Physical Vapor Deposition (PVD) is a versatile and advanced coating technology that offers numerous advantages across various industries. It is widely used for creating thin films and coatings with exceptional quality, precision, and durability. PVD operates at lower temperatures, reducing the risk of thermal damage to substrates, and produces coatings with high hardness, wear resistance, and corrosion resistance. These coatings are ideal for applications in industries such as automotive, aerospace, cutting tools, medical devices, and jewelry. Additionally, PVD is environmentally friendly, cost-effective, and suitable for both high-volume and small-batch production, making it a preferred choice for modern manufacturing and decorative applications.
Key Points Explained:
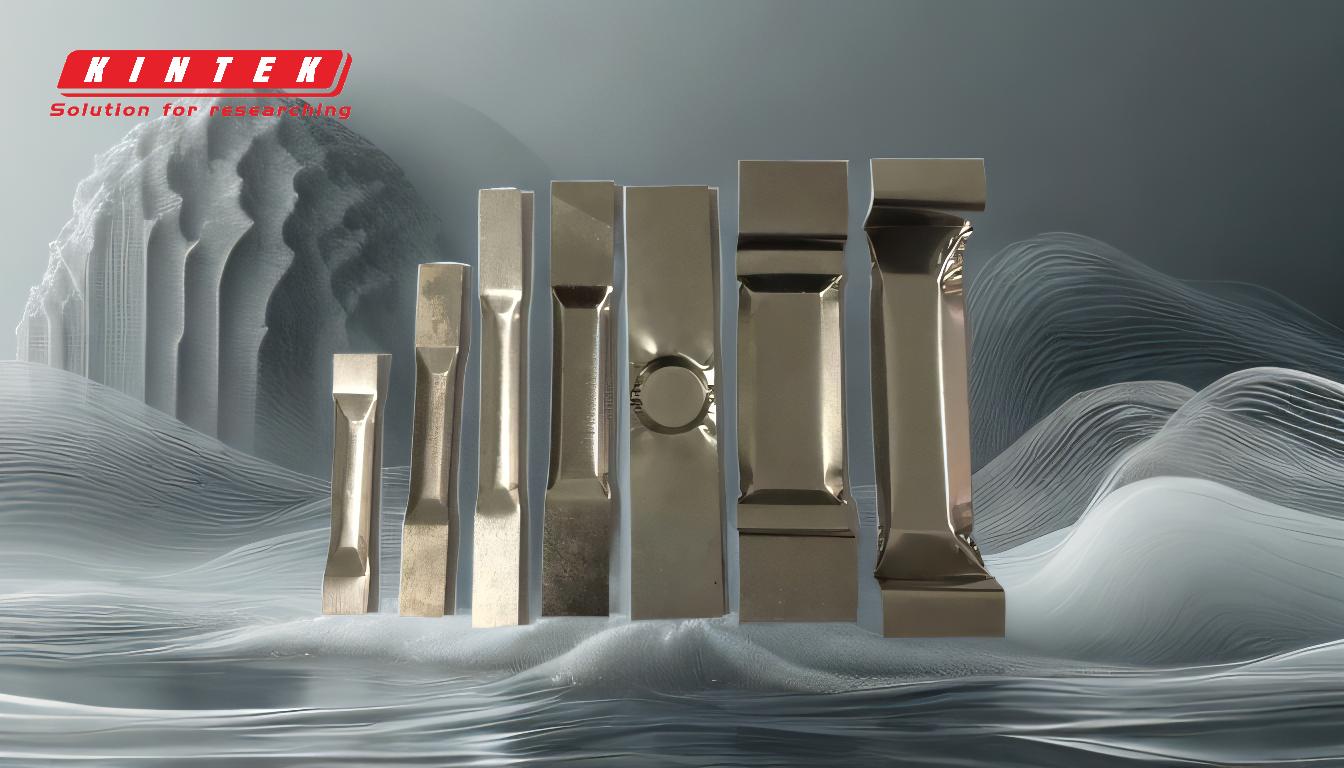
-
High-Quality Thin Films and Coatings
- PVD enables the creation of thin films and coatings with exceptional quality and accuracy. The process allows for precise control over coating thickness, typically ranging from 0.02 to 5 microns, ensuring uniformity and consistency.
