Chemical vapor deposition (CVD) is a highly advantageous method for synthesizing nanomaterials due to its versatility, precision, and ability to produce high-quality coatings. It is widely used across various industries because it can deposit a wide range of materials, including ceramics, metals, and graphene, with excellent purity, durability, and uniformity. CVD is particularly valued for its ability to coat complex and precision surfaces, withstand extreme temperatures, and produce materials with tailored properties by adjusting deposition parameters. Additionally, it is relatively affordable, easy to operate, and offers a high deposition rate with commendable adhesion, making it a preferred choice for applications requiring high-performance coatings.
Key Points Explained:
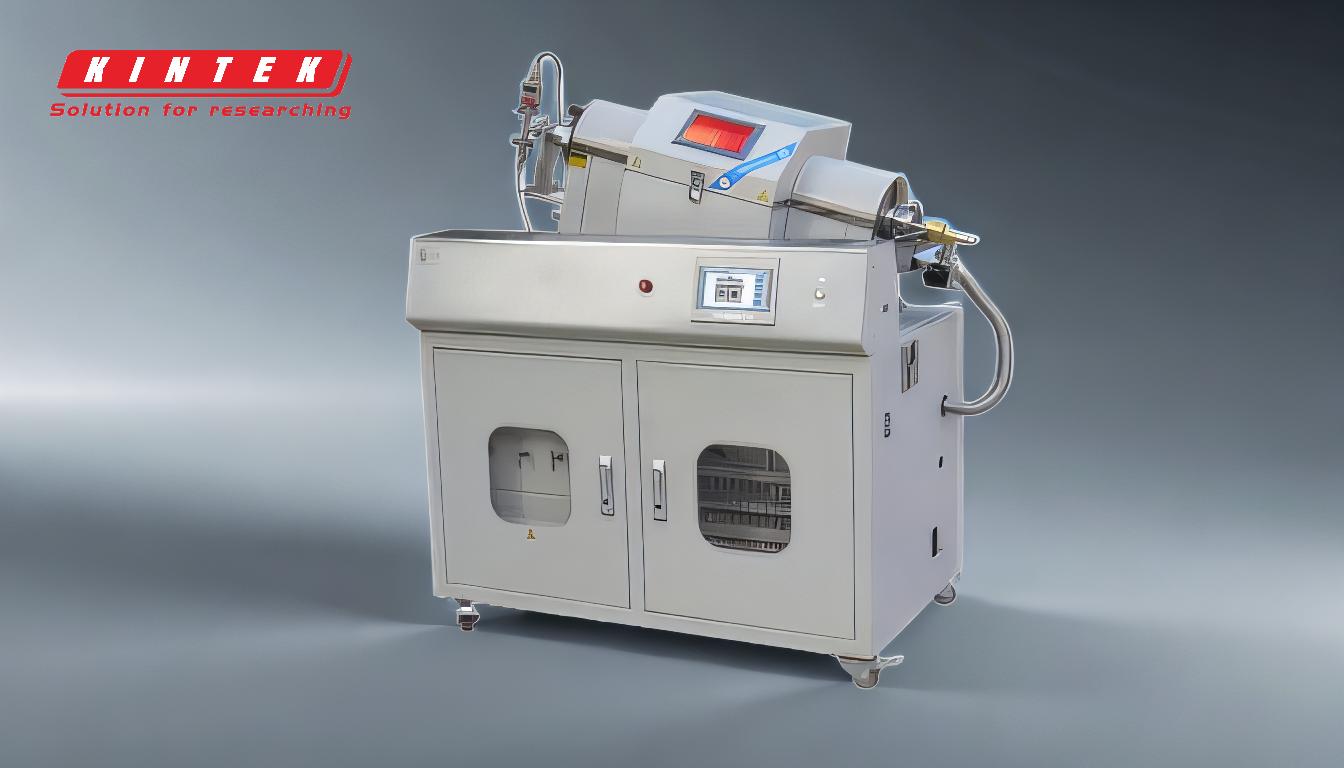
-
Versatility in Material Deposition
- CVD can deposit a wide variety of materials, including ceramics, metals, glass, and graphene. This makes it suitable for diverse applications, from electronics to protective coatings.
- The method allows for the optimization of gases to achieve specific properties such as corrosion resistance, abrasion resistance, or high purity, depending on the application requirements.
-
High-Quality Coatings
- CVD produces coatings with high purity, density, and durability, making them resistant to agitation, damage, and high-stress environments.
- The process ensures uniform coating, even on complex and precision surfaces, due to its good wrap-around properties.
-
Tailored Material Properties
- By adjusting deposition parameters such as temperature, pressure, and gas composition, the properties of the deposited materials can be precisely controlled. This includes crystallinity, residual stress, and thickness, enabling the creation of materials with specific performance characteristics.
-
Suitability for Complex and Precision Surfaces
- CVD is capable of coating intricate and precision surfaces, making it ideal for applications in microelectronics, optics, and other high-tech industries.
- The non-line-of-sight nature of the process ensures uniform coverage even on irregular geometries.
-
Durability in Extreme Conditions
- Coatings produced by CVD can withstand extreme temperatures and temperature variations, making them suitable for use in harsh environments such as aerospace and automotive industries.
-
Cost-Effectiveness and Ease of Operation
- CVD is relatively affordable compared to other coating methods, and the equipment is simple to operate and maintain.
- The high deposition rate and commendable adhesion further contribute to its cost-effectiveness and efficiency.
-
Applications in Advanced Technologies
- CVD is ideal for producing ultra-thin layers of materials, making it essential for applications such as electrical circuits, sensors, and nanotechnology.
- Its ability to create high-purity products with controlled properties makes it a preferred method for research and industrial applications requiring precision and reliability.
In summary, chemical vapor deposition stands out as a versatile, precise, and cost-effective method for synthesizing nanomaterials with tailored properties, making it indispensable in modern material science and engineering.
Summary Table:
Advantage | Description |
---|---|
Versatility in Material Deposition | Deposits ceramics, metals, glass, and graphene; optimizes gases for specific properties. |
High-Quality Coatings | Produces coatings with high purity, density, and durability; ensures uniform coating. |
Tailored Material Properties | Adjusts temperature, pressure, and gas composition to control crystallinity, stress, and thickness. |
Suitability for Complex Surfaces | Coats intricate and precision surfaces; ideal for microelectronics and optics. |
Durability in Extreme Conditions | Withstands extreme temperatures and variations; suitable for harsh environments. |
Cost-Effectiveness | Affordable, easy to operate, and offers high deposition rates with excellent adhesion. |
Applications in Advanced Tech | Essential for electrical circuits, sensors, and nanotechnology; produces high-purity materials. |
Interested in leveraging CVD for your nanomaterial needs? Contact our experts today to learn more!