PVD (Physical Vapor Deposition) coatings are versatile and widely used across various industries due to their ability to enhance the durability, performance, and functionality of materials. These coatings are applied to improve hardness, wear resistance, corrosion resistance, electrical conductivity, and optical performance, among other properties. They are a greener alternative to traditional plating methods like chrome plating, avoiding toxic byproducts. PVD coatings are used in industries such as aerospace, automotive, medical, optics, electronics, and firearms, extending the lifespan of products like surgical tools, car parts, cutting tools, and more. Their adaptability to both organic and inorganic materials makes them suitable for diverse applications, from decorative finishes to high-performance industrial uses.
Key Points Explained:
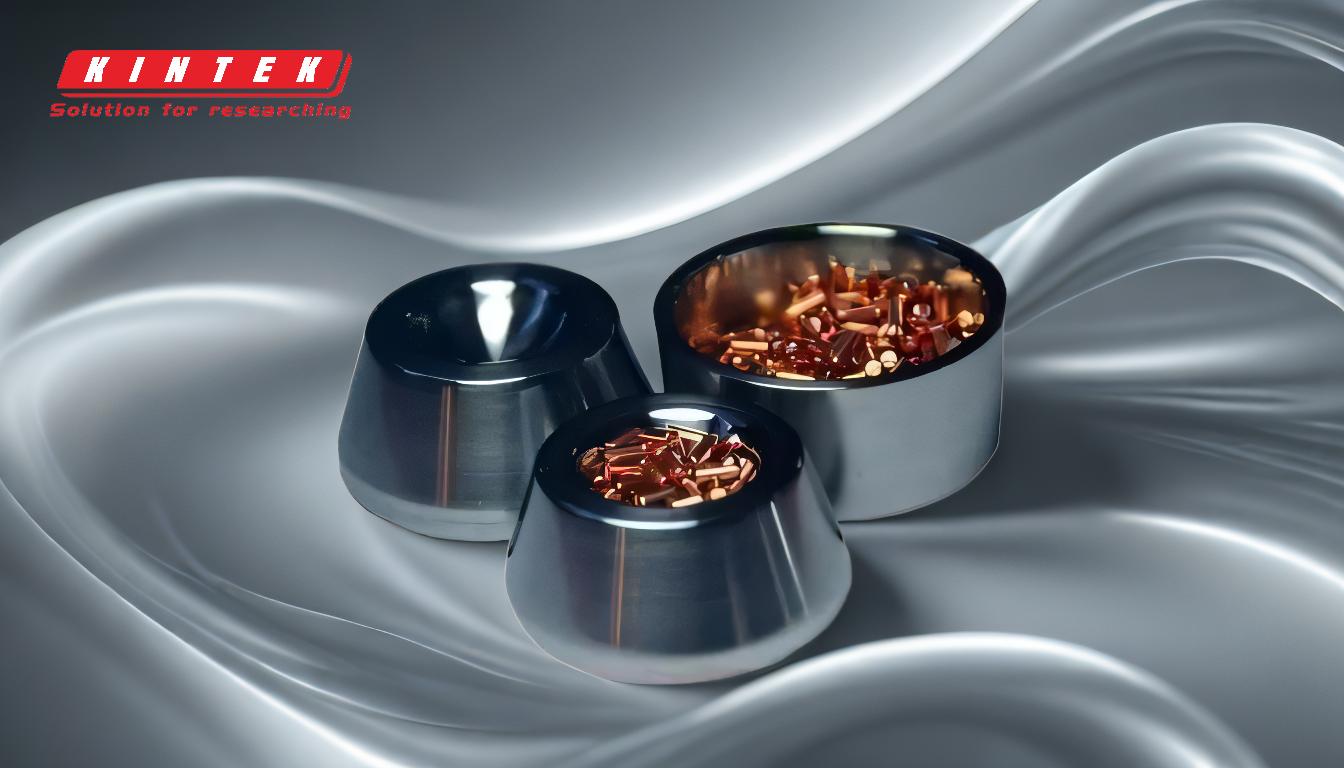
-
Extended Product Lifespan:
- PVD coatings significantly enhance the durability of products, increasing their lifespan by up to ten times in some cases. For example, car parts like wheels and pistons, as well as surgical tools and drill bits, benefit from these coatings, lasting more than 25 years in certain applications.
