The Physical Vapor Deposition (PVD) process is a widely used technique in various industries for coating materials with thin films. It offers several advantages, such as being eco-friendly, producing high-quality coatings, and enabling the creation of advanced technologies like microchips and solar panels. However, PVD also has its limitations, including low deposition rates, the need for a clean low-pressure vacuum, and high-quality sputtering targets. In contrast, Chemical Vapor Deposition (CVD) offers advantages like high versatility, the ability to coat complex shapes, and high deposition rates, but it also has disadvantages such as high-temperature requirements and difficulties in synthesizing multi-component materials. Understanding the pros and cons of both PVD and CVD is crucial for selecting the appropriate coating process for specific applications.
Key Points Explained:
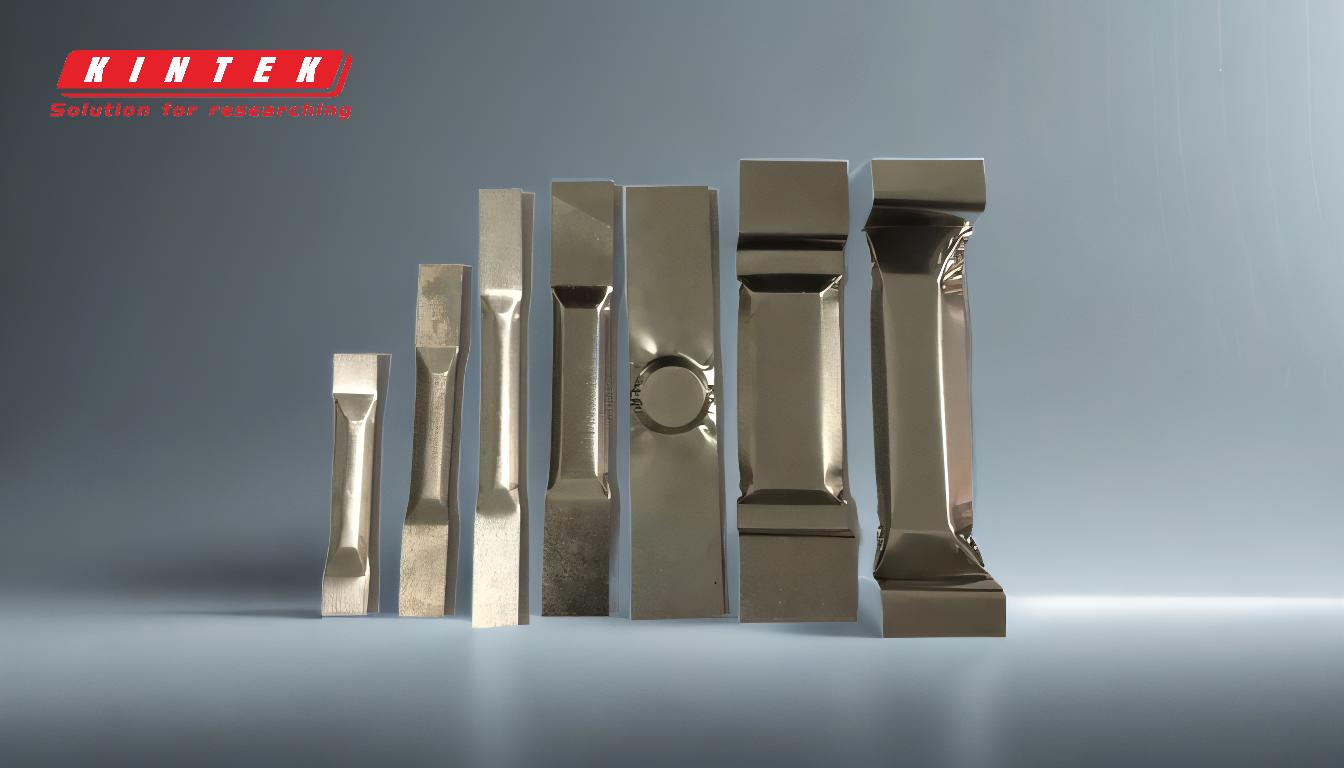
-
Eco-Friendly Nature of PVD:
- PVD is an environmentally friendly process as it does not produce waste during the coating process. This eliminates the need for disposal operations and further treatments after the coating is applied, making it a sustainable choice for industries looking to reduce their environmental footprint.
-
High-Quality Coatings:
- PVD is known for producing some of the toughest and most brilliant coatings available today. This makes it ideal for applications requiring high durability and aesthetic appeal, such as in the production of microchips and solar panels.
-
Limitations of Traditional PVD Techniques:
- Traditional PVD techniques have several drawbacks, including low deposition rates (around 1 nm/s), the need for a clean low-pressure vacuum, and relatively high working pressures (1 Pa to 100 Pa) to sustain a stable glow discharge. These factors can limit the efficiency and scalability of the PVD process.
-
Advantages of CVD Over PVD:
- CVD offers several advantages over PVD, including the ability to coat complex shapes and deep recesses, high deposition rates, and the ability to produce thick coatings. Additionally, CVD does not typically require an ultra-high vacuum, making it more economical in some cases.
-
Versatility and Control in CVD:
- CVD is highly versatile due to its reliance on chemical reactions, allowing for full control over the timing of the process. This makes it ideal for creating ultra-thin layers of materials, which are essential for producing electrical circuits and other advanced technologies.
-
Disadvantages of CVD:
- Despite its advantages, CVD has several disadvantages. It usually cannot be performed on-site and must be delivered to a coating center. Additionally, the process requires breaking down parts into individual components, and the size of the vacuum chamber is limited, making it difficult to coat larger surfaces. High-temperature requirements can also be problematic when working with certain materials.
-
Challenges in Synthesizing Multi-Component Materials with CVD:
- One of the significant challenges with CVD is the difficulty in synthesizing multi-component materials due to variations in vapor pressure, nucleation, and growth rates during the gas-to-particle conversion. This results in the heterogeneous composition of particles, which can affect the quality and uniformity of the coatings.
-
Comparison with Other Deposition Techniques:
- CVD has several advantages over other deposition techniques, such as sputtering and evaporation, including the ability to deposit films with high purity and uniformity. This makes CVD a preferred choice for applications requiring high-quality coatings.
-
Microwave Plasma Chemical Vapor Deposition:
- Microwave plasma chemical vapor deposition is an advanced form of CVD that uses microwave plasma to enhance the deposition process. This technique offers improved control over the deposition process and can produce high-quality coatings with enhanced properties.
In conclusion, both PVD and CVD have their unique advantages and disadvantages. The choice between these two processes depends on the specific requirements of the application, including the desired coating properties, the complexity of the shapes to be coated, and the environmental considerations. Understanding these factors is essential for making an informed decision when selecting a coating process.
Summary Table:
Aspect | PVD Advantages | PVD Disadvantages |
---|---|---|
Environmental Impact | Eco-friendly, no waste produced | - |
Coating Quality | High durability, brilliant coatings | Low deposition rates (~1 nm/s) |
Process Requirements | - | Requires clean low-pressure vacuum, high-quality sputtering targets |
Versatility | Ideal for microchips, solar panels | Limited scalability due to working pressures (1 Pa to 100 Pa) |
Comparison with CVD | - | CVD offers higher deposition rates, better for complex shapes, but requires high temps |
Need help choosing the right coating process for your application? Contact our experts today!