Sputtering systems are advanced plasma-based deposition tools used to create thin films of materials on substrates. These systems operate by bombarding a target material with high-energy ions in a vacuum environment, causing atoms to be ejected from the target and deposited onto a substrate. This process is highly precise and versatile, making it essential in industries like semiconductors, optics, and solar energy. Sputtering systems are designed to handle various applications, from semiconductor wafer metallization to coating large architectural glass panels, and are capable of depositing materials ranging from metals to alloys in a single run. The technology is valued for its ability to produce high-quality, durable, and uniform thin films at relatively low temperatures, making it suitable for heat-sensitive substrates.
Key Points Explained:
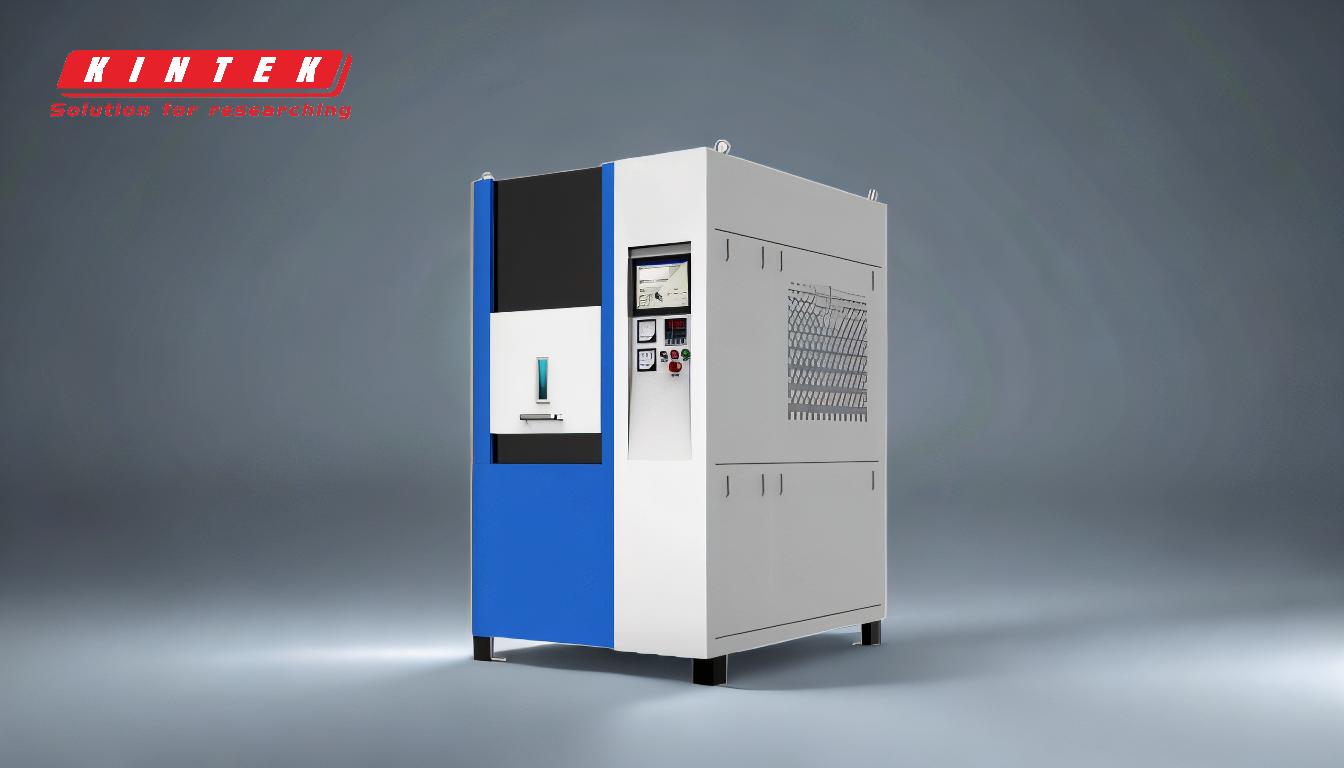
-
What is Sputtering?
- Sputtering is a plasma-based deposition process where high-energy ions bombard a target material, causing atoms to be ejected from its surface. These atoms then travel and deposit onto a substrate, forming a thin film.
- The process occurs in a vacuum chamber to prevent contamination from air or other gases, ensuring high-purity coatings.
-
How Sputtering Systems Work
- A sputtering system consists of a vacuum chamber, a target material, and a substrate. The target is bombarded with ions, typically from a plasma generated by an electric field (DC, RF, or magnetron sputtering).
- The ejected atoms from the target have high kinetic energy and condense onto the substrate, forming a thin film. The substrate is often placed opposite the target to ensure uniform deposition.
-
Applications of Sputtering Systems
- Semiconductor Industry: Used for depositing thin films of metals, alloys, and dielectrics in integrated circuit fabrication.
- Optical Industry: Applied for antireflection coatings, polarization filters, and low-emissivity coatings on glass.
- Architectural Glass: Used to coat large-area surfaces for energy-efficient windows.
- Data Storage: Essential for depositing metal layers in CDs, DVDs, and hard disks.
- Solar Energy: Utilized in manufacturing photovoltaic solar cells and optical waveguides.
- Tooling and Plastics: Coating tool bits with nitrides and metalizing plastics for enhanced durability and functionality.
-
Advantages of Sputtering Systems
- Precision: Capable of depositing thin films with nanometer-scale accuracy.
- Versatility: Can deposit a wide range of materials, including metals, alloys, and compounds, in a single run.
- Low Temperature: Suitable for heat-sensitive substrates like plastics.
- Uniformity: Produces highly uniform and durable coatings.
- Scalability: Can be used for both small-scale research and large-scale industrial applications.
-
Types of Sputtering Systems
- Direct Sputtering Systems: Used for high deposition rates and large substrates, such as in semiconductor wafer metallization and flat panel displays.
- Magnetron Sputtering Systems: Utilize magnetic fields to enhance plasma density, improving deposition rates and efficiency.
- Reactive Sputtering Systems: Introduce reactive gases (e.g., nitrogen or oxygen) to form compound films like nitrides or oxides.
-
Key Components of Sputtering Systems
- Vacuum Chamber: Maintains a controlled environment to prevent contamination.
- Target Material: The source of atoms to be deposited.
- Substrate Holder: Positions the substrate for uniform film deposition.
- Power Supply: Generates the electric field to create plasma.
- Gas Inlet System: Introduces inert or reactive gases into the chamber.
-
Importance in Advanced Manufacturing
- Sputtering systems are critical for developing smaller, lighter, and more durable products. They enable the creation of advanced materials and coatings that enhance performance in various industries, from electronics to renewable energy.
-
Challenges and Considerations
- Cost: High initial investment for equipment and maintenance.
- Complexity: Requires skilled operators and precise control of process parameters.
- Material Limitations: Some materials may not sputter efficiently or may require specialized conditions.
By understanding these key points, equipment and consumable purchasers can make informed decisions about selecting sputtering systems that meet their specific needs, whether for research, development, or large-scale production.
Summary Table:
Key Aspect | Details |
---|---|
Process | Plasma-based deposition in a vacuum environment. |
Applications | Semiconductors, optics, solar energy, architectural glass, data storage. |
Advantages | Precision, versatility, low-temperature operation, uniformity, scalability. |
Types | Direct, magnetron, and reactive sputtering systems. |
Key Components | Vacuum chamber, target material, substrate holder, power supply, gas inlet. |
Challenges | High cost, complexity, and material limitations. |
Ready to enhance your manufacturing process with advanced sputtering systems? Contact us today for expert guidance!