Metal sintering is a versatile and efficient manufacturing process that offers numerous advantages, making it a preferred choice for producing high-performance components. It enhances material properties such as strength, durability, conductivity, and porosity control, while also enabling the creation of complex shapes with high precision. The process is cost-effective, energy-efficient, and environmentally friendly, making it suitable for large-scale production and applications involving high-melting-point materials. Below, the key advantages of metal sintering are explained in detail.
Key Points Explained:
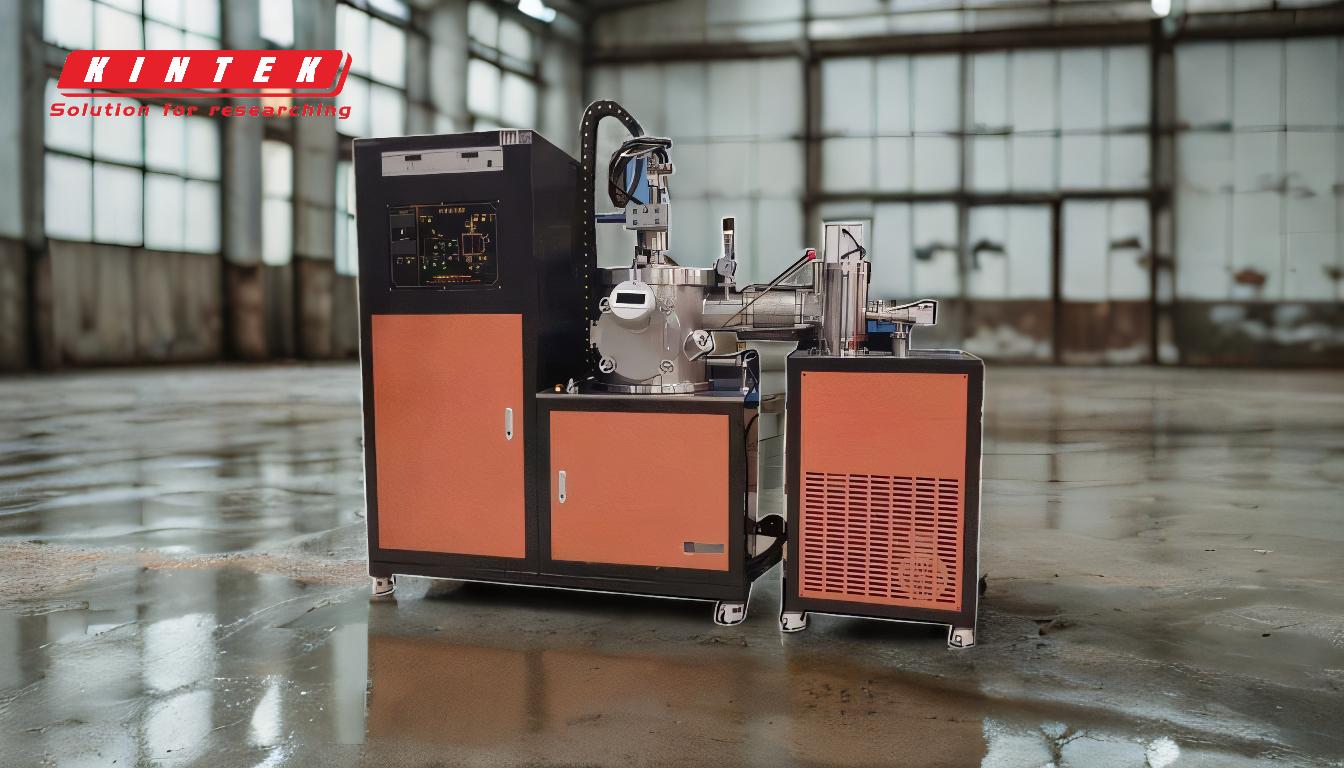
-
Enhanced Material Properties
- Sintering reduces surface porosity, which improves properties such as:
- Strength and Durability: Minimized porosity enhances tensile strength and structural integrity, making parts more resistant to wear and deformation.
