Deposition is a critical process in materials science and engineering, used to create thin films or coatings on substrates. The two primary methods of deposition are Physical Vapour Deposition (PVD) and Chemical Vapour Deposition (CVD). PVD involves physically transferring material from a source to a substrate, typically through processes like sputtering or thermal evaporation. In contrast, CVD relies on chemical reactions to deposit a thin film, often involving gaseous precursors that react on the substrate surface. Both methods have unique advantages and are chosen based on the desired film properties, substrate compatibility, and application requirements.
Key Points Explained:
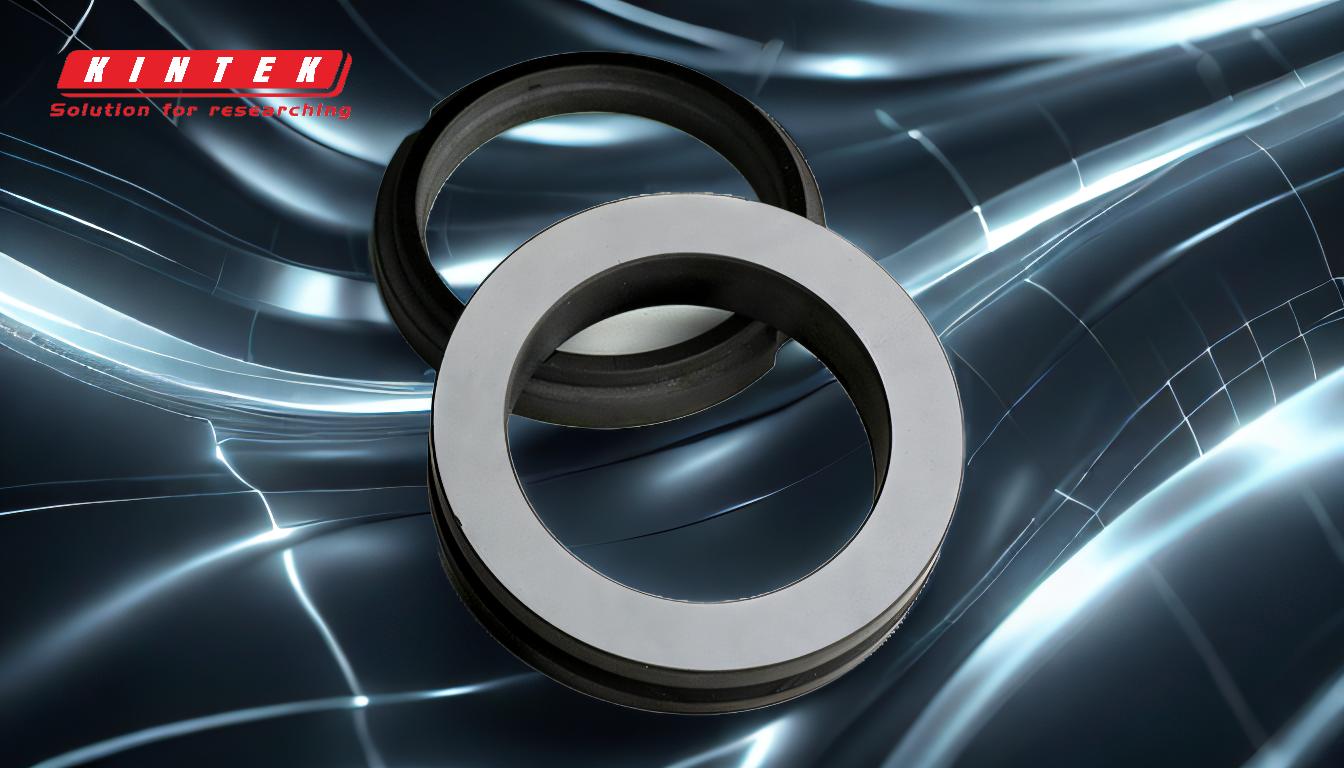
-
Physical Vapour Deposition (PVD):
- Definition: PVD is a process where material is physically transferred from a source to a substrate in a vacuum environment.
-
Techniques:
-
Sputtering: This involves bombarding a target material with high-energy ions, causing atoms to be ejected and deposited onto the substrate. Common sputtering techniques include:
- Direct Current (DC) Sputtering: Used for conductive materials, where a DC voltage is applied to create a plasma.
- Radio Frequency (RF) Sputtering: Suitable for insulating materials, where an RF field is used to generate the plasma.
- Thermal Evaporation: This method uses high temperatures to vaporize the target material, which then condenses onto the substrate. It is often used for materials with low melting points.
-
Sputtering: This involves bombarding a target material with high-energy ions, causing atoms to be ejected and deposited onto the substrate. Common sputtering techniques include:
- Advantages: PVD produces high-purity films with excellent adhesion and can be used for a wide range of materials. It is also environmentally friendly, as it typically does not involve hazardous chemicals.
- Applications: PVD is widely used in the semiconductor industry, for optical coatings, and in the production of wear-resistant coatings.
-
Chemical Vapour Deposition (CVD):
- Definition: CVD is a process where chemical reactions between gaseous precursors result in the deposition of a solid material onto a substrate.
- Process: The substrate is exposed to volatile precursors, which react or decompose on the surface to form the desired film. The process often requires elevated temperatures and controlled pressure.
- Advantages: CVD can produce films with excellent conformality, meaning it can uniformly coat complex geometries. It also allows for the deposition of a wide variety of materials, including metals, semiconductors, and ceramics.
- Applications: CVD is used in the production of microelectronic devices, solar cells, and protective coatings. It is also essential in the fabrication of carbon nanotubes and graphene.
-
Comparison of PVD and CVD:
- Deposition Mechanism: PVD relies on physical processes, while CVD involves chemical reactions.
- Film Properties: PVD films tend to have better adhesion and purity, while CVD films offer superior conformality and can be deposited at lower temperatures.
- Material Compatibility: PVD is suitable for a wide range of materials, including metals and alloys, while CVD is preferred for materials that require precise stoichiometry, such as semiconductors.
- Environmental Impact: PVD is generally more environmentally friendly, as it does not involve toxic precursors, whereas CVD often requires hazardous chemicals.
-
Other Deposition Techniques:
- Atomic Layer Deposition (ALD): A variant of CVD that deposits films one atomic layer at a time, offering exceptional control over film thickness and composition. It is ideal for applications requiring ultra-thin, uniform coatings.
- Spray Pyrolysis: A technique where a solution containing the desired material is sprayed onto a heated substrate, causing the solvent to evaporate and the material to decompose, forming a thin film. This method is cost-effective and suitable for large-area coatings.
In summary, the choice between PVD and CVD depends on the specific requirements of the application, including the desired film properties, substrate material, and environmental considerations. Both methods are indispensable in modern manufacturing and materials science, enabling the creation of advanced materials and devices.
Summary Table:
Method | Mechanism | Key Techniques | Advantages | Applications |
---|---|---|---|---|
PVD | Physical transfer | Sputtering, Thermal Evaporation | High-purity films, excellent adhesion, environmentally friendly | Semiconductors, optical coatings, wear-resistant coatings |
CVD | Chemical reactions | Gaseous precursors, elevated temps | Superior conformality, wide material compatibility, precise stoichiometry | Microelectronics, solar cells, carbon nanotubes, graphene |
Discover the best deposition method for your project—contact our experts today!