Plasma Enhanced Chemical Vapor Deposition (PECVD) is a highly advantageous thin-film deposition technique that combines the benefits of chemical vapor deposition (CVD) with the added energy of plasma. This method allows for lower processing temperatures, improved film properties, and enhanced control over deposition processes. PECVD is widely used in industries requiring high-quality thin films with excellent electrical, optical, and mechanical properties. Below, the key advantages of PECVD are explained in detail.
Key Points Explained:
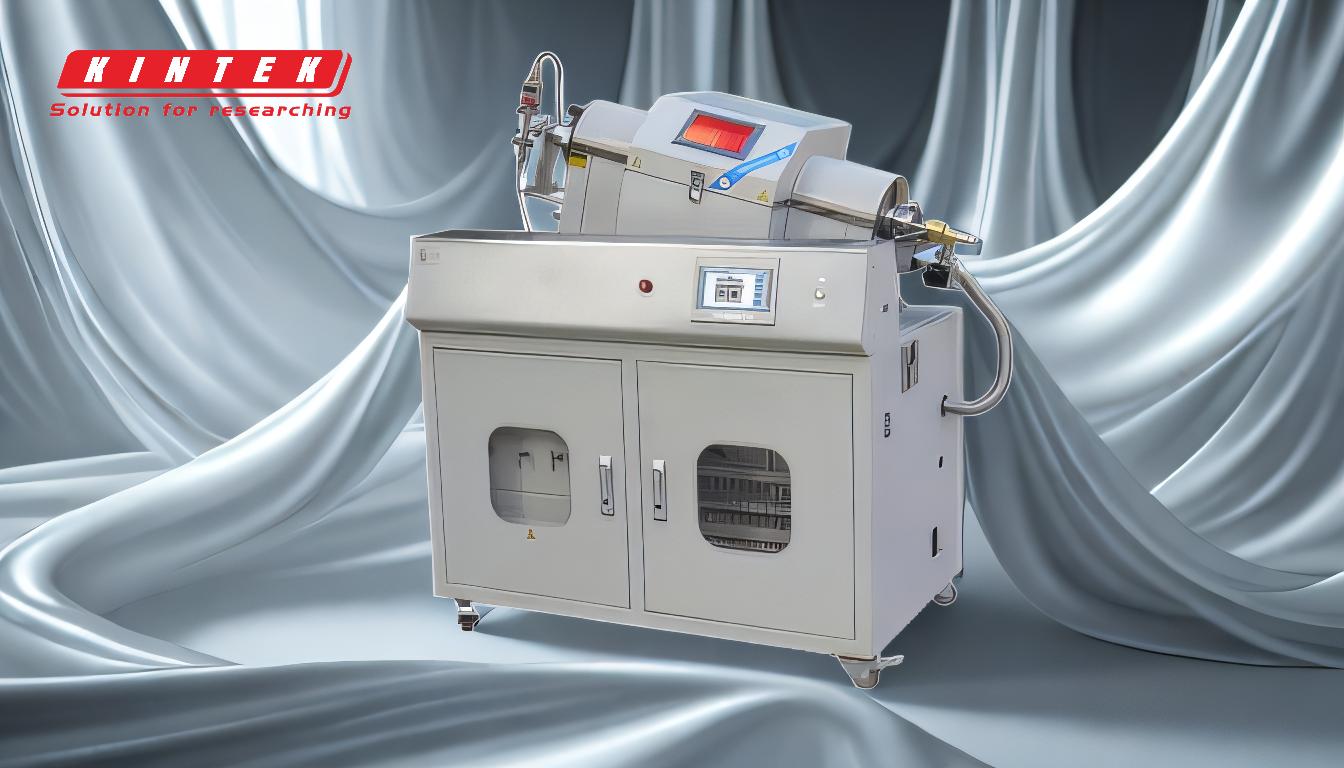
-
Low Deposition Temperature
- PECVD operates at significantly lower temperatures (200-400°C) compared to traditional CVD methods like LPCVD (425-900°C).
