Physical Vapor Deposition (PVD) is a widely used coating technique in various industries, offering several advantages over other methods like Chemical Vapor Deposition (CVD). However, it also has its limitations. PVD operates at lower temperatures, making it safer and more suitable for coating sensitive materials or tools. It avoids the use of volatile chemicals, reducing harmful byproducts. On the downside, PVD can be more expensive due to the need for vacuum systems and specialized equipment. Additionally, it may have limitations in coating complex geometries uniformly. Understanding these pros and cons is essential for selecting the right process for specific applications.
Key Points Explained:
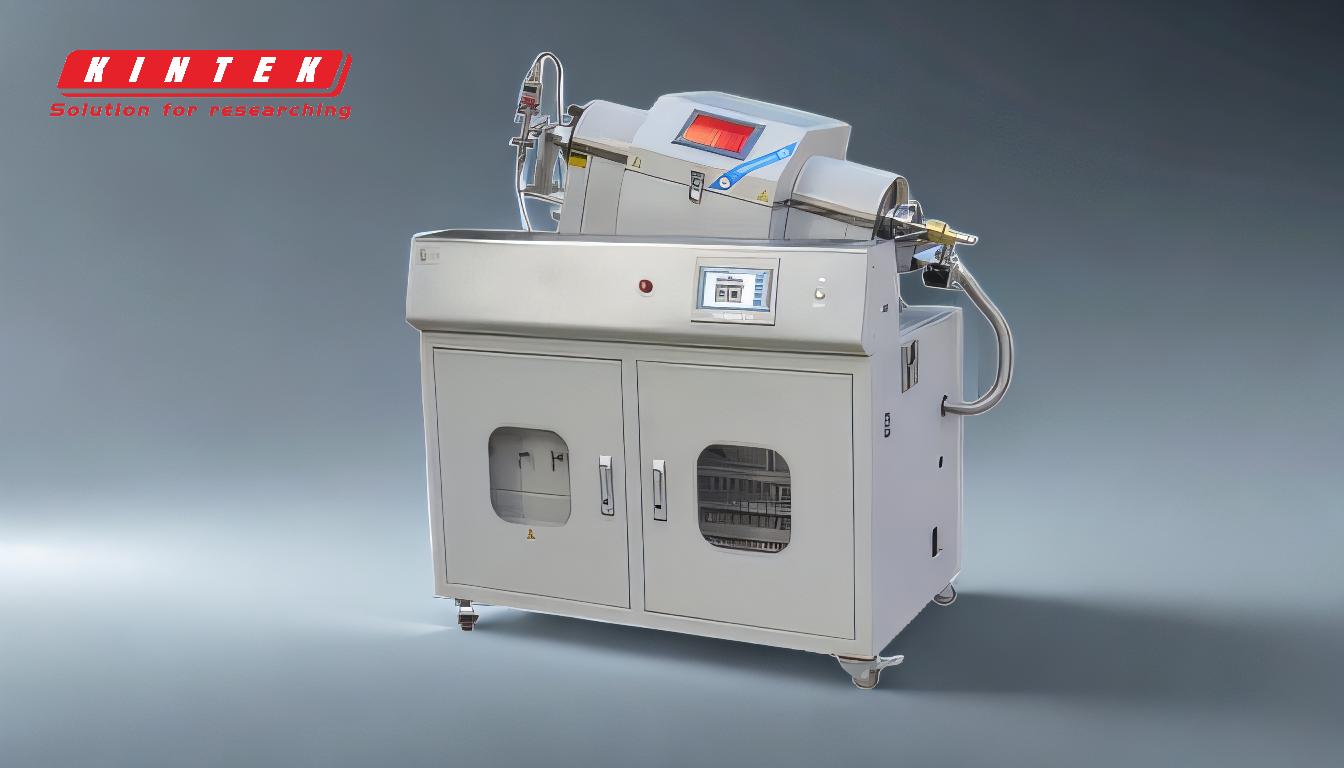
-
Advantages of PVD:
- Lower Operating Temperatures: PVD operates at lower temperatures compared to CVD, which helps prevent thermal degradation of sensitive materials. This makes it ideal for coating cutting tools and other heat-sensitive components.
- Safer Process: PVD does not involve volatile chemicals, reducing the risk of harmful gas emissions and making it a safer option for industrial applications.
- High-Quality Coatings: PVD produces dense, uniform, and high-purity coatings, which enhance the durability and performance of the coated materials.
- Environmental Benefits: The absence of toxic byproducts makes PVD an environmentally friendly choice compared to CVD.
-
Disadvantages of PVD:
- Higher Costs: PVD requires vacuum systems and specialized equipment, which can be expensive to install and maintain.
- Limited Uniformity on Complex Geometries: Achieving uniform coatings on complex or intricate shapes can be challenging with PVD, as the process relies on line-of-sight deposition.
- Slower Deposition Rates: PVD generally has slower deposition rates compared to CVD, which can increase production time and costs.
- Material Limitations: Some materials may not be suitable for PVD due to their properties or the need for specific precursor gases.
-
Comparison with Short Path Vacuum Distillation:
- While PVD and short path vacuum distillation both utilize vacuum systems, they serve different purposes. PVD is used for coating materials, whereas short path vacuum distillation is a separation technique for purifying compounds. Both processes benefit from reduced pressure, which lowers boiling points and minimizes thermal degradation. However, short path distillation is more focused on achieving high-purity distillates for sensitive organic compounds, while PVD emphasizes creating durable and high-performance coatings.
-
Applications and Suitability:
- PVD is widely used in industries such as aerospace, automotive, and electronics for coating tools, components, and decorative finishes. Its ability to produce hard, wear-resistant coatings makes it a preferred choice for cutting tools and molds.
- Short path vacuum distillation, on the other hand, is ideal for purifying heat-sensitive compounds in industries like pharmaceuticals, essential oils, and cannabis extraction. Its compact design and efficient operation make it suitable for small-scale and budget-conscious setups.
-
Cost and Space Considerations:
- PVD systems can be costly due to the need for vacuum chambers and specialized equipment. However, the long-term benefits of high-quality coatings often justify the investment.
- Short path distillation systems are more compact and cost-effective, making them accessible for smaller operations or those with limited space. Both processes, however, require careful consideration of initial costs and operational efficiency.
By weighing these advantages and disadvantages, users can determine whether PVD is the right choice for their specific needs, especially when compared to alternative methods like CVD or short path vacuum distillation.
Summary Table:
Aspect | Advantages | Disadvantages |
---|---|---|
Operating Temperatures | Lower temperatures prevent thermal degradation of sensitive materials. | - |
Safety | No volatile chemicals, reducing harmful emissions. | - |
Coating Quality | Dense, uniform, and high-purity coatings enhance durability. | Limited uniformity on complex geometries. |
Environmental Impact | No toxic byproducts, making it eco-friendly. | - |
Cost | - | Higher costs due to vacuum systems and specialized equipment. |
Deposition Rates | - | Slower deposition rates compared to CVD. |
Material Suitability | - | Some materials may not be suitable for PVD. |
Need help deciding if PVD is right for your application? Contact our experts today for personalized advice!