Physical Vapor Deposition (PVD) and Chemical Vapor Deposition (CVD) are two widely used thin-film deposition techniques, each with distinct advantages and limitations. PVD is favored for its environmental friendliness, as it does not require chemical reagents or post-treatment cleaning, and it offers excellent adhesion, resistance, and durability of coatings. It also allows precise control over composition and thickness. In contrast, CVD excels in coating complex geometries, offers high deposition rates, and does not require ultra-high vacuum conditions. However, PVD operates at lower temperatures and avoids corrosive byproducts, making it suitable for temperature-sensitive substrates. The choice between PVD and CVD depends on specific application requirements, such as material compatibility, deposition temperature, and desired film properties.
Key Points Explained:
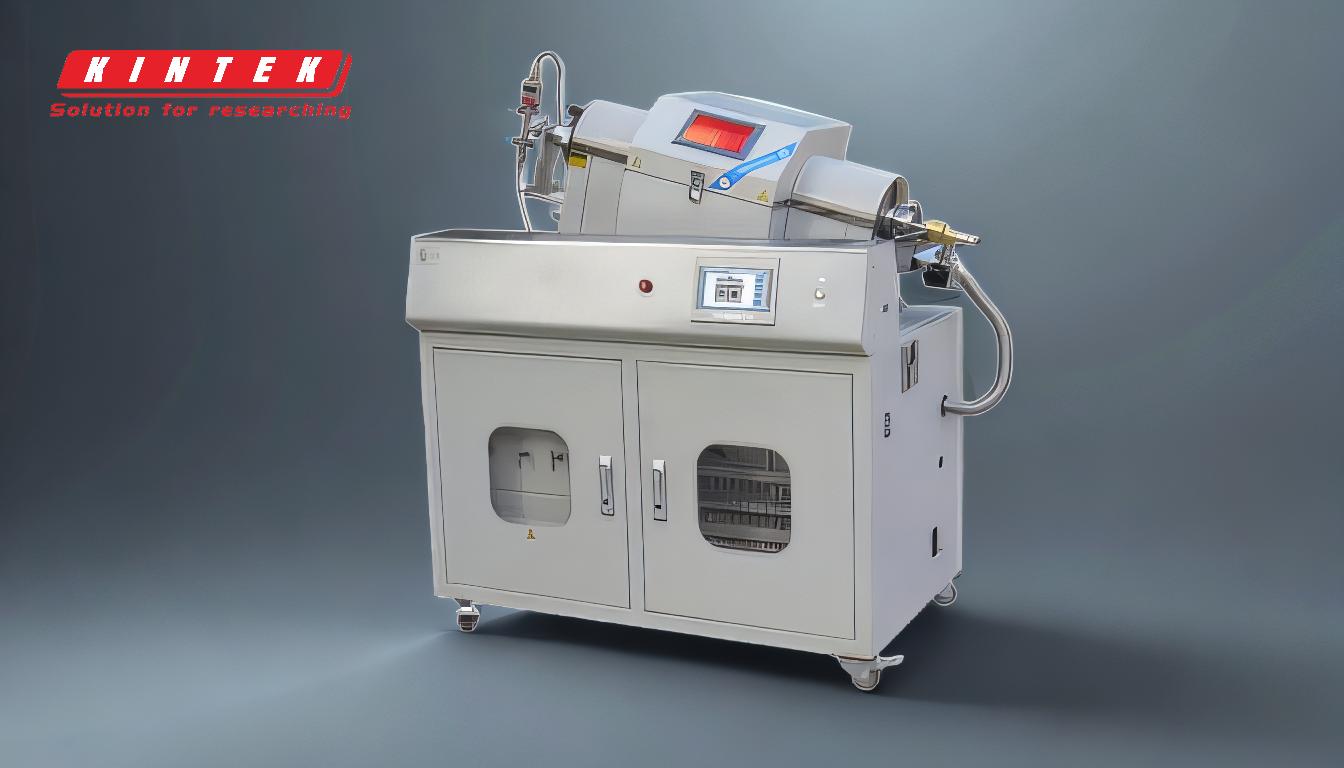
-
Environmental Impact and Cleanliness:
- PVD does not involve chemical reagents, reducing the need for post-treatment cleaning and minimizing environmental impact.
- CVD, on the other hand, often requires chemical precursors and can produce corrosive gaseous byproducts, which may require additional handling and disposal measures.
-
Material Compatibility:
- PVD can be applied to a wide range of inorganic materials, making it versatile for various applications.
- CVD also supports a broad range of materials, including metals, semiconductors, and ceramics, but it is particularly advantageous for coating complex shapes and deep recesses due to its non-line-of-sight deposition capability.
-
Deposition Temperature:
- PVD operates at lower temperatures (250°C~450°C), which is beneficial for temperature-sensitive substrates.
- CVD typically requires higher temperatures (450°C to 1050°C), which can limit its use with certain materials but is advantageous for achieving high-quality, uniform films.
-
Film Properties and Control:
- PVD offers excellent adhesion, resistance, and durability of coatings, with precise control over composition and thickness.
- CVD provides high precision in controlling film thickness, composition, and microstructure, enabling the production of films with specific properties. It also offers high deposition rates and uniformity across the substrate surface.
-
Economic Considerations:
- CVD is often more economical due to its high deposition rates and ability to produce thick coatings, making it suitable for large-scale industrial applications.
- PVD, while potentially more costly due to the need for sophisticated equipment and cleanroom facilities, offers advantages in terms of material utilization efficiency and lower operational temperatures.
-
Application-Specific Advantages:
- PVD is particularly suitable for applications requiring high-purity films and low-temperature processing, such as in the electronics and optics industries.
- CVD is preferred for applications involving complex geometries and high-throughput production, such as in the semiconductor and coating industries.
In summary, the choice between PVD and CVD depends on the specific requirements of the application, including material compatibility, deposition temperature, film properties, and economic considerations. PVD offers advantages in terms of environmental impact, lower deposition temperatures, and precise control over film properties, while CVD excels in coating complex geometries, high deposition rates, and economic scalability. For more specialized applications, techniques like microwave plasma chemical vapor deposition can offer additional benefits, particularly in achieving high-quality films with specific properties.
Summary Table:
Aspect | PVD Advantages | CVD Advantages |
---|---|---|
Environmental Impact | No chemical reagents; minimal post-treatment cleaning | Requires chemical precursors; may produce corrosive byproducts |
Material Compatibility | Versatile for inorganic materials | Supports metals, semiconductors, ceramics; excels in complex geometries |
Deposition Temperature | Lower temperatures (250°C~450°C); suitable for sensitive substrates | Higher temperatures (450°C~1050°C); ideal for high-quality, uniform films |
Film Properties | Excellent adhesion, resistance, durability; precise control over composition | High precision in thickness, composition, and microstructure; high deposition rates |
Economic Considerations | Higher initial costs; efficient material utilization | Economical for large-scale production; high deposition rates |
Applications | Electronics, optics (high-purity films, low-temperature processing) | Semiconductor, coating industries (complex geometries, high-throughput production) |
Need help choosing between PVD and CVD for your application? Contact our experts today for tailored advice!