Physical Vapor Deposition (PVD) is a coating method that offers numerous advantages, particularly in terms of durability, environmental friendliness, and versatility. PVD coatings are known for their hardness, corrosion resistance, and ability to withstand high temperatures and impacts. They are also highly resistant to abrasion, often eliminating the need for additional protective topcoats. Additionally, PVD can be applied to a wide variety of substrates and materials, making it a flexible solution for many industries. Compared to traditional coating methods like electroplating, PVD is often more environmentally friendly and produces coatings with superior performance characteristics.
Key Points Explained:
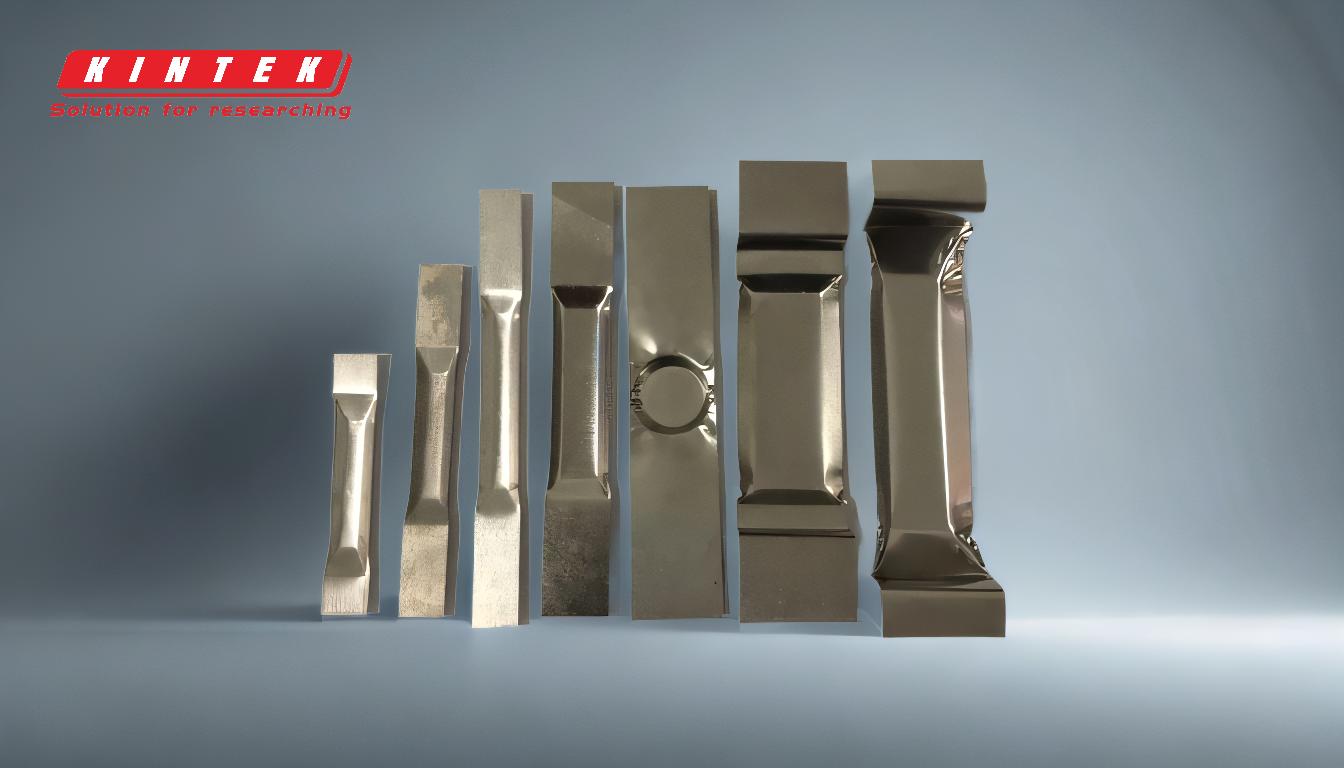
-
Enhanced Durability and Performance:
- PVD coatings are harder and more corrosion-resistant than those applied by traditional methods like electroplating.
- They exhibit excellent abrasion resistance and high impact strength, making them ideal for applications requiring long-lasting protection.
- Due to their durability, protective topcoats are rarely necessary, reducing additional processing steps and costs.
-
High-Temperature Resistance:
- PVD coatings can withstand high temperatures, making them suitable for applications in harsh environments, such as aerospace or automotive industries.
- This property ensures that the coatings maintain their integrity and performance even under extreme conditions.
-
Versatility in Material and Substrate Compatibility:
- PVD can utilize a wide range of inorganic and some organic coating materials, providing flexibility in meeting specific application requirements.
- It can be applied to diverse substrates, including metals, ceramics, and plastics, making it a versatile choice for various industries.
-
Environmental Friendliness:
- PVD processes are often more environmentally friendly compared to traditional coating methods like electroplating and painting.
- They produce fewer harmful byproducts and waste, aligning with modern sustainability goals.
-
Precision and Efficiency:
- PVD allows for precise control over the coating process, ensuring consistent quality and performance.
- The method is efficient and can be tailored to specific needs, reducing material waste and improving cost-effectiveness.
-
Comparison with Short Path Vacuum Distillation:
- While PVD focuses on coating applications, short path vacuum distillation is a method used for separating compounds at lower temperatures, preserving the integrity of heat-sensitive materials.
- Both methods leverage vacuum conditions to enhance performance—PVD for coating durability and short path distillation for maintaining compound purity.
By leveraging these advantages, PVD stands out as a superior coating method for industries requiring high-performance, durable, and environmentally friendly solutions. Its ability to adapt to various materials and substrates further enhances its appeal across a broad spectrum of applications.
Summary Table:
Advantage | Description |
---|---|
Enhanced Durability | Harder, corrosion-resistant, abrasion-resistant, and impact-resistant coatings. |
High-Temperature Resistance | Maintains integrity and performance in extreme conditions. |
Versatility | Compatible with metals, ceramics, plastics, and various coating materials. |
Environmental Friendliness | Fewer harmful byproducts and waste compared to traditional methods. |
Precision and Efficiency | Consistent quality, reduced material waste, and cost-effectiveness. |
Unlock the full potential of PVD coatings for your industry—contact our experts today!