Temperature control systems are essential in a wide range of applications, ensuring precise temperature regulation, energy efficiency, and process stability. They are widely used in HVAC systems to maintain comfortable indoor environments, in refrigeration to preserve perishable goods, in ovens for consistent cooking or industrial heating, and in process control systems to optimize manufacturing and chemical processes. These systems help minimize energy consumption, prevent temperature fluctuations, and ensure safety and quality in various industries. Below, we explore the key applications and benefits of temperature control systems in detail.
Key Points Explained:
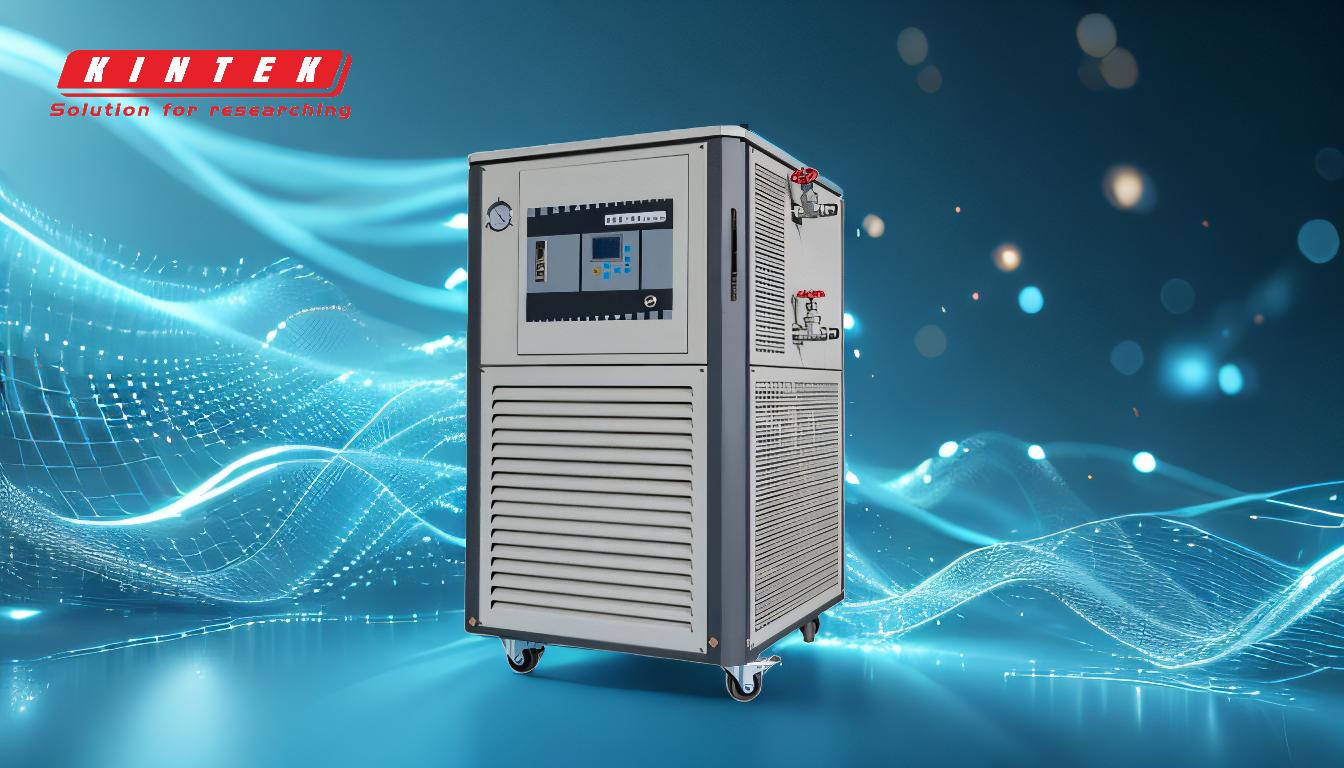
-
HVAC Systems:
- Purpose: Temperature control systems are integral to Heating, Ventilation, and Air Conditioning (HVAC) systems, ensuring optimal indoor climate conditions.
- Functionality: They regulate heating and cooling to maintain consistent temperatures, improving comfort and energy efficiency.
-
Benefits:
- Energy savings by preventing unnecessary heating or cooling.
- Enhanced comfort through precise temperature management.
- Improved air quality by maintaining stable environmental conditions.
-
Refrigeration:
- Purpose: Temperature control is critical in refrigeration systems to preserve perishable goods, such as food, pharmaceuticals, and chemicals.
- Functionality: These systems maintain low temperatures within a narrow range to prevent spoilage and ensure product integrity.
-
Benefits:
- Extended shelf life of perishable items.
- Compliance with safety and regulatory standards.
- Reduced energy consumption through efficient temperature regulation.
-
Ovens and Industrial Heating:
- Purpose: Temperature control systems are used in ovens for cooking, baking, and industrial heating processes.
- Functionality: They ensure consistent and accurate temperatures, which are crucial for achieving desired outcomes in food preparation or material processing.
-
Benefits:
- Consistent product quality in cooking or manufacturing.
- Energy efficiency by avoiding overheating or underheating.
- Prevention of damage to materials or food due to temperature fluctuations.
-
Process Control Systems:
- Purpose: Temperature control is vital in industrial and chemical processes where precise temperature regulation is required.
- Functionality: These systems monitor and adjust temperatures in real-time to optimize production processes and ensure safety.
-
Benefits:
- Enhanced product quality and consistency.
- Improved safety by preventing overheating or hazardous conditions.
- Energy savings through efficient process control.
-
Energy Efficiency and Cost Savings:
- Purpose: Temperature control systems are designed to minimize energy usage while maintaining precise temperature regulation.
- Functionality: They use advanced algorithms and sensors to optimize heating and cooling cycles.
-
Benefits:
- Reduced operational costs through lower energy consumption.
- Longer equipment lifespan due to reduced strain on components.
- Environmental benefits from lower energy usage.
-
Preventing Temperature Fluctuations:
- Purpose: Temperature control systems prevent overshooting or undershooting of desired temperatures, which can be critical in sensitive applications.
- Functionality: They use feedback mechanisms to adjust heating or cooling in real-time.
-
Benefits:
- Improved process stability and product quality.
- Prevention of damage or spoilage due to temperature variations.
- Enhanced safety in critical applications.
In summary, temperature control systems are indispensable in a variety of applications, from HVAC and refrigeration to industrial processes and ovens. They provide precise temperature regulation, energy efficiency, and process stability, making them a critical component in ensuring quality, safety, and cost-effectiveness across industries.
Summary Table:
Application | Purpose | Benefits |
---|---|---|
HVAC Systems | Maintain optimal indoor climate conditions | Energy savings, enhanced comfort, improved air quality |
Refrigeration | Preserve perishable goods like food and pharmaceuticals | Extended shelf life, compliance with safety standards, reduced energy usage |
Ovens & Industrial Heating | Ensure consistent temperatures for cooking or material processing | Consistent quality, energy efficiency, prevention of damage |
Process Control Systems | Optimize manufacturing and chemical processes | Enhanced product quality, improved safety, energy savings |
Energy Efficiency | Minimize energy usage while maintaining precise temperature regulation | Reduced operational costs, longer equipment lifespan, environmental benefits |
Preventing Fluctuations | Prevent overshooting or undershooting of desired temperatures | Improved process stability, prevention of spoilage, enhanced safety |
Ready to optimize your processes with advanced temperature control systems? Contact us today to learn more!