Vacuum induction melting (VIM) offers numerous advantages, making it a preferred method for producing high-quality alloys and metals. The process involves melting metals in a vacuum environment using electromagnetic induction, which eliminates contamination from gases and impurities. Key benefits include improved material purity, precise control over alloy composition, reduced oxidation, and enhanced environmental protection. Additionally, VIM ensures efficient removal of harmful elements and gases, leading to superior mechanical properties and performance of the final product. The process also features advanced safety mechanisms, energy efficiency, and the ability to produce homogeneous and defect-free materials.
Key Points Explained:
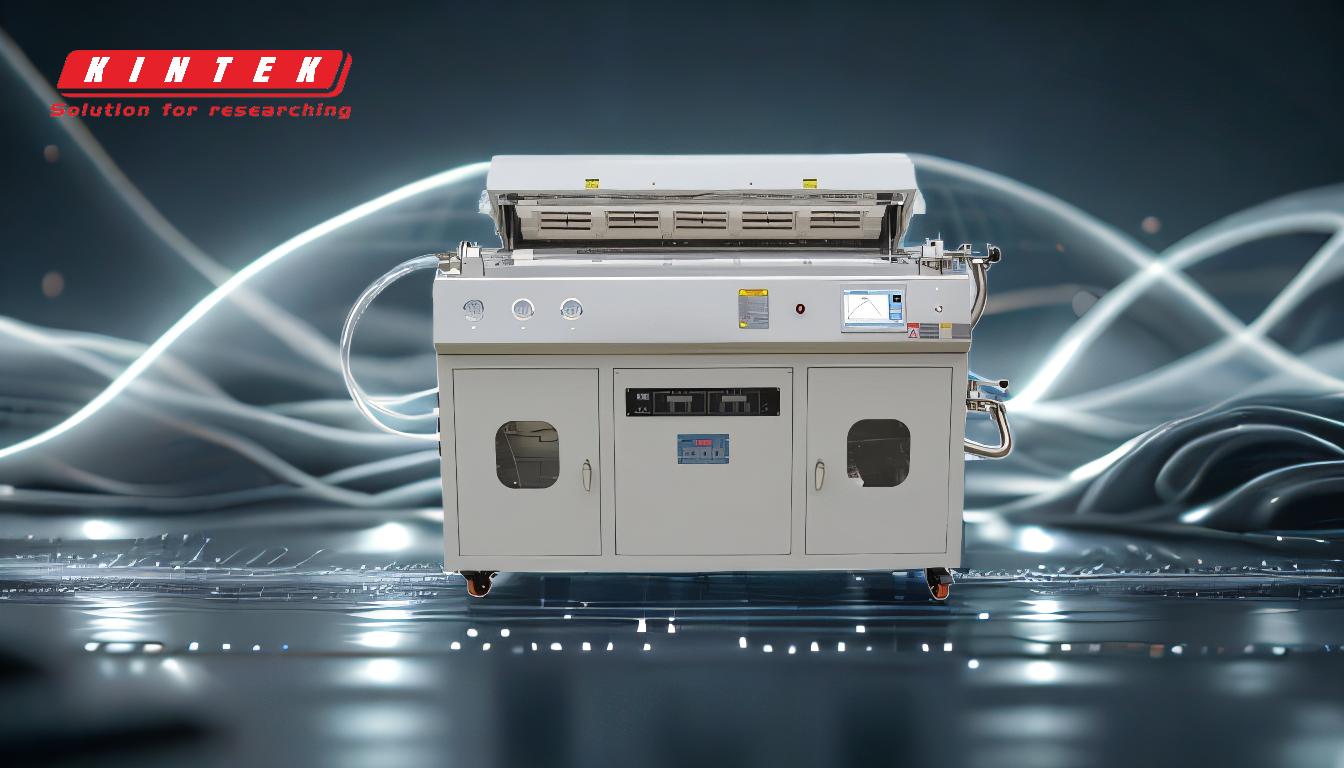
-
Enhanced Material Purity and Performance
- Vacuum induction melting takes place in a vacuum environment, which prevents gas-phase interactions and contamination. This results in purer alloys with fewer impurities.
