Electron beam evaporation is a highly advanced thin film deposition technique that offers unique advantages, such as the ability to evaporate high-temperature materials and achieve high deposition rates with precision. However, it also comes with notable disadvantages, including high equipment costs, complex electronics, and safety concerns. This method is particularly suitable for applications requiring high purity and precision, such as ophthalmic coatings and solar panels, but may not be cost-effective for smaller-scale or laboratory settings. Below, the key advantages and disadvantages are explored in detail.
Key Points Explained:
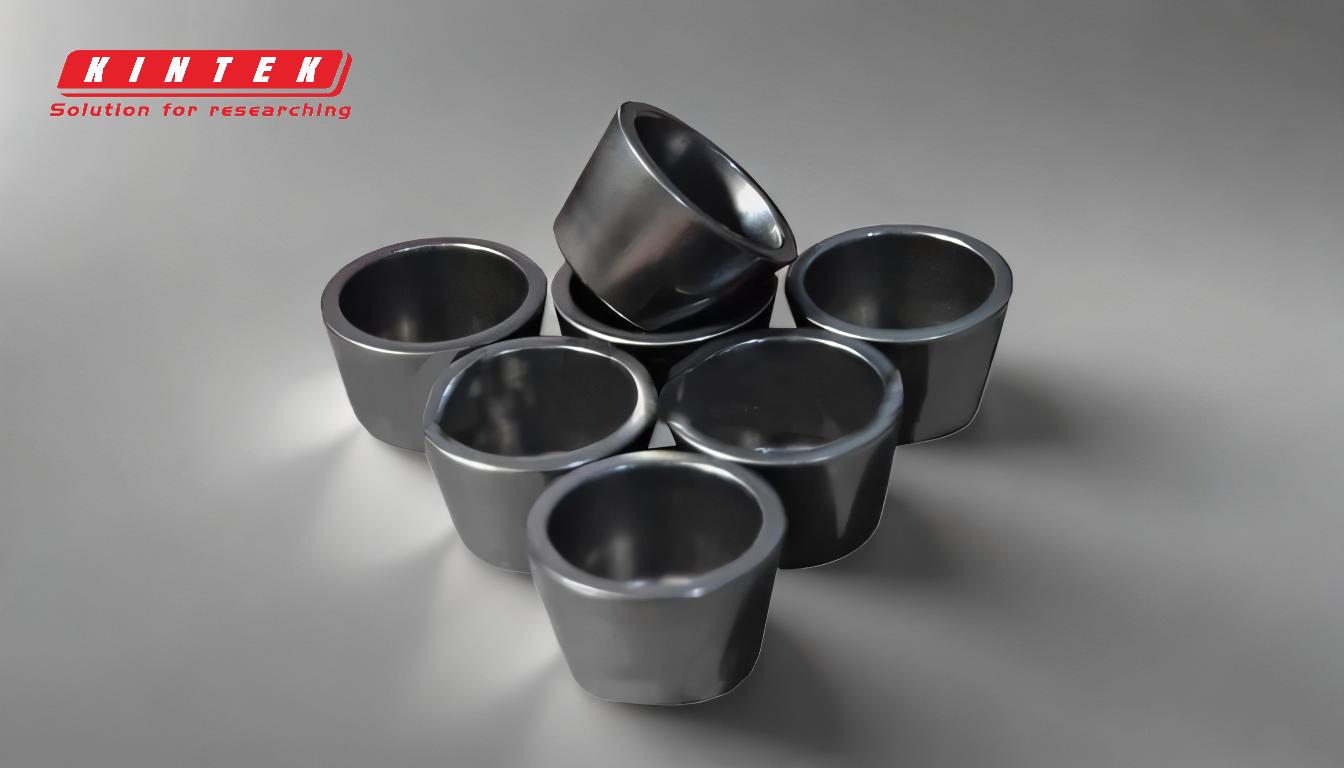
Advantages of Electron Beam Evaporation:
-
Ability to Evaporate High-Temperature Materials:
- Electron beam evaporation excels at heating materials locally, making it possible to evaporate refractory metals and other high-temperature materials that are difficult to process using other methods.