- The use of plasma provides the necessary energy to break stable volatile precursors, reducing the reliance on thermal energy.
- This makes PECVD suitable for temperature-sensitive substrates, such as polymers or materials that degrade at high temperatures.
- Lower temperatures also reduce energy consumption, leading to cost savings and increased throughput.
-
Excellent Electrical Properties of Deposited Films
- PECVD produces films with superior electrical properties, such as high dielectric strength and low leakage currents.
- These properties are critical for applications in microelectronics, such as insulating layers in integrated circuits or passivation layers in semiconductor devices.
- The plasma-enhanced process ensures a high degree of control over film composition and uniformity, which directly impacts electrical performance.
-
Good Substrate Adhesion
- PECVD films exhibit excellent adhesion to a wide range of substrates, including metals, ceramics, and polymers.
- The plasma activation of the substrate surface enhances bonding between the film and the substrate, ensuring durability and reliability.
- This is particularly important for applications requiring robust coatings, such as protective layers in harsh environments.
-
Excellent Step Coverage
- PECVD provides excellent step coverage, meaning it can uniformly coat complex or irregular substrate geometries.
- This is achieved through the combination of plasma energy and controlled gas flow, which ensures even deposition over high-aspect-ratio features.
- This capability is essential for advanced semiconductor manufacturing, where precise film deposition on intricate structures is required.
-
Improved Film Purity and Density
- The plasma environment in PECVD promotes the formation of dense, high-purity films with minimal defects.
- This results in films with superior mechanical, optical, and thermal properties, making them ideal for demanding applications.
- For example, PECVD is used to deposit silicon nitride films for optical coatings and barrier layers in solar cells.
-
Energy Efficiency and Cost Reduction
- By operating at lower temperatures and utilizing plasma energy, PECVD reduces overall energy consumption compared to traditional CVD methods.
- This leads to lower operational costs and a smaller environmental footprint.
- Additionally, the increased throughput and reduced processing times further enhance cost-effectiveness.
-
Versatility and Control Over Film Properties
- PECVD allows for precise control over film properties such as composition, hardness, conductivity, and transparency.
- This versatility enables the engineering of thin films tailored to specific applications, such as anti-reflective coatings, wear-resistant layers, or conductive films.
- The ability to fine-tune film properties makes PECVD a preferred choice for industries ranging from electronics to aerospace.
-
Applications in Advanced Technologies
- PECVD is widely used in the fabrication of microelectronic devices, including shallow trench isolation, sidewall isolation, and metal-linked media isolation.
- It is also employed in the production of optical coatings, solar cells, and protective coatings for various industrial applications.
- The combination of low-temperature processing and high-quality film deposition makes PECVD a cornerstone technology in modern manufacturing.
In summary, PECVD offers a unique combination of low-temperature processing, superior film properties, and enhanced control over deposition processes. These advantages make it an indispensable tool for industries requiring high-performance thin films with tailored properties.
Summary Table:
Advantage | Key Benefit |
---|---|
Low Deposition Temperature | Operates at 200-400°C, ideal for temperature-sensitive substrates. |
Excellent Electrical Properties | High dielectric strength, low leakage currents for microelectronics. |
Good Substrate Adhesion | Strong bonding to metals, ceramics, and polymers for durable coatings. |
Excellent Step Coverage | Uniform coating on complex geometries, essential for semiconductor manufacturing. |
Improved Film Purity and Density | Dense, high-purity films with superior mechanical and optical properties. |
Energy Efficiency and Cost Reduction | Lower energy consumption, reduced operational costs, and faster throughput. |
Versatility and Control | Tailored film properties for specific applications like anti-reflective coatings. |
Applications in Advanced Technologies | Used in microelectronics, solar cells, and protective coatings. |
Unlock the potential of PECVD for your projects—contact our experts today to learn more!