Graphite furnace atomic absorption spectroscopy (GFAAS) and flame atomic absorption spectroscopy (FAAS) are two common techniques used for trace metal analysis. GFAAS offers higher sensitivity and lower detection limits compared to FAAS, making it suitable for analyzing very low concentrations of elements. However, it is more complex, slower, and requires more expensive equipment. FAAS, on the other hand, is faster, simpler, and more cost-effective but has higher detection limits and is less sensitive. The choice between the two depends on the specific analytical requirements, such as the concentration range of the analyte, sample throughput, and available resources.
Key Points Explained:
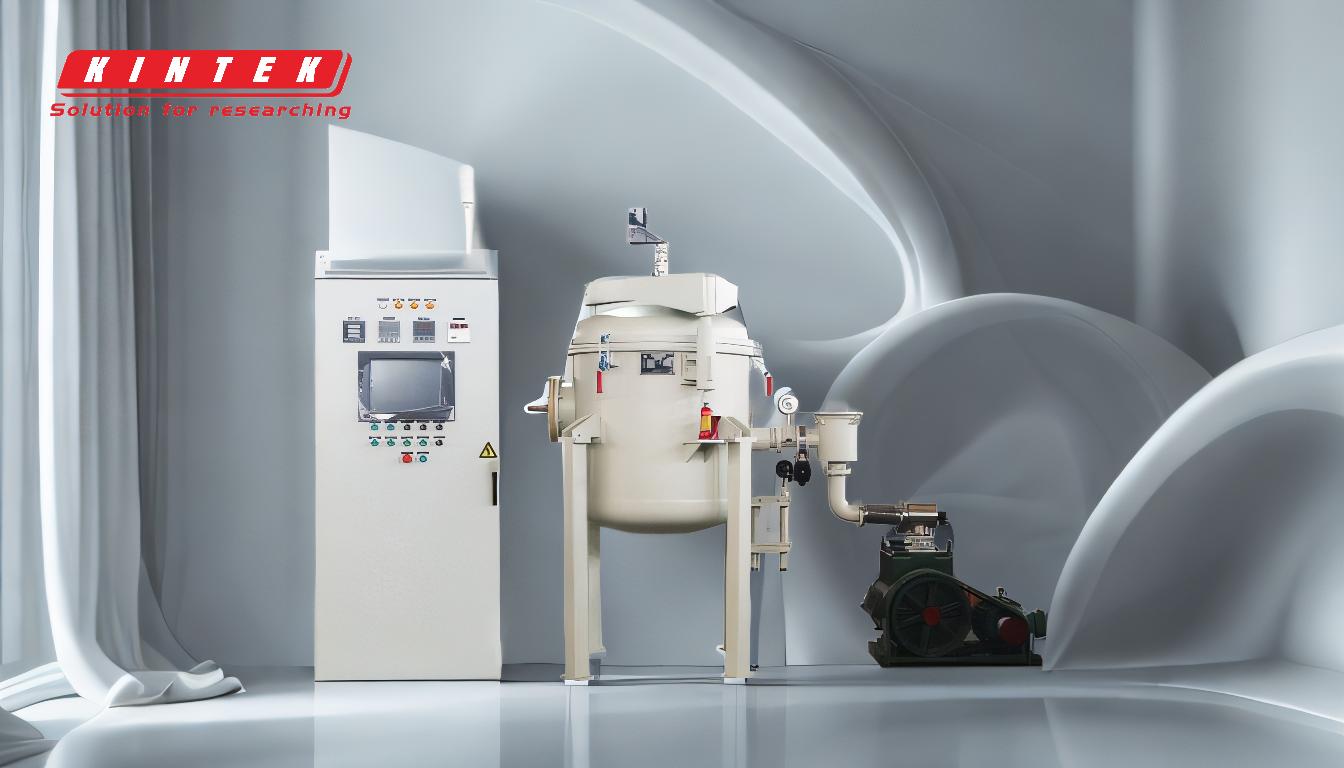
-
Sensitivity and Detection Limits:
-
GFAAS:
- Advantage: GFAAS provides significantly higher sensitivity and lower detection limits, often in the parts-per-billion (ppb) or even parts-per-trillion (ppt) range. This is due to the efficient atomization process in the graphite furnace, where the sample is heated in a controlled environment, leading to better atomization and less interference.