- This capability is crucial for applications requiring materials with high melting points, such as tungsten or tantalum.
-
High Deposition Rates:
- The process can achieve very high deposition rates, making it efficient for large-scale production or applications where speed is critical.
- This is particularly beneficial in industries like solar panel manufacturing, where throughput is a key factor.
-
Precision and Purity:
- Electron beam evaporation allows for the transfer of pure and precise metal coatings at the atomic and molecular level.
- This makes it ideal for applications demanding high precision, such as optical coatings and semiconductor manufacturing.
-
Versatility with Vacuum-Compatible Materials:
- The technique can evaporate almost any material that is vacuum-compatible, provided it does not decompose under high temperatures.
- This versatility makes it suitable for a wide range of materials, including metals, ceramics, and some polymers.
-
Localized Heating:
- Unlike resistive evaporation, which heats the entire material, electron beam evaporation focuses energy on a small area, reducing contamination and improving efficiency.
Disadvantages of Electron Beam Evaporation:
-
High Equipment Costs:
- The equipment required for electron beam evaporation is significantly more expensive than that for filament or boat evaporation.
- This makes it a less attractive option for smaller-scale operations or laboratories with limited budgets.
-
Complex and Costly Drive Electronics:
- The technology relies on complex drive electronics, which add to the overall cost and maintenance requirements.
- The need for precise control over the electron beam further increases the complexity of the system.
-
High Voltage Safety Hazards:
- The process involves high voltages, posing significant safety risks to operators.
- Proper safety protocols and training are essential to mitigate these risks, adding to operational costs.
-
Limited Scalability:
- Electron beam evaporation is not as easily scalable as resistive evaporation, making it less suitable for applications requiring large-area coatings or high-volume production.
- This limitation restricts its use to specific high-precision or niche applications.
-
Material Decomposition Risk:
- While the method can handle a wide range of materials, some compounds may decompose under the intense localized heating, limiting its applicability for certain organic or sensitive materials.
Applications and Suitability:
-
High-Precision Industries:
- Electron beam evaporation is widely used in industries requiring high precision and purity, such as ophthalmic coatings, semiconductor manufacturing, and solar panel production.
- Its ability to handle high-temperature materials and deliver precise coatings makes it indispensable in these fields.
-
Niche and Specialized Applications:
- The technique is often chosen for specialized applications where other methods fall short, such as depositing refractory metals or creating ultra-thin films.
-
Cost Considerations:
- While the technology is powerful, its high cost and complexity make it less practical for general laboratory use or small-scale projects.
- For such applications, simpler and more cost-effective methods like resistive evaporation or sputtering may be preferred.
Conclusion:
Electron beam evaporation is a powerful and versatile thin film deposition technique with distinct advantages, particularly in high-precision and high-temperature applications. However, its high cost, complexity, and safety concerns limit its suitability for smaller-scale or less specialized uses. When selecting a deposition method, it is essential to weigh these factors against the specific requirements of the application to determine the most appropriate technology.
Summary Table:
Aspect | Advantages | Disadvantages |
---|---|---|
High-Temperature Materials | Can evaporate refractory metals like tungsten and tantalum. | High equipment costs. |
Deposition Rates | Achieves high deposition rates, ideal for large-scale production. | Complex and costly drive electronics. |
Precision and Purity | Delivers atomic-level precision, suitable for optical coatings and semiconductors. | High voltage safety hazards. |
Versatility | Works with vacuum-compatible materials, including metals and ceramics. | Limited scalability for large-area coatings. |
Localized Heating | Reduces contamination by focusing energy on a small area. | Risk of material decomposition for sensitive compounds. |
Need help choosing the right thin film deposition method? Contact our experts today for tailored solutions!