Chemical vapor deposition (CVD) is a highly versatile and widely used method for depositing thin films and coatings on various substrates. It offers numerous advantages, including the ability to produce high-purity, uniform, and durable coatings with precise control over the process. CVD is suitable for a wide range of materials, including metals, ceramics, and glass, and can be tailored to enhance properties such as corrosion resistance, abrasion resistance, and thermal conductivity. Additionally, it is a non-line-of-sight process, making it ideal for coating complex and precision surfaces. These features make CVD a preferred choice in industries requiring high-performance coatings for optical, mechanical, and chemical applications.
Key Points Explained:
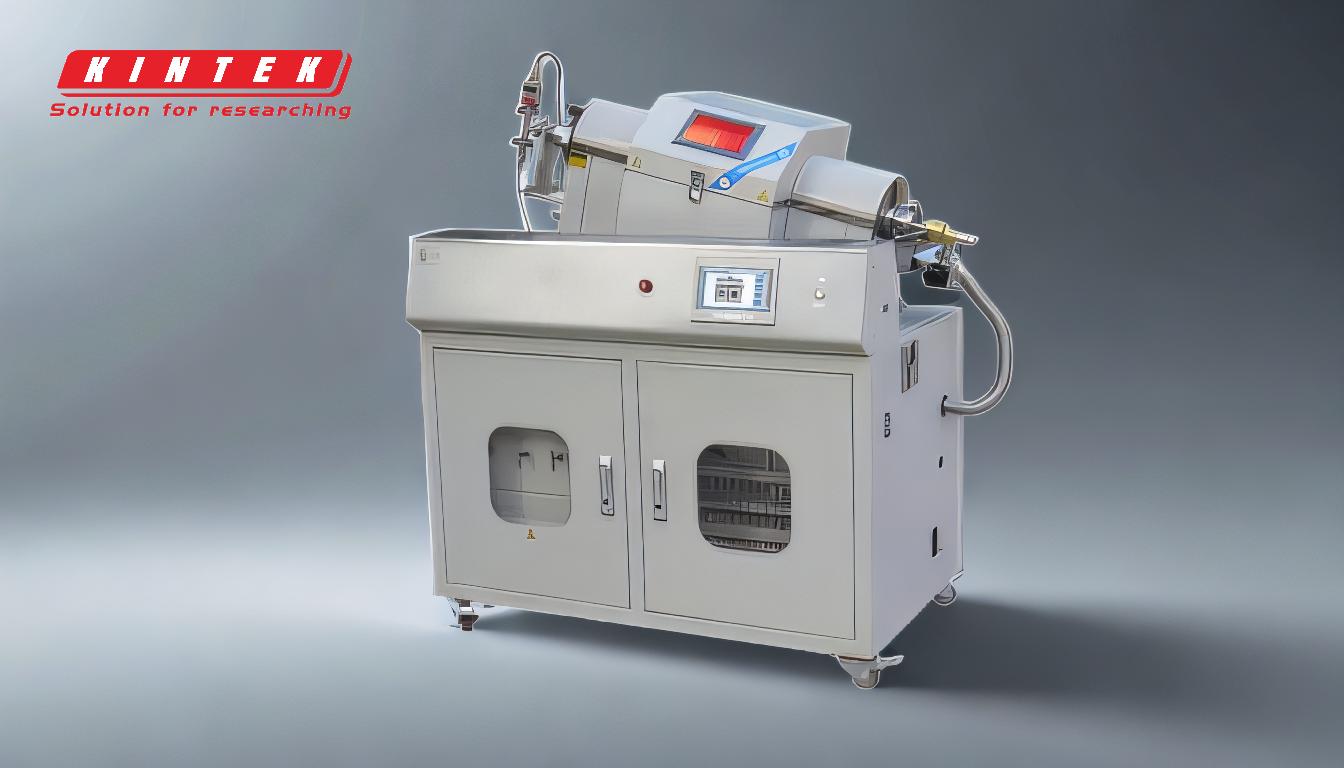
-
Versatility and Material Compatibility:
- CVD can be applied to a wide range of base materials, including metals, ceramics, and glass. This versatility makes it suitable for diverse industrial applications, from electronics to aerospace.
- The process allows for the optimization of gases to achieve specific properties, such as corrosion resistance, abrasion resistance, or high purity, depending on the application requirements.
-
High Deposition Rate and Uniformity:
- CVD offers a high deposition rate, ensuring efficient production of thin films and coatings.
- The process provides uniform coating thickness, even on complex geometries, which is critical for applications requiring precision and consistency.
-
High Purity and Durability:
- The coatings produced by CVD are of high purity, making them ideal for applications in industries like semiconductors and optics.
- The resulting films are durable and can withstand high-stress environments, extreme temperatures, and temperature variations, ensuring long-term performance.
-
Non-Line-of-Sight Process:
- Unlike other deposition methods, CVD does not require a direct line of sight between the source and the substrate. This makes it possible to coat intricate and complex surfaces uniformly, including internal features and hard-to-reach areas.
-
Surface Property Enhancement:
- CVD improves surface properties by creating smoother surfaces, enhancing electrical and thermal conductivity, and improving compatibility with other materials.
- The even buildup of coating material on the substrate ensures consistent performance and functionality.
-
Control and Precision:
- The process allows full control over the timing and parameters of the deposition, enabling precise customization of the coating properties.
- This level of control is essential for applications in industries such as microelectronics, where ultra-thin layers and precise material properties are required.
-
Applications in High-Performance Coatings:
- CVD is widely used in the development of high-performance thin solid coatings for optical, mechanical, and chemical operations.
- Its ability to produce coatings with tailored properties makes it indispensable in industries such as semiconductor manufacturing, aerospace, and energy.
In summary, chemical vapor deposition is a highly advantageous method for producing thin films and coatings with exceptional purity, durability, and uniformity. Its versatility, precision, and ability to enhance surface properties make it a cornerstone technology in modern industrial manufacturing.
Summary Table:
Advantage | Description |
---|---|
Versatility | Compatible with metals, ceramics, and glass for diverse applications. |
High Deposition Rate | Efficient production of thin films with uniform thickness. |
High Purity & Durability | Ideal for semiconductors, optics, and high-stress environments. |
Non-Line-of-Sight Process | Coats complex and intricate surfaces uniformly. |
Surface Property Enhancement | Improves conductivity, smoothness, and material compatibility. |
Precision & Control | Customizable coatings for ultra-thin layers and specific properties. |
High-Performance Applications | Used in semiconductor, aerospace, and energy industries for tailored coatings. |
Unlock the potential of CVD for your industry—contact our experts today to learn more!