- Disadvantage: The high sensitivity can sometimes lead to over-detection, where trace contaminants might interfere with the analysis.
-
FAAS:
- Advantage: FAAS is less sensitive, which can be advantageous when analyzing samples with higher concentrations of analytes, as it avoids the need for extensive dilution.
- Disadvantage: The detection limits are higher, typically in the parts-per-million (ppm) range, making it unsuitable for ultra-trace analysis.
-
GFAAS:
-
Sample Volume and Throughput:
-
GFAAS:
- Advantage: Requires very small sample volumes (microliters), which is beneficial when sample quantity is limited.
- Disadvantage: The analysis is slower due to the stepwise heating process (drying, ashing, atomization), leading to lower sample throughput.
-
FAAS:
- Advantage: FAAS can handle larger sample volumes and is faster, allowing for higher sample throughput, which is ideal for routine analysis.
- Disadvantage: Larger sample volumes are required, which might be a limitation when sample availability is low.
-
GFAAS:
-
Complexity and Cost:
-
GFAAS:
- Advantage: The ability to analyze very low concentrations makes GFAAS indispensable for certain applications, such as environmental monitoring and clinical analysis.
- Disadvantage: The equipment is more complex, requires skilled operators, and is more expensive to purchase and maintain.
-
FAAS:
- Advantage: FAAS is simpler to operate, requires less training, and is more cost-effective, making it accessible for routine laboratory use.
- Disadvantage: The lower sensitivity and higher detection limits may not meet the requirements for certain trace analysis applications.
-
GFAAS:
-
Interferences and Matrix Effects:
-
GFAAS:
- Advantage: The controlled environment in the graphite furnace reduces chemical and spectral interferences, leading to more accurate results.
- Disadvantage: Matrix effects can still be significant, and background correction techniques (e.g., Zeeman or deuterium lamp) are often required, adding to the complexity.
-
FAAS:
- Advantage: FAAS is less prone to matrix effects in some cases, especially when using flame conditions that minimize interferences.
- Disadvantage: Chemical and spectral interferences are more common in FAAS, requiring the use of modifiers or additional steps to mitigate these effects.
-
GFAAS:
-
Applications and Suitability:
-
GFAAS:
- Advantage: Ideal for applications requiring ultra-trace analysis, such as environmental monitoring, food safety, and clinical diagnostics.
- Disadvantage: Not suitable for high-throughput or routine analysis due to slower processing times.
-
FAAS:
- Advantage: Best suited for routine analysis where higher detection limits are acceptable, such as in industrial quality control or geological surveys.
- Disadvantage: Limited use in applications requiring detection of very low concentrations.
-
GFAAS:
-
Maintenance and Operational Considerations:
-
GFAAS:
- Advantage: The graphite furnace can be cleaned and reused, reducing consumable costs over time.
- Disadvantage: Requires regular maintenance, including replacement of graphite tubes and frequent calibration, which can be labor-intensive and costly.
-
FAAS:
- Advantage: Generally lower maintenance requirements, with fewer consumables and less frequent calibration needed.
- Disadvantage: The flame system requires a continuous supply of gases (e.g., acetylene, air), which can be a logistical concern and adds to operational costs.
-
GFAAS:
In summary, the choice between GFAAS and FAAS depends on the specific needs of the analysis. GFAAS is preferred for ultra-trace analysis where sensitivity is critical, while FAAS is more suitable for routine analysis with higher sample throughput and lower operational complexity. Each method has its own set of advantages and disadvantages, and the decision should be based on factors such as detection limits, sample volume, throughput, cost, and the nature of the sample matrix.
Summary Table:
Feature | GFAAS | FAAS |
---|---|---|
Sensitivity | High (ppb/ppt range) | Lower (ppm range) |
Sample Volume | Small (microliters) | Larger |
Throughput | Slower (stepwise heating process) | Faster (ideal for routine analysis) |
Complexity | High (requires skilled operators) | Low (simpler operation) |
Cost | Higher (expensive equipment and maintenance) | Lower (cost-effective for routine use) |
Applications | Ultra-trace analysis (e.g., environmental, clinical) | Routine analysis (e.g., industrial quality control) |
Maintenance | Regular (graphite tube replacement, calibration) | Lower (fewer consumables, less frequent calibration) |
Need help choosing between GFAAS and FAAS for your analysis? Contact our experts today for personalized guidance!