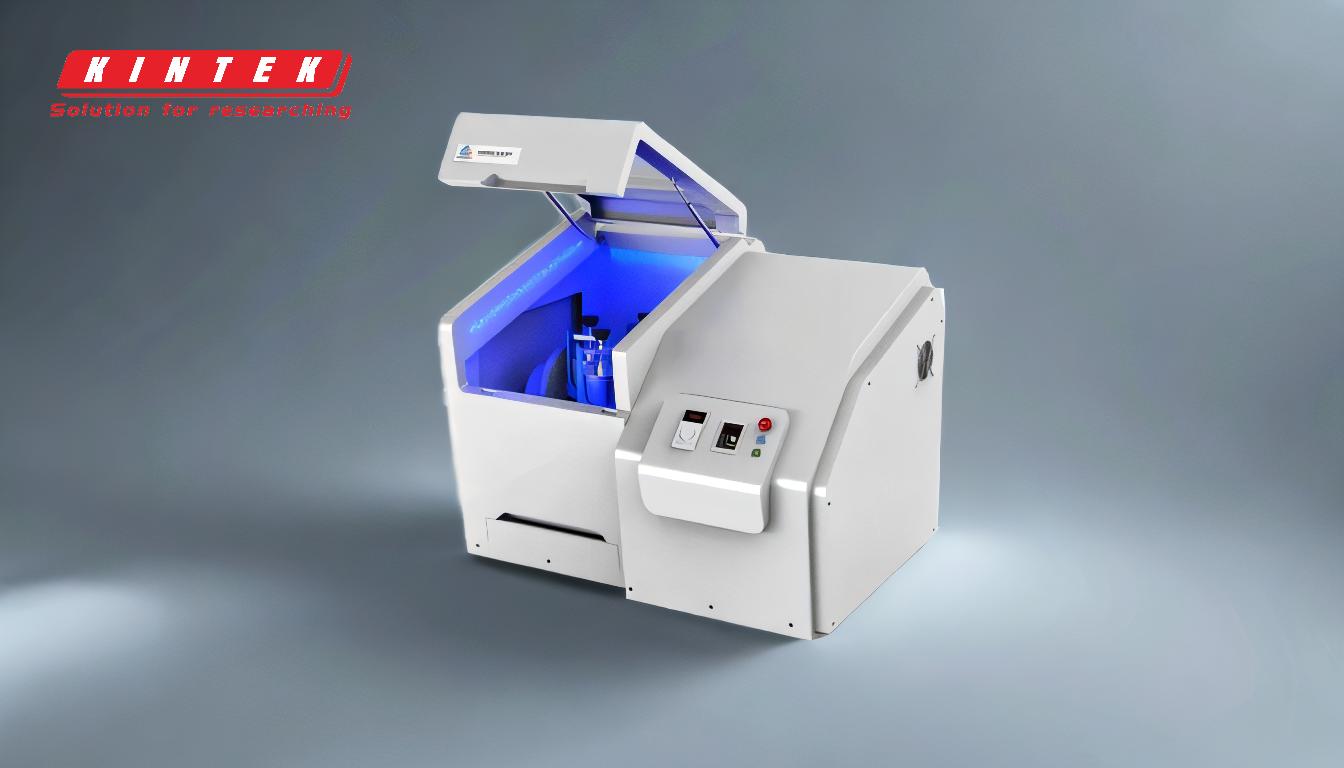
-
Common Materials Used for Mill Balls:
- Steel and Stainless Steel: These are widely used due to their high density and durability. Steel balls are suitable for grinding hard materials like iron ore, while stainless steel is preferred for applications requiring corrosion resistance.
- Ceramic: Ceramic balls, such as those made from alumina or zirconia, are ideal for grinding materials where contamination from metal is a concern. They are chemically inert and provide a contamination-free environment.
- Tungsten Carbide: Known for its extreme hardness and wear resistance, tungsten carbide is used in high-precision grinding applications.
- Agate: Agate balls are used in laboratory settings for grinding small quantities of material without introducing impurities.
- Silicon Nitride: This material offers high strength and thermal shock resistance, making it suitable for high-temperature grinding applications.
- Brass and Bronze: These materials are less common but are used in specific applications where non-sparking properties are required.
- Flint: Flint pebbles are a traditional grinding medium, often used in historical or low-impact grinding processes.
- Non-Sparking Lead: Used in environments where sparking could be hazardous, such as in the presence of flammable materials.
-
Properties and Advantages of Each Material:
- Density and Hardness: Materials like steel and tungsten carbide are chosen for their high density and hardness, which make them effective for grinding tough materials.
- Chemical Inertness: Ceramic and agate balls are chemically inert, making them suitable for grinding materials that are sensitive to contamination.
- Wear Resistance: Tungsten carbide and silicon nitride offer excellent wear resistance, extending the lifespan of the grinding media.
- Corrosion Resistance: Stainless steel and ceramic balls are resistant to corrosion, making them ideal for use in wet or chemically aggressive environments.
- Non-Sparking Properties: Brass, bronze, and non-sparking lead are used in environments where sparking could pose a safety risk.
-
Applications of Different Mill Balls:
- Industrial Grinding: Steel and stainless steel balls are commonly used in industrial ball mills for grinding materials like iron ore, cement, and ceramics.
- Laboratory Grinding: Ceramic, agate, and silicon nitride balls are often used in laboratory ball mills for grinding small quantities of material without contamination.
- Specialized Applications: Tungsten carbide balls are used in high-precision grinding applications, while non-sparking lead balls are used in hazardous environments.
-
Considerations for Selecting Mill Balls:
- Material to be Ground: The hardness and chemical properties of the material being ground will influence the choice of grinding media.
- Required Fineness: The desired fineness of the grind will determine the size and density of the balls needed.
- Contamination Concerns: For applications where contamination must be minimized, ceramic or agate balls are preferred.
- Environmental Conditions: The presence of moisture, chemicals, or flammable materials will influence the choice of material for the grinding media.
By understanding the properties and advantages of different materials used for mill balls, purchasers can make informed decisions that optimize the efficiency and effectiveness of their grinding processes.
Summary Table:
Material | Properties | Applications |
---|---|---|
Steel/Stainless Steel | High density, durability, corrosion resistance | Industrial grinding (e.g., iron ore, cement) |
Ceramic | Chemically inert, contamination-free | Laboratory grinding, sensitive materials |
Tungsten Carbide | Extreme hardness, wear resistance | High-precision grinding |
Agate | Non-contaminating, ideal for small quantities | Laboratory settings |
Silicon Nitride | High strength, thermal shock resistance | High-temperature grinding |
Brass/Bronze | Non-sparking properties | Hazardous environments |
Flint | Traditional, low-impact grinding | Historical or low-impact processes |
Non-Sparking Lead | Safe for flammable environments | Hazardous or explosive environments |
Need help selecting the right mill balls for your application? Contact our experts today for personalized advice!