- This precision is particularly beneficial for industries like semiconductors, optoelectronics, and cutting tools, where high-performance coatings are essential.
-
Lower Process Temperatures
- PVD operates at relatively low temperatures (around 500 °C), which minimizes the risk of thermal distortion or damage to the substrate.
- This characteristic makes PVD suitable for heat-sensitive materials, such as plastics and certain metals, ensuring that the original properties of the substrate remain intact.
-
Enhanced Durability and Wear Resistance
- PVD coatings are known for their high hardness and wear resistance, making them ideal for applications in cutting tools, molds, and industrial components.
- The compressive stress formed during the PVD process prevents crack formation and expansion, enhancing the durability of the coated products.
-
Corrosion and Chemical Resistance
- PVD coatings provide excellent corrosion resistance, protecting substrates from environmental factors and chemical exposure.
- This makes PVD-coated products suitable for harsh environments, such as those found in the automotive, aerospace, and marine industries.
-
Aesthetic and Decorative Applications
- PVD can replicate the appearance of expensive metals like gold, brass, bronze, and copper, offering a cost-effective alternative for decorative purposes.
- It is widely used in jewelry, watches, and architectural finishes, where maintaining the original color and appearance is crucial.
-
Environmental and Cost Benefits
- PVD is an environmentally friendly process, as it does not involve harmful chemicals or produce significant waste.
- The process is cost-effective for both high-volume production and small-batch manufacturing, reducing production costs and turnaround times.
-
Versatility in Applications
- PVD is suitable for a wide range of industries, including automotive, aerospace, medical devices, and cutting tools.
- Its ability to coat various materials, such as metals, ceramics, and composites, makes it a versatile solution for diverse applications.
-
Improved Performance in Cutting Tools
- PVD coatings are thinner (3~5μm) compared to other methods, preserving the sharpness of cutting tools and reducing cutting force and heat.
- This makes PVD-coated tools ideal for interrupted cutting processes, such as milling, where durability and precision are critical.
-
Computer-Controlled Precision
- Modern PVD coating machines are computer-controlled, allowing operators to multitask and achieve consistent results.
- This automation enhances efficiency and reduces human error, making PVD a reliable choice for industrial applications.
-
Increased Product Lifespan
- PVD coatings significantly enhance the lifespan of products by improving their wear resistance, corrosion resistance, and overall durability.
- This results in reduced maintenance costs and longer service life, providing long-term value to manufacturers and end-users.
In summary, Physical Vapor Deposition (PVD) offers a combination of technical, economic, and environmental benefits, making it a preferred coating technology for a wide range of industries. Its ability to produce high-quality, durable, and aesthetically pleasing coatings ensures its continued relevance in modern manufacturing and decorative applications.
Summary Table:
Advantage | Description |
---|---|
High-Quality Thin Films | Precise control over coating thickness (0.02-5μm) for uniformity and consistency. |
Lower Process Temperatures | Operates at ~500°C, minimizing thermal damage to heat-sensitive materials. |
Enhanced Durability | High hardness and wear resistance, ideal for cutting tools and industrial components. |
Corrosion Resistance | Protects substrates from harsh environments, suitable for automotive and aerospace applications. |
Aesthetic Applications | Replicates expensive metals for cost-effective decorative uses in jewelry and watches. |
Environmental and Cost Benefits | Eco-friendly, cost-effective for high-volume and small-batch production. |
Versatility | Suitable for metals, ceramics, and composites across multiple industries. |
Improved Cutting Tool Performance | Thin coatings (3~5μm) preserve sharpness and reduce cutting force and heat. |
Computer-Controlled Precision | Automated process ensures consistency and efficiency. |
Increased Product Lifespan | Enhances wear and corrosion resistance, reducing maintenance costs and extending service life. |
Unlock the full potential of PVD coatings for your industry—contact our experts today to learn more!