Multi-cavity molds are a popular choice in injection molding due to their ability to significantly increase production efficiency and reduce costs. By allowing multiple parts to be produced simultaneously in a single cycle, these molds optimize cycle time and lower the per-unit cost of each part. This makes them ideal for high-volume production runs where consistency, speed, and cost-effectiveness are critical. Below, we explore the key advantages of multi-cavity molds in detail.
Key Points Explained:
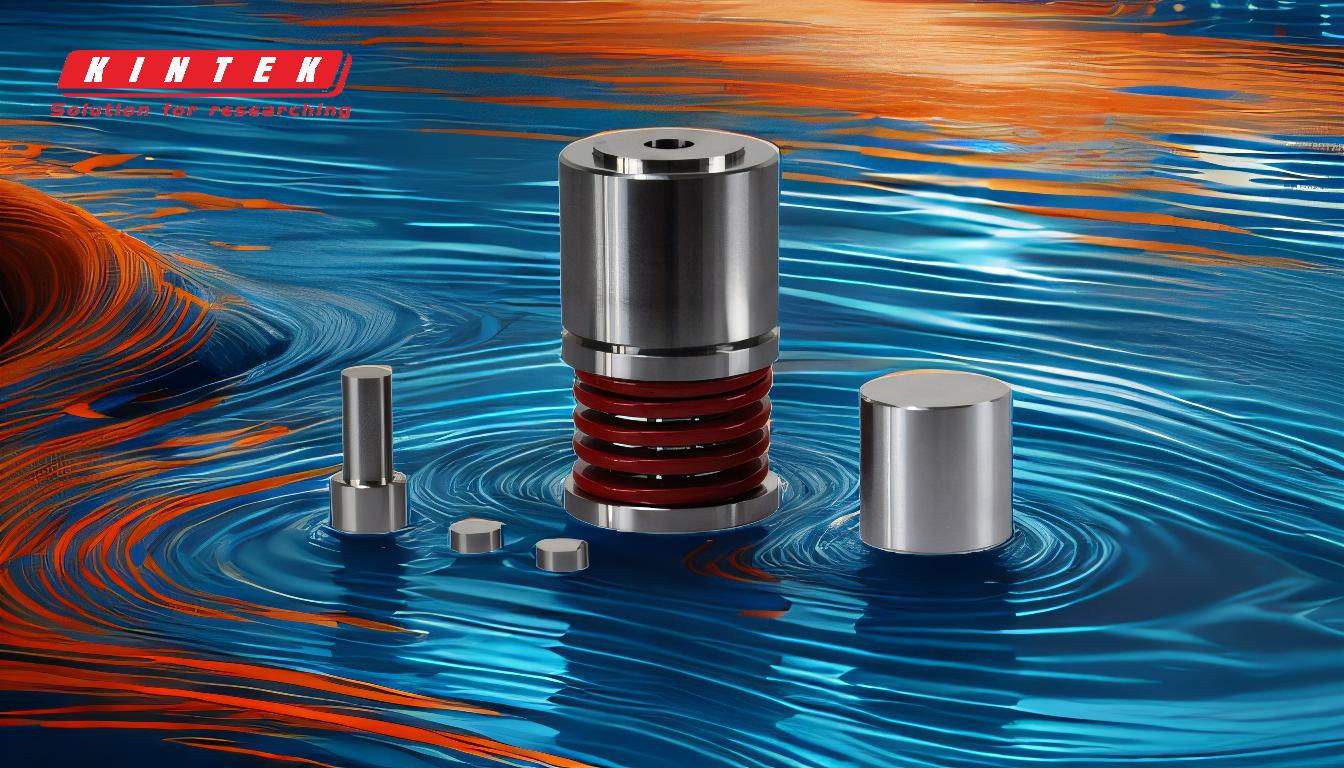
-
Increased Production Efficiency
- Multi-cavity molds enable the production of multiple parts in a single injection molding cycle, reducing the overall production time.
- By maximizing the use of each cycle, manufacturers can achieve higher output rates without increasing machine runtime.
- This efficiency is particularly beneficial for large-scale production runs, where time savings translate directly into cost savings.
-
Lower Per-Unit Cost
- Since multiple parts are produced simultaneously, the cost of materials, labor, and machine operation is distributed across a larger number of units.
- This reduces the per-unit cost of each part, making multi-cavity molds a cost-effective solution for high-volume manufacturing.
- The initial investment in a multi-cavity mold is often offset by the long-term savings in production costs.
-
Consistency and Uniformity
- Multi-cavity molds ensure that all parts produced in a single cycle are identical, maintaining high levels of consistency and quality.
- This uniformity is crucial for industries where precision and repeatability are essential, such as automotive, medical, and consumer electronics.
-
Optimal Use of Machine Capacity
- By producing multiple parts in one cycle, multi-cavity molds make full use of the injection molding machine's capacity.
- This reduces idle time and ensures that the machine operates at peak efficiency, further enhancing productivity.
-
Reduced Material Waste
- Multi-cavity molds minimize material waste by ensuring that each cycle produces the maximum number of usable parts.
- This is particularly important for expensive or specialized materials, where waste reduction can lead to significant cost savings.
-
Scalability for High-Volume Production
- Multi-cavity molds are ideal for scaling up production to meet high demand without requiring additional machines or significant changes to the production process.
- This scalability makes them a versatile solution for manufacturers looking to expand their operations.
-
Energy Efficiency
- Producing multiple parts in a single cycle reduces the energy consumption per part, contributing to more sustainable manufacturing practices.
- This energy efficiency aligns with the growing demand for environmentally friendly production methods.
-
Flexibility in Design
- Multi-cavity molds can be designed to produce different parts within the same mold, offering flexibility for manufacturers with diverse product lines.
- This versatility allows for greater adaptability in meeting varying production needs.
In summary, multi-cavity molds offer a range of advantages, including increased production efficiency, lower per-unit costs, and improved consistency. They are particularly well-suited for high-volume manufacturing, where their ability to optimize cycle time and reduce waste can lead to significant cost savings and operational improvements. For equipment and consumable purchasers, investing in multi-cavity molds can provide a competitive edge by enhancing productivity and reducing overall production costs.
Summary Table:
Advantage | Description |
---|---|
Increased Efficiency | Produce multiple parts per cycle, reducing production time and boosting output. |
Lower Per-Unit Cost | Distribute costs across more units, reducing expenses per part. |
Consistency & Uniformity | Ensure identical parts for precision-critical industries. |
Optimal Machine Use | Maximize machine capacity and reduce idle time. |
Reduced Material Waste | Minimize waste by producing more usable parts per cycle. |
Scalability | Easily scale production without additional machines or process changes. |
Energy Efficiency | Lower energy consumption per part, supporting sustainable practices. |
Design Flexibility | Produce different parts in the same mold for diverse product lines. |
Ready to enhance your production efficiency? Contact us today to explore multi-cavity mold solutions!