Powder metallurgy sintering is a highly efficient and versatile manufacturing process that offers numerous advantages, making it a preferred choice for producing complex and high-performance components. Key benefits include energy efficiency, cost-effectiveness, and the ability to produce parts with exceptional precision and uniformity. The process is environmentally friendly, with minimal material waste, and is particularly suited for materials with high melting points or poor castability. Additionally, sintering enhances material properties, such as strength and durability, while allowing for the creation of intricate shapes and structures tailored to specific requirements.
Key Points Explained:
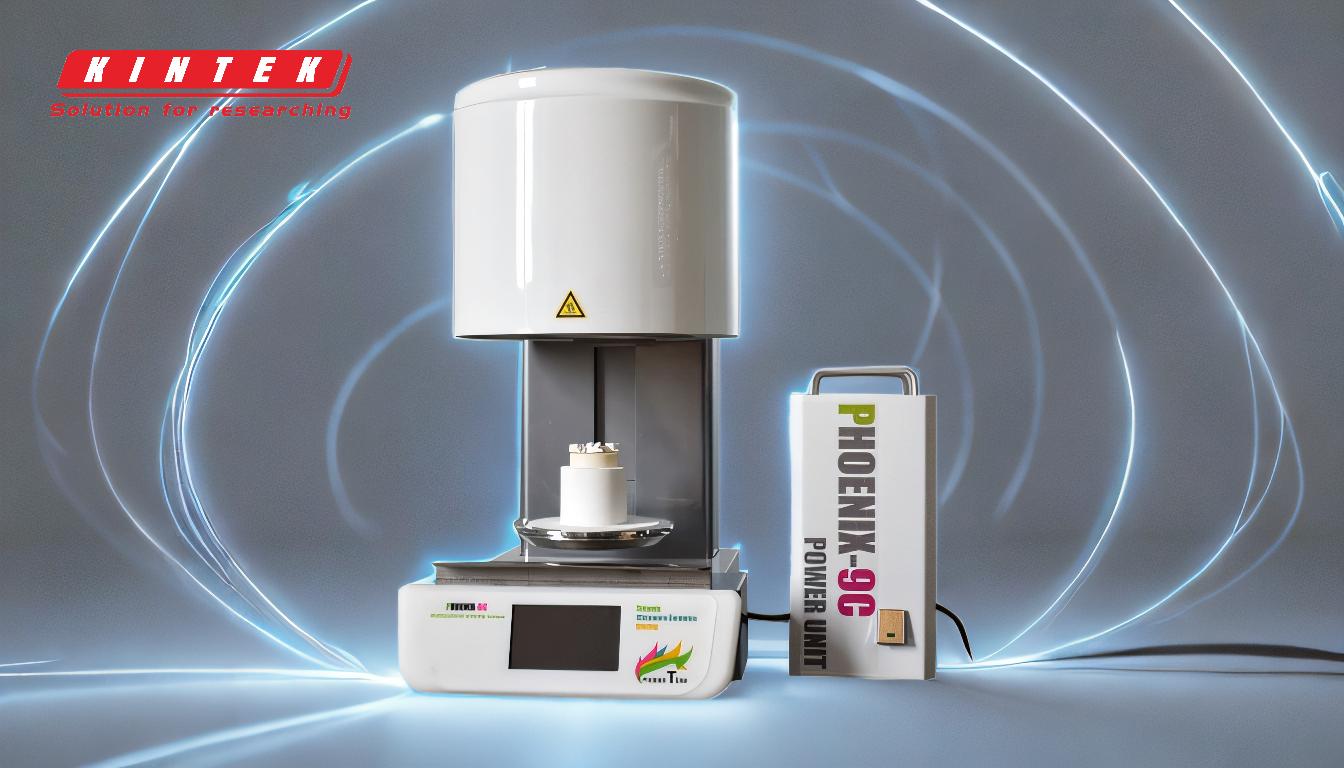
-
Energy Efficiency and Low Process Temperature:
- Powder metallurgy sintering operates at lower temperatures compared to traditional melting processes, reducing energy consumption. This makes it an environmentally friendly option, especially for materials with high melting points.
- The lower process temperature also minimizes thermal stress and distortion in the final product, ensuring better dimensional accuracy.
-
High Sintering Compactness and Material Utilization:
- Sintering results in high-density parts with minimal porosity, enhancing the mechanical properties of the final product, such as strength and durability.
- The process is highly efficient, with up to 97% of the material used becoming part of the final product, significantly reducing waste and material costs.
-
Short Sintering Time and Process Efficiency:
- The sintering process is relatively quick, allowing for faster production cycles compared to traditional manufacturing methods.
- This short processing time, combined with the ability to produce near-net-shape parts, reduces the need for additional machining, saving time and resources.
-
Ability to Produce Complex and Intricate Shapes:
- Powder metallurgy sintering enables the creation of highly complex external and internal geometries with exceptional precision. This is achieved through the use of molds and dies made by wire EDM (Electrical Discharge Machining) with centesimal tolerances.
- This capability is particularly valuable in industries like automotive and aerospace, where intricate and lightweight components are essential.
-
Tailored Material Properties and Versatility:
- The process allows for the precise control of material composition and structure, enabling the production of parts with customized properties to meet specific application requirements.
- It is particularly beneficial for materials with large differences in melting points or poor castability, as it avoids the challenges associated with traditional melting and casting processes.
-
Cost-Effectiveness and Economic Benefits:
- Powder metallurgy sintering reduces material waste and eliminates the need for extensive machining, lowering overall production costs.
- The ability to produce parts with high precision and consistency reduces the likelihood of defects, further enhancing cost savings and product reliability.
-
Environmental Friendliness:
- The process generates minimal waste and requires less energy compared to traditional manufacturing methods, making it a sustainable choice for modern manufacturing.
- Its eco-friendly nature aligns with the growing demand for green manufacturing technologies.
-
Improved Strength and Durability:
- Sintering minimizes surface porosity, resulting in parts with enhanced mechanical properties, such as higher strength and wear resistance.
- This makes sintered components suitable for demanding applications where durability and performance are critical.
-
Wide Range of Applications:
- Powder metallurgy sintering is widely used in industries such as automotive, aerospace, electronics, and medical devices due to its ability to produce high-quality, precision components.
- Its versatility and adaptability make it a key technology for modern manufacturing.
In summary, powder metallurgy sintering offers a combination of technical, economic, and environmental advantages, making it a highly effective and sustainable manufacturing process. Its ability to produce complex, high-performance parts with minimal waste and energy consumption positions it as a cornerstone of advanced manufacturing technologies.
Summary Table:
Advantage | Description |
---|---|
Energy Efficiency | Operates at lower temperatures, reducing energy consumption and thermal stress. |
High Sintering Compactness | Produces high-density parts with minimal porosity and enhanced strength. |
Short Sintering Time | Faster production cycles and reduced need for additional machining. |
Complex Shapes | Enables intricate geometries with exceptional precision. |
Tailored Material Properties | Customizes material composition for specific application needs. |
Cost-Effectiveness | Reduces material waste and machining costs. |
Environmental Friendliness | Minimal waste and energy use, aligning with green manufacturing. |
Improved Strength and Durability | Enhances mechanical properties like wear resistance. |
Wide Range of Applications | Used in automotive, aerospace, electronics, and medical industries. |
Unlock the potential of powder metallurgy sintering for your manufacturing needs—contact our experts today!