Electrodeposition, also known as electroplating, is a widely used process in various industries due to its numerous advantages. It involves the deposition of a metal or alloy onto a conductive surface using an electric current. This process offers benefits such as enhanced corrosion resistance, improved wear resistance, better electrical conductivity, and aesthetic appeal. Additionally, electrodeposition allows for precise control over the thickness and composition of the deposited layer, making it suitable for applications requiring high precision. The process is also cost-effective, scalable, and environmentally friendly compared to other coating methods. Below, the key advantages of electrodeposition are explained in detail.
Key Points Explained:
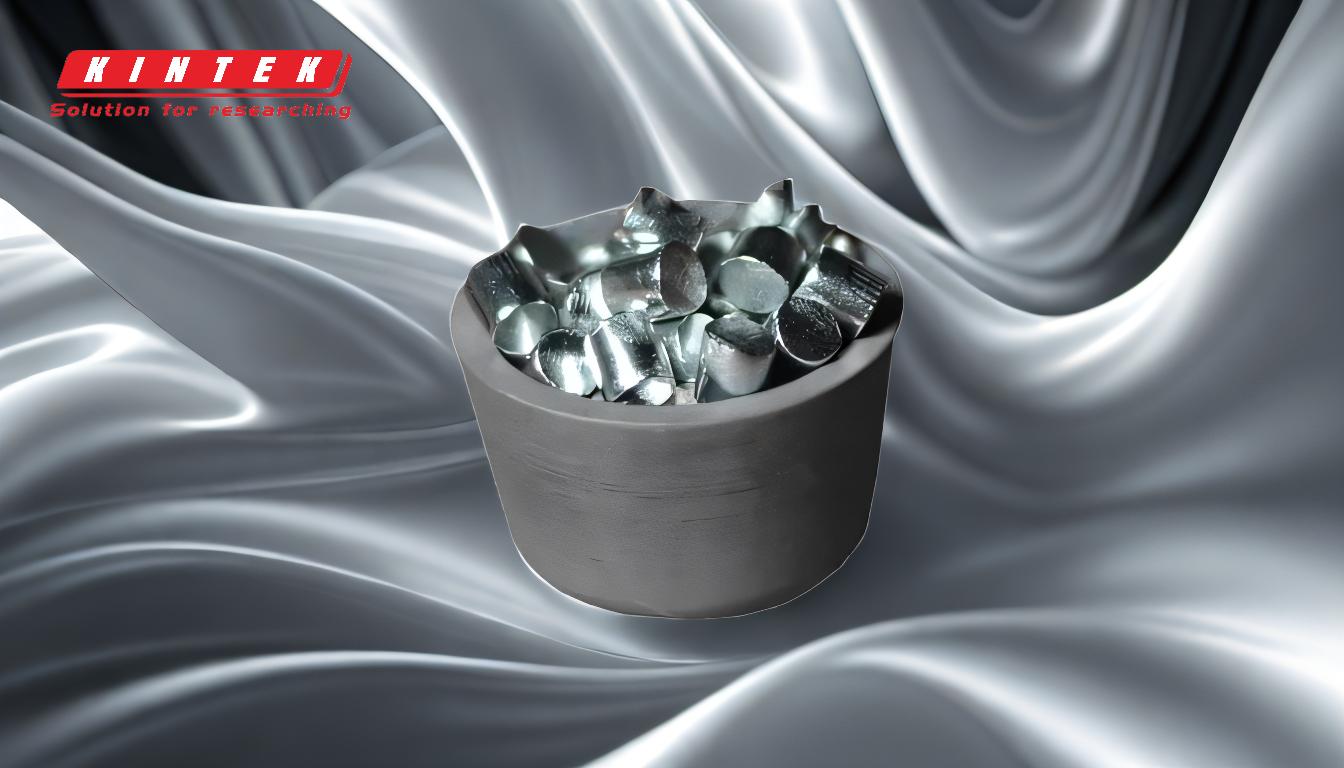
-
Enhanced Corrosion Resistance:
- Electrodeposition can significantly improve the corrosion resistance of a substrate by applying a protective metal coating. For example, zinc or nickel coatings are commonly used to protect steel from rusting.
- The deposited layer acts as a barrier, preventing the underlying material from coming into contact with corrosive elements such as moisture, oxygen, or chemicals.
- This advantage is particularly valuable in industries like automotive, aerospace, and marine, where components are exposed to harsh environments.
-
Improved Wear Resistance:
- Electrodeposited coatings, such as chromium or hard nickel, can enhance the wear resistance of a surface, making it more durable and long-lasting.
- This is crucial for components subjected to friction, abrasion, or mechanical stress, such as engine parts, tools, and industrial machinery.
- The ability to tailor the hardness and thickness of the coating ensures optimal performance for specific applications.
-
Better Electrical Conductivity:
- Electrodeposition is often used to improve the electrical conductivity of surfaces. For instance, copper or silver coatings are applied to connectors, circuit boards, and other electronic components.
- This ensures efficient electrical contact and reduces energy loss, which is critical in the electronics and telecommunications industries.
- The process also allows for the creation of uniform coatings, which is essential for maintaining consistent electrical performance.
-
Aesthetic Appeal:
- Electrodeposition can be used to enhance the appearance of products by applying decorative coatings such as gold, silver, or chrome.
- These coatings provide a shiny, reflective finish that is visually appealing and often used in jewelry, automotive trim, and consumer electronics.
- The ability to achieve a high-quality finish with excellent adhesion makes electrodeposition a preferred choice for decorative applications.
-
Precise Control Over Coating Thickness and Composition:
- One of the standout advantages of electrodeposition is the ability to precisely control the thickness and composition of the deposited layer.
- This is achieved by adjusting parameters such as current density, bath composition, and deposition time.
- Such precision is essential for applications requiring specific performance characteristics, such as in the aerospace and medical device industries.
-
Cost-Effectiveness:
- Electrodeposition is a cost-effective coating method compared to alternatives like physical vapor deposition (PVD) or chemical vapor deposition (CVD).
- The process requires relatively low capital investment and operational costs, making it accessible for small and large-scale production.
- Additionally, the ability to reuse plating solutions and recover metals from waste streams further reduces costs.
-
Scalability and Versatility:
- Electrodeposition is highly scalable, making it suitable for both small-batch and mass production.
- It can be applied to a wide range of materials, including metals, plastics, and ceramics, provided the substrate is conductive or can be made conductive through pre-treatment.
- This versatility makes it a preferred choice across diverse industries, from automotive to electronics to decorative arts.
-
Environmental Friendliness:
- Modern electrodeposition processes are designed to minimize environmental impact by using less toxic chemicals and implementing waste treatment systems.
- The ability to recover and recycle metals from plating baths reduces waste and conserves resources.
- Compared to other coating methods, electrodeposition often has a lower carbon footprint, aligning with sustainability goals.
-
Uniform Coating on Complex Geometries:
- Electrodeposition can produce uniform coatings even on complex-shaped objects, such as threaded fasteners, gears, or intricate jewelry.
- This is achieved through proper bath agitation and the use of specialized fixtures to ensure even current distribution.
- The ability to coat complex geometries without compromising quality is a significant advantage in manufacturing.
-
Improved Adhesion and Durability:
- Electrodeposited coatings exhibit excellent adhesion to the substrate, ensuring long-term durability and performance.
- Pre-treatment processes, such as cleaning and activation, further enhance adhesion by removing contaminants and creating a receptive surface.
- This results in coatings that are less prone to peeling, flaking, or delamination, even under demanding conditions.
In summary, electrodeposition offers a wide range of advantages, including enhanced corrosion and wear resistance, improved electrical conductivity, aesthetic appeal, precise control over coating properties, cost-effectiveness, scalability, environmental friendliness, and the ability to coat complex geometries uniformly. These benefits make it a versatile and valuable process across numerous industries, from electronics and automotive to decorative arts and aerospace.
Summary Table:
Advantage | Description |
---|---|
Enhanced Corrosion Resistance | Protects substrates from rust and corrosion, ideal for harsh environments. |
Improved Wear Resistance | Increases durability for components under friction or stress. |
Better Electrical Conductivity | Ensures efficient electrical contact in electronics and telecommunications. |
Aesthetic Appeal | Provides decorative finishes like gold, silver, or chrome for visual appeal. |
Precise Control Over Coating | Allows exact thickness and composition adjustments for high-precision needs. |
Cost-Effectiveness | More affordable than PVD or CVD, with reusable plating solutions. |
Scalability and Versatility | Suitable for small-batch and mass production across various materials. |
Environmental Friendliness | Minimizes environmental impact with less toxic chemicals and waste recycling. |
Uniform Coating on Complex Shapes | Ensures even coatings on intricate geometries without quality loss. |
Improved Adhesion and Durability | Enhances coating adhesion, reducing peeling or flaking under demanding conditions. |
Unlock the full potential of electrodeposition for your projects—contact our experts today!