- Why it matters: This makes PVD coatings cost-effective and sustainable, reducing the need for frequent replacements and maintenance.
-
Improved Material Properties:
- PVD coatings improve hardness, wear resistance, and oxidation resistance. They are used in high-stress environments such as aerospace, automotive, and industrial tools, where materials must withstand extreme conditions.
- Why it matters: Enhanced material properties lead to better performance and reliability in critical applications, such as gas turbine blades and cutting tools.
-
Corrosion and Wear Resistance:
- These coatings are applied to prevent corrosion and wear in various applications, including machine tools, press tools, and gas turbine blades. They are also used in biomedical instruments to ensure longevity and safety.
- Why it matters: Corrosion and wear resistance are essential for maintaining the integrity and functionality of equipment in harsh environments.
-
Electrical and Optical Performance:
- PVD coatings are used to improve electrical conductivity in electronic circuitry (e.g., aluminium tracks and ceramic resistors) and optical performance in applications like anti-reflective coatings for optics and decorative finishes on plastics.
- Why it matters: These properties are critical for industries like electronics and optics, where precision and efficiency are paramount.
-
Versatility Across Industries:
- PVD coatings are applied in a wide range of industries, including aerospace (coating composites), medical (titanium coatings for implants and surgical tools), and firearms (enhancing durability and performance).
- Why it matters: Their adaptability makes PVD coatings a go-to solution for diverse needs, from high-tech aerospace components to everyday consumer products.
-
Eco-Friendly Alternative:
- PVD coatings are a greener alternative to traditional plating methods like chrome plating, as they do not produce toxic substances during the coating process.
- Why it matters: This aligns with global sustainability goals and reduces environmental impact, making PVD coatings a preferred choice for eco-conscious industries.
-
Specialized Applications:
- PVD coatings are used in niche applications such as thin film coatings for photovoltaics, semiconductor devices, and surface-enhanced Raman scattering (SERS) in research. They are also used for decorative purposes, such as coatings on watches and plastics.
- Why it matters: These specialized applications highlight the versatility and precision of PVD coatings in meeting unique industry requirements.
-
High-Performance Industrial Tools:
- Hard ceramic coatings applied via PVD are used in industrial tools to enhance wear resistance and durability, ensuring long-term performance in demanding environments.
- Why it matters: This reduces downtime and maintenance costs, improving overall productivity in industrial settings.
-
Medical and Biomedical Applications:
- PVD coatings are used on medical implants and surgical tools to improve biocompatibility, corrosion resistance, and longevity, ensuring patient safety and device reliability.
- Why it matters: In the medical field, these properties are critical for ensuring the effectiveness and safety of devices and implants.
-
Decorative and Functional Finishes:
- PVD coatings are used for both decorative purposes (e.g., coatings on watches and plastics) and functional finishes (e.g., anti-reflective coatings for optics and window tinting).
- Why it matters: This dual functionality makes PVD coatings valuable in industries where aesthetics and performance are equally important.
In summary, PVD coatings are a transformative technology used across multiple industries to enhance the durability, performance, and functionality of materials. Their ability to improve hardness, wear resistance, corrosion resistance, and optical/electrical properties, combined with their eco-friendly nature, makes them an indispensable solution for modern manufacturing and high-tech applications.
Summary Table:
Key Benefits of PVD Coatings | Applications | Why It Matters |
---|---|---|
Extended product lifespan (up to 10x) | Car parts, surgical tools, drill bits | Cost-effective, sustainable, reduces replacements |
Improved hardness, wear, and oxidation resistance | Aerospace, automotive, industrial tools | Enhances performance in extreme conditions |
Corrosion and wear resistance | Machine tools, biomedical instruments | Ensures longevity and safety in harsh environments |
Enhanced electrical and optical performance | Electronics, optics | Critical for precision and efficiency |
Versatility across industries | Aerospace, medical, firearms | Adaptable for diverse needs |
Eco-friendly alternative to chrome plating | All industries | Reduces environmental impact |
Specialized applications (e.g., photovoltaics, SERS) | Research, decorative finishes | Meets unique industry requirements |
High-performance industrial tools | Industrial settings | Reduces downtime and maintenance costs |
Medical and biomedical applications | Implants, surgical tools | Ensures biocompatibility and patient safety |
Decorative and functional finishes | Watches, plastics, optics | Combines aesthetics and performance |
Ready to enhance your products with PVD coatings? Contact us today to learn more!