- Conductivity: Reduced porosity improves electrical and thermal conductivity, which is critical for applications like heat pipes, electrical contacts, and bearings.
- Corrosion Resistance: Denser materials with fewer pores are less susceptible to corrosion, extending the lifespan of components.
- The process also allows for the creation of specific porosity levels, which is beneficial for filters, catalysts, and other applications requiring gas absorbency.
- Sintering reduces surface porosity, which improves properties such as:
-
Complex Shape Formation
- Metal sintering enables the production of intricate and complex shapes that are difficult or impossible to achieve with traditional manufacturing methods like casting or machining.
- This is particularly useful for industries requiring precision components, such as aerospace, automotive, and medical devices.
-
High Dimensional Precision and Consistency
- Sintering ensures high dimensional accuracy, producing parts that are very close to the desired shape and size.
- The process is highly repeatable, making it ideal for large-scale production where consistency and reliability are critical.
-
Energy Efficiency and Environmental Benefits
- Sintering requires less energy compared to melting metals, making it a more energy-efficient and cost-effective process.
- It produces no harmful emissions, aligning with green manufacturing practices and reducing environmental impact.
-
Creation of Isotropic Materials
- Sintered materials exhibit uniform properties in all directions (isotropic), which is advantageous for applications requiring consistent performance, such as turbine blades and structural components.
-
Improved Mechanical Handling Strength
- The dense bond formed between particles during sintering enhances the mechanical handling strength of the final product, reducing the risk of damage during assembly or use.
-
Self-Lubricating and Vibration Damping Properties
- The dense bond between particles in sintered materials can provide self-lubricating properties, reducing friction and wear in moving parts.
- The material's structure also offers vibration damping, which is beneficial for applications like automotive components and machinery.
-
Cost-Effectiveness and Scalability
- Sintering is a cost-effective method for producing high-quality parts, particularly for large-scale production.
- The ability to work with high-melting-point materials without melting them further reduces costs and expands the range of materials that can be used.
-
Control Over Porosity and Material Composition
- Sintering allows for precise control over porosity, which is essential for applications like filters, catalysts, and porous bearings.
- The process also enables the diffusion of elements like nickel, copper, and graphite, enhancing the material's properties and performance.
-
Versatility in Material Selection
- Sintering can be used with a wide range of materials, including those with very high melting points, such as tungsten and molybdenum.
- This versatility makes it suitable for demanding applications in industries like aerospace, defense, and energy.
-
Improved Surface Finish and Cleanliness
- The sintering process reduces surface oxygen and eliminates the need for lubricants in compacted powders, resulting in cleaner and smoother surfaces.
- This is particularly important for applications requiring high surface quality, such as jewelry and medical implants.
-
Manufacturing of Nearly Net-Shaped Objects
- Sintering produces parts that are close to their final shape, reducing the need for additional machining and minimizing material waste.
- This contributes to cost savings and faster production times.
In summary, metal sintering is a highly advantageous manufacturing process that combines enhanced material properties, cost-effectiveness, and environmental benefits. Its ability to produce complex shapes with high precision and consistency makes it a valuable technique for a wide range of industries, from automotive and aerospace to medical and consumer goods. The process's versatility, energy efficiency, and scalability further solidify its position as a leading choice for modern manufacturing.
Summary Table:
Advantage | Key Benefit |
---|---|
Enhanced Material Properties | Improved strength, durability, conductivity, and corrosion resistance. |
Complex Shape Formation | Enables intricate designs for aerospace, automotive, and medical industries. |
High Dimensional Precision | Ensures consistent, accurate parts for large-scale production. |
Energy Efficiency | Reduces energy consumption and environmental impact. |
Isotropic Materials | Uniform properties in all directions for consistent performance. |
Cost-Effectiveness | Affordable for high-quality, large-scale production. |
Versatility in Material Selection | Works with high-melting-point materials like tungsten and molybdenum. |
Improved Surface Finish | Cleaner, smoother surfaces ideal for medical implants and jewelry. |
Nearly Net-Shaped Objects | Minimizes material waste and machining requirements. |
Ready to leverage the benefits of metal sintering for your manufacturing needs? Contact our experts today to get started!