Electron Beam Machining (EBM) is a highly specialized thermal machining process that uses a focused beam of high-velocity electrons to vaporize material, enabling precise cutting, boring, or engraving of various metals. It offers advantages such as high precision, better surface finish, and the ability to work with a wide range of materials. However, it also comes with significant drawbacks, including high equipment and operational costs, the need for a vacuum environment, safety concerns, and limitations in surface finish and depth of cut. These factors make EBM suitable primarily for high-value applications where precision and material compatibility are critical.
Key Points Explained:
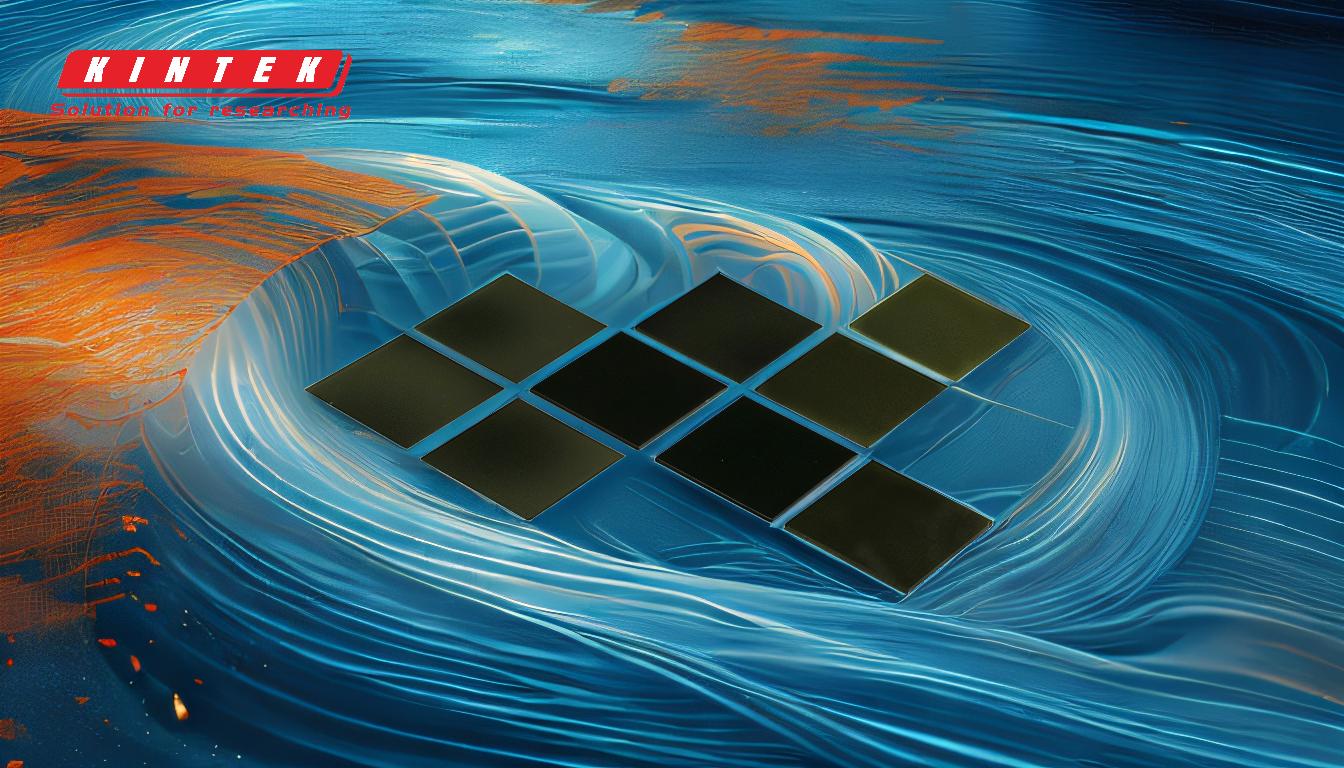
-
Advantages of Electron Beam Machining (EBM):
- High Precision and Accuracy: EBM can achieve extremely fine cuts and narrow kerf widths, making it ideal for applications requiring high precision.
- Superior Surface Finish: The process provides a better surface finish compared to other thermal machining methods, reducing the need for additional finishing processes.
- Material Versatility: EBM can accurately cut or bore a wide variety of metals, including those that are difficult to machine using conventional methods.
- Localized Heating: The electron beam can be precisely controlled to heat and vaporize material locally, minimizing thermal damage to surrounding areas.
- High Deposition Rates: In applications like electron beam evaporation, EBM can achieve very high deposition rates, making it efficient for certain industrial processes.
-
Disadvantages of Electron Beam Machining (EBM):
- High Equipment and Operational Costs: EBM requires expensive equipment and complex drive electronics, making it a costly option compared to other machining methods.
- Vacuum Requirements: The process must be conducted in a vacuum environment, adding to the complexity and cost of the setup.
- Safety Concerns: The use of high-voltage electron beams poses significant safety hazards, requiring stringent safety measures and protocols.
- Limited Surface Finish: While EBM provides a good surface finish, it may not be suitable for applications requiring ultra-smooth finishes.
- Limited Depth of Cut: EBM is less effective for deep cuts or thick materials, limiting its applicability in certain scenarios.
- Energy Consumption: The process consumes a significant amount of energy, contributing to higher operational costs.
- Scalability Issues: EBM is not easily scalable, making it less suitable for large-scale production or laboratory settings where cost-effectiveness is a priority.
-
Applications and Limitations:
- High-Value Products: Due to its high cost and precision, EBM is typically used for high-value products where the benefits outweigh the expenses.
- Specific Process Applications: EBM is popular in niche applications such as ophthalmic coatings and other specialized industries where its unique capabilities are required.
- Unsuitability for Certain Materials: Some materials may not be compatible with EBM, either due to decomposition under high heat or other material-specific limitations.
-
Comparison with Other Machining Methods:
- Versus Thermal Cutting Processes: EBM offers better surface finish and narrower kerf widths compared to other thermal cutting methods, but at a higher cost.
- Versus Filament or Boat Evaporation: EBM provides higher deposition rates and the ability to evaporate high-temperature materials, but it is significantly more expensive and complex to operate.
In summary, Electron Beam Machining is a powerful and precise technology with distinct advantages in terms of accuracy, surface finish, and material versatility. However, its high costs, safety concerns, and operational limitations make it suitable primarily for specialized, high-value applications. Understanding these trade-offs is essential for determining whether EBM is the right choice for a given machining need.
Summary Table:
Aspect | Details |
---|---|
Advantages | High precision, superior surface finish, material versatility, localized heating, high deposition rates |
Disadvantages | High costs, vacuum requirements, safety concerns, limited depth of cut, energy consumption, scalability issues |
Applications | High-value products, ophthalmic coatings, specialized industrial processes |
Limitations | Unsuitable for certain materials, not ideal for large-scale production |
Interested in learning more about Electron Beam Machining? Contact our experts today for tailored solutions!