Plasma deposition processes, particularly those involving chemical vapor deposition (CVD), are advanced techniques used to create thin films and coatings on substrates. These processes leverage plasma—a highly energized state of matter—to enhance the deposition of materials. Plasma-assisted CVD (PACVD) or plasma-enhanced CVD (PECVD) involves the use of plasma to activate chemical reactions, enabling deposition at lower temperatures compared to traditional CVD. This method is widely used in industries such as semiconductor manufacturing, optics, and protective coatings. The process typically involves the generation of reactive species in a plasma environment, which then interact with the substrate to form thin films. Below, we explore the key aspects of plasma deposition processes, focusing on their mechanisms, advantages, and applications.
Key Points Explained:
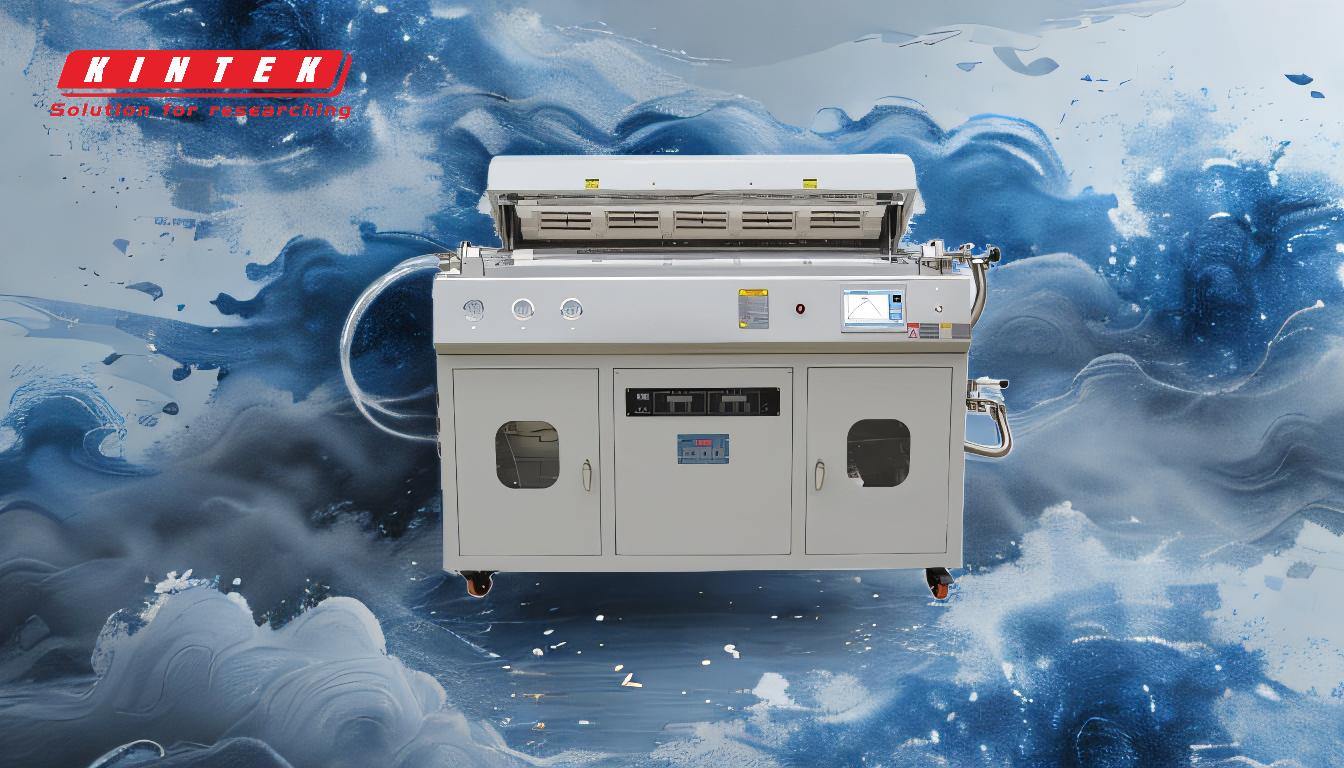
-
Definition and Mechanism of Plasma Deposition:
- Plasma deposition processes, such as chemical vapor deposition, involve the use of plasma to activate chemical reactions that deposit thin films on substrates.
- In these processes, a gas or vapor is ionized to create plasma, which contains highly reactive species like ions, electrons, and radicals. These species interact with the substrate, leading to the formation of a thin film.
-
Steps Involved in Plasma-Assisted CVD:
- Transport of Reacting Species: Gaseous reactants are introduced into the reaction chamber and transported to the substrate surface.
- Plasma Activation: The gas is ionized using an external energy source (e.g., radiofrequency or microwave), creating a plasma state that generates reactive species.
- Surface Reactions: The reactive species adsorb onto the substrate surface, where they undergo chemical reactions to form the desired material.
- Film Growth and Nucleation: The deposited material grows into a thin film, with nucleation occurring at specific sites on the substrate.
- Desorption of Byproducts: Gaseous byproducts are desorbed from the surface and removed from the reaction chamber.
-
Advantages of Plasma Deposition:
- Lower Temperature Operation: Plasma-assisted CVD allows deposition at lower temperatures compared to traditional CVD, making it suitable for temperature-sensitive substrates.
- Enhanced Reaction Rates: The high energy of plasma species accelerates chemical reactions, leading to faster deposition rates.
- Improved Film Quality: Plasma processes often result in films with better adhesion, uniformity, and density.
- Versatility: Plasma deposition can be used with a wide range of materials, including metals, ceramics, and polymers.
-
Applications of Plasma Deposition:
- Semiconductor Manufacturing: Plasma deposition is used to create thin films for integrated circuits, transistors, and other electronic components.
- Optical Coatings: It is employed to produce anti-reflective, protective, and functional coatings for lenses, mirrors, and displays.
- Protective Coatings: Plasma-deposited films are used to enhance the wear resistance, corrosion resistance, and thermal stability of materials.
- Biomedical Applications: Thin films deposited via plasma processes are used in medical devices, implants, and sensors.
-
Comparison with Traditional CVD:
- Traditional CVD relies solely on thermal energy to drive chemical reactions, often requiring high temperatures. In contrast, plasma-assisted CVD uses plasma to provide additional energy, enabling deposition at lower temperatures and with greater control over film properties.
- Plasma deposition is particularly advantageous for substrates that cannot withstand high temperatures or for materials that require precise control over film composition and structure.
-
Challenges and Considerations:
- Complexity of Plasma Systems: Plasma deposition systems can be more complex and expensive to operate compared to traditional CVD.
- Uniformity and Scalability: Achieving uniform deposition over large areas or complex geometries can be challenging.
- Material Compatibility: Not all materials are suitable for plasma deposition, and the process may require optimization for specific applications.
In summary, plasma deposition processes, particularly plasma-assisted CVD, offer a powerful and versatile method for creating high-quality thin films and coatings. By leveraging the unique properties of plasma, these processes enable deposition at lower temperatures, with enhanced reaction rates and improved film properties. While there are challenges associated with plasma deposition, its advantages make it a valuable tool in industries ranging from electronics to biomedical engineering.
Summary Table:
Aspect | Details |
---|---|
Definition | Plasma deposition uses plasma to deposit thin films via chemical reactions. |
Key Steps | Transport, plasma activation, surface reactions, film growth, desorption. |
Advantages | Lower temperatures, faster deposition, improved film quality, versatility. |
Applications | Semiconductors, optical coatings, protective coatings, biomedical devices. |
Challenges | System complexity, uniformity, scalability, material compatibility. |
Unlock the potential of plasma deposition for your projects—contact us today for expert guidance!