E-beam evaporation is a versatile and efficient thin-film deposition technique widely used in various industries. It offers several advantages, such as the ability to handle high-melting-point materials, higher deposition rates, better material utilization efficiency, and improved film purity. Additionally, it provides excellent step coverage and is compatible with ion-assisted deposition for enhanced film properties. However, it also has some challenges, such as the risk of particle fracturing or contamination during the process. Overall, e-beam evaporation is a highly controllable and repeatable method, making it suitable for critical applications like optical coatings and laser optics.
Key Points Explained:
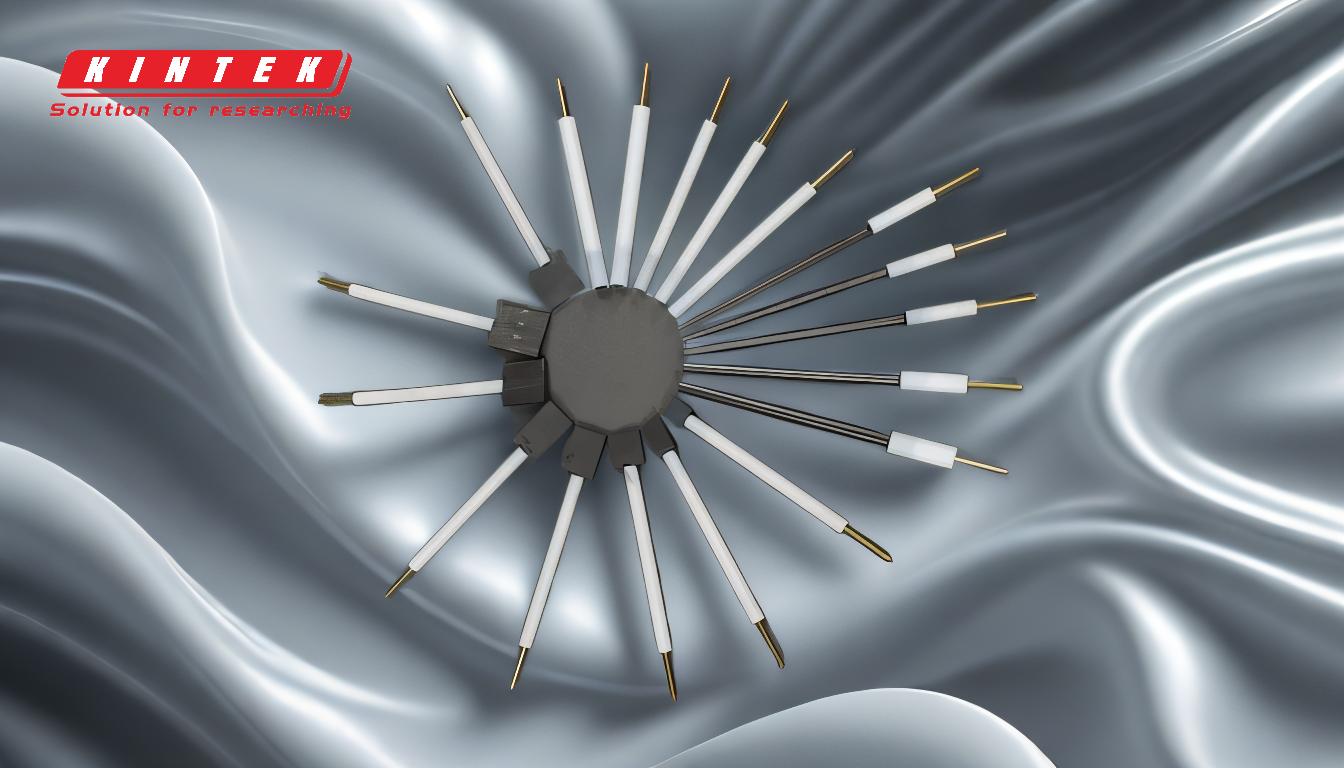
-
Versatility with High-Melting-Point Materials:
- E-beam evaporation is capable of depositing materials with very high melting points that cannot be processed using traditional thermal evaporation methods. This makes it suitable for a wide range of materials, including metals, ceramics, and refractory compounds.
-
Higher Deposition Rates and Material Utilization Efficiency:
- The direct heat transfer between the electron beam and the target material allows for very high deposition rates compared to other methods like sputtering. Additionally, the material utilization efficiency is higher, reducing waste and cost.
-
Improved Film Purity and Reduced Contamination:
- Since the material is vaporized by a high-energy electron beam without melting it in a crucible, the risk of contamination from the crucible is minimized. This results in films with higher purity, which is critical for applications requiring precise material properties.
-
Better Step Coverage:
- E-beam evaporation provides better step coverage than sputtering or chemical vapor deposition (CVD). This is particularly important for coating complex geometries or uneven surfaces, ensuring uniform film thickness.
-
Compatibility with Ion-Assisted Deposition (IAD):
- The process can be combined with an ion assist source for pre-cleaning or ion-assisted deposition, which enhances thin film performance characteristics such as adhesion, density, and stress.
-
Controllability and Repeatability:
- The process is highly controllable and repeatable, with real-time optical monitoring and control. This makes it ideal for critical applications like optical coatings, where precision and consistency are paramount.
-
Challenges and Limitations:
- Despite its advantages, e-beam evaporation has some challenges. These include the risk of particle fracturing, explosions, or detrimental reactions during the process. Additionally, reductions or decompositions of materials can occur, which may affect film quality.
-
Applications in Optical Coatings and Laser Optics:
- E-beam evaporation is widely used in industries requiring high-density thin films and optimal substrate adhesion. It is particularly valuable for controlling the reflection of specific wavelength bands, making it suitable for producing laser optics and architectural glass products.
In summary, e-beam evaporation is a powerful and versatile thin-film deposition technique with significant advantages in terms of material versatility, deposition rates, and film quality. However, it requires careful handling to mitigate potential challenges and ensure optimal results.
Summary Table:
Advantages | Disadvantages |
---|---|
Handles high-melting-point materials | Risk of particle fracturing or contamination |
Higher deposition rates | Potential for explosions or detrimental reactions |
Improved film purity | Reductions or decompositions of materials |
Better step coverage | |
Compatible with ion-assisted deposition (IAD) | |
Highly controllable and repeatable | |
Suitable for optical coatings and laser optics |
Discover how e-beam evaporation can elevate your thin-film processes—contact our experts today!