- The process effectively removes low-melting-point volatile metal impurities (e.g., Pb, Bi, Sb, Cu, Sn, and Te) and harmful dissolved gases (e.g., O2, N2, and H2), significantly improving material performance.
- The absence of oxidation and slag pollution ensures the production of high-quality alloys with superior mechanical properties.
-
Precise Control Over Alloy Composition
- VIM allows for precise control of alloy composition, especially for reactive elements like aluminum, titanium, boron, and zirconium.
- The process minimizes the burning of alloying elements, ensuring consistent and accurate chemical composition in the final product.
- This level of control is critical for producing specialized alloys used in aerospace, medical, and high-performance industrial applications.
-
Reduction of Harmful Elements and Gases
- The vacuum environment facilitates the removal of undesirable elements such as hydrogen and nitrogen, which can degrade material properties.
- High-vapor-pressure metal impurities (e.g., copper, zinc, lead, antimony, bismuth, tin, and arsenic) are effectively eliminated during the melting process.
- This results in alloys with low gas content and improved resistance to defects like porosity and brittleness.
-
Electromagnetic Stirring for Homogeneity
- The electromagnetic induction process creates electrodynamic circulation of the molten metal, promoting uniformity in composition and temperature.
- This stirring action helps merge and uplift non-metallic inclusions, leading to a more homogeneous and defect-free final product.
-
Environmental and Operational Benefits
- VIM is a nearly flame-free process, producing minimal combustion products and environmental pollution.
- The use of a vacuum melting furnace reduces heat loss and improves energy efficiency.
- Advanced safety features, such as over-temperature, over-pressure, and under-voltage alarms, ensure safe and reliable operation.
-
Energy Efficiency and Advanced Technology
- The vacuum pump used in VIM is energy-efficient, with low noise levels and a high pumping rate.
- Specialized coil designs ensure long life and resistance to deformation, reducing maintenance costs.
- The frequency conversion rotary casting device allows for precise control of pouring speed, enabling the production of multiple molds with consistent quality.
-
Improved High-Temperature Alloy Performance
- VIM significantly increases the maximum operating temperature of high-temperature alloys, from 750-810 ℃ to 980-1090 ℃.
- This enhancement is achieved by reducing gap elements and completely removing non-metallic inclusions, making the alloys suitable for extreme conditions.
-
Versatility and Adaptability
- The vacuum induction melting process can be used for a wide range of metals and alloys, including those with reactive and volatile elements.
- Its adaptability makes it ideal for producing materials for advanced applications, such as turbine blades, medical implants, and aerospace components.
By leveraging the advantages of vacuum induction melting, manufacturers can produce high-performance materials with exceptional purity, consistency, and reliability. The process not only improves material properties but also aligns with modern environmental and operational standards. For more details on the technology, you can explore the vacuum melting furnace.
Summary Table:
Advantage | Description |
---|---|
Enhanced Material Purity | Removes impurities and harmful gases, producing high-quality alloys. |
Precise Alloy Composition Control | Ensures accurate chemical composition for specialized applications. |
Reduction of Harmful Elements | Eliminates undesirable elements like hydrogen and nitrogen. |
Electromagnetic Stirring | Promotes uniform composition and defect-free materials. |
Environmental Benefits | Minimizes pollution and improves energy efficiency. |
Energy Efficiency | Features energy-efficient vacuum pumps and advanced coil designs. |
High-Temperature Alloy Performance | Increases operating temperature for extreme conditions. |
Versatility | Suitable for a wide range of metals and advanced applications. |
Ready to enhance your alloy production? Contact us today to learn more about vacuum induction melting!