Sintered metal offers several advantages that make it a preferred choice over traditional metal fabrication methods. These benefits include cost-effectiveness, increased control over material properties, reproducibility, improved mechanical properties, and the ability to create complex shapes and designs.
What are the advantages of sintered metal? (5 Key Benefits)
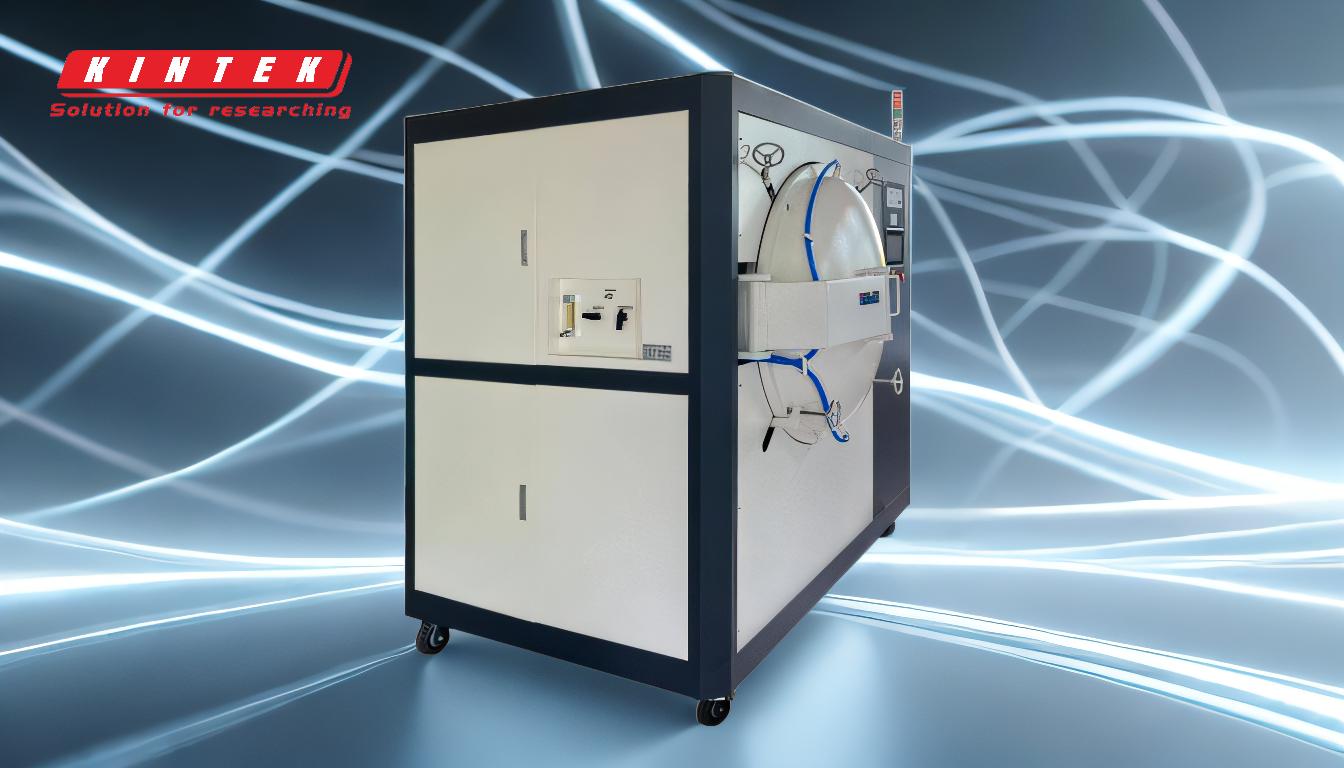
1. Cost-effectiveness
Sintering is a more cost-effective method of metal fabrication compared to traditional methods like stamping, cutting, and casting.
This is primarily because sintering produces less waste and requires less energy.
The process involves compacting metal powders at high pressure and then heating them to a temperature below the melting point, which results in a solid structure with minimal material loss.
This reduction in waste material directly translates to lower costs for materials and disposal.
2. Increased control
Sintering allows for the binding of materials with different melting points, including very high ones, without melting the metal entirely.
This process control enables the fine-tuning of the sintering process to achieve more consistent and precise results.
The ability to manipulate the heating and cooling rates, as well as the pressure applied during compaction, allows for the creation of parts with specific mechanical and physical properties.
3. Reproducible size and hardness
Due to the high degree of control in the sintering process, it is easier to consistently reproduce parts with the same size and hardness.
This reproducibility is crucial in industries where parts must meet strict specifications, such as in automotive or aerospace manufacturing.
4. Improved mechanical properties
Sintering enhances the mechanical properties of materials, leading to components with superior performance characteristics.
During sintering, particles bond and densify, improving strength, hardness, and wear resistance.
The controlled heating and diffusion mechanisms contribute to the development of a dense and cohesive structure, enhancing the overall mechanical integrity of the component.
5. Complex shapes and intricate designs
Sintering can produce components with complex shapes and intricate designs that would be difficult to achieve with traditional machining techniques.
This is possible because sintering starts with powdered materials, which can be easily shaped into complex geometries before being sintered into a solid form.
This capability is particularly beneficial in industries that require customized components for specific applications.
Continue exploring, consult our experts
Experience the Future of Metal Fabrication with KINTEK SOLUTION. Unlock the full potential of sintered metal and revolutionize your production process.
From unparalleled cost-effectiveness to the ability to create intricate designs, our sintered metal solutions are the answer for high-performance, precision components.
Join the ranks of leading industries that trust KINTEK SOLUTION for consistent quality and unmatched technical expertise.
Contact us today and let's transform your